Together with experts from the world of science, we had the opportunity to participate in Warsaw Industry Automatica, organized between 14 and 15 May 2024. The event at EXPO Warsaw, the largest exhibition center in Poland, was a great opportunity to establish business relationships in central and eastern Europe and attend the trade fair connected with the Automation Industry Conference 2024. This year there wasn't any outdoor space with industrial equipment but still, the event was very impressive.
See our outcomes from the fairs and conference, which shed more light on the current developments in automation and robotics in the manufacturing industry, supply chain, and inventory management with modern systems that streamline operations across multiple locations.

Expo Warsaw: innovation meets practical demand
We had an amazing opportunity to visit the latest industry event in Warsaw. The venue created by EXPO was keeping ahead with industry trends at the trade fairs in Central and Eastern Europe, we want to follow current developments in robotics and automation as closely as possible.
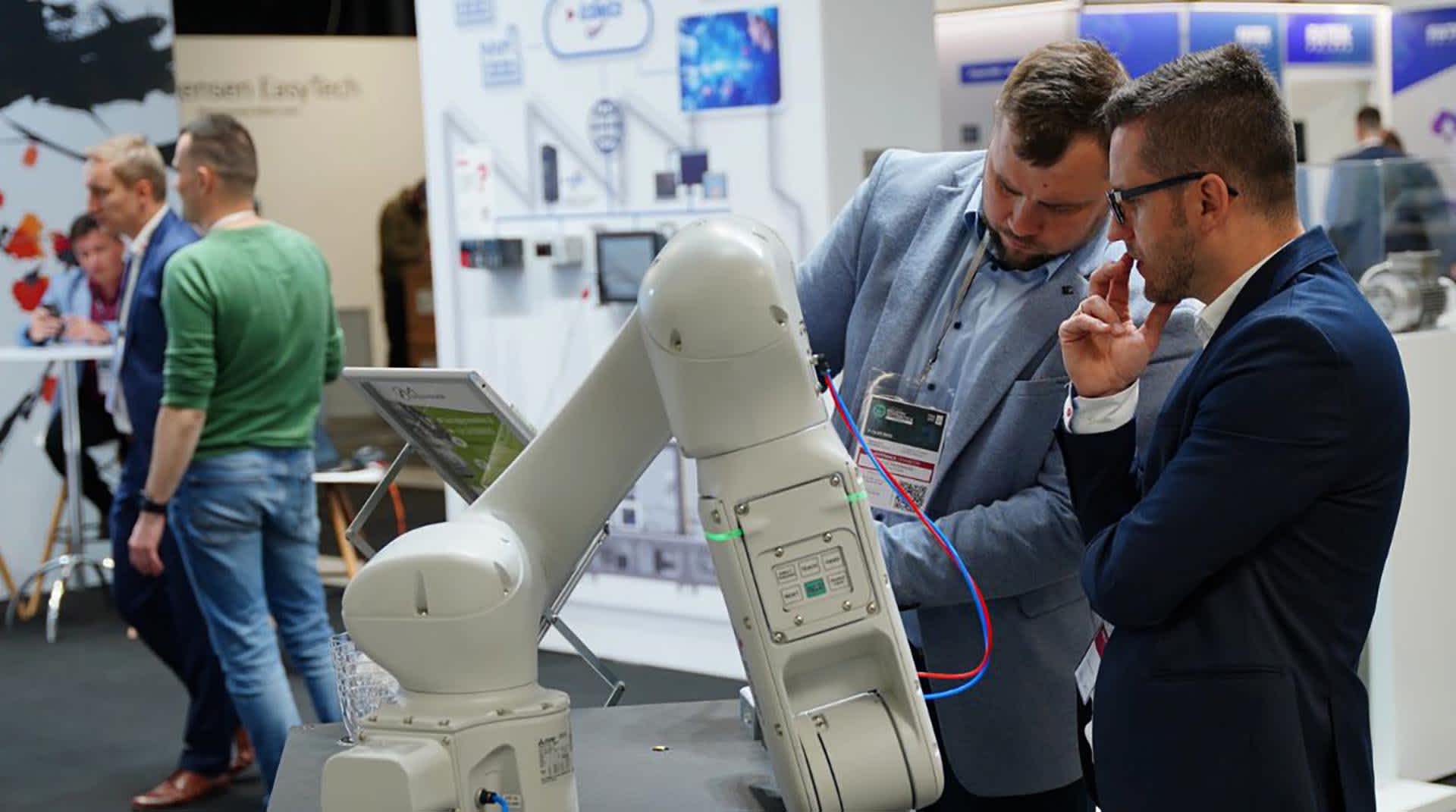
What about this year's edition?
This year's event edition, Warsaw Industry Automatica, has attracted nearly 10K visitors from various industries. Relying on the details from the previous edition, the number of visitors has reached nearly 2K from abroad, spanning 14 countries. These are very good results that highlight the value of the entire exhibition space.
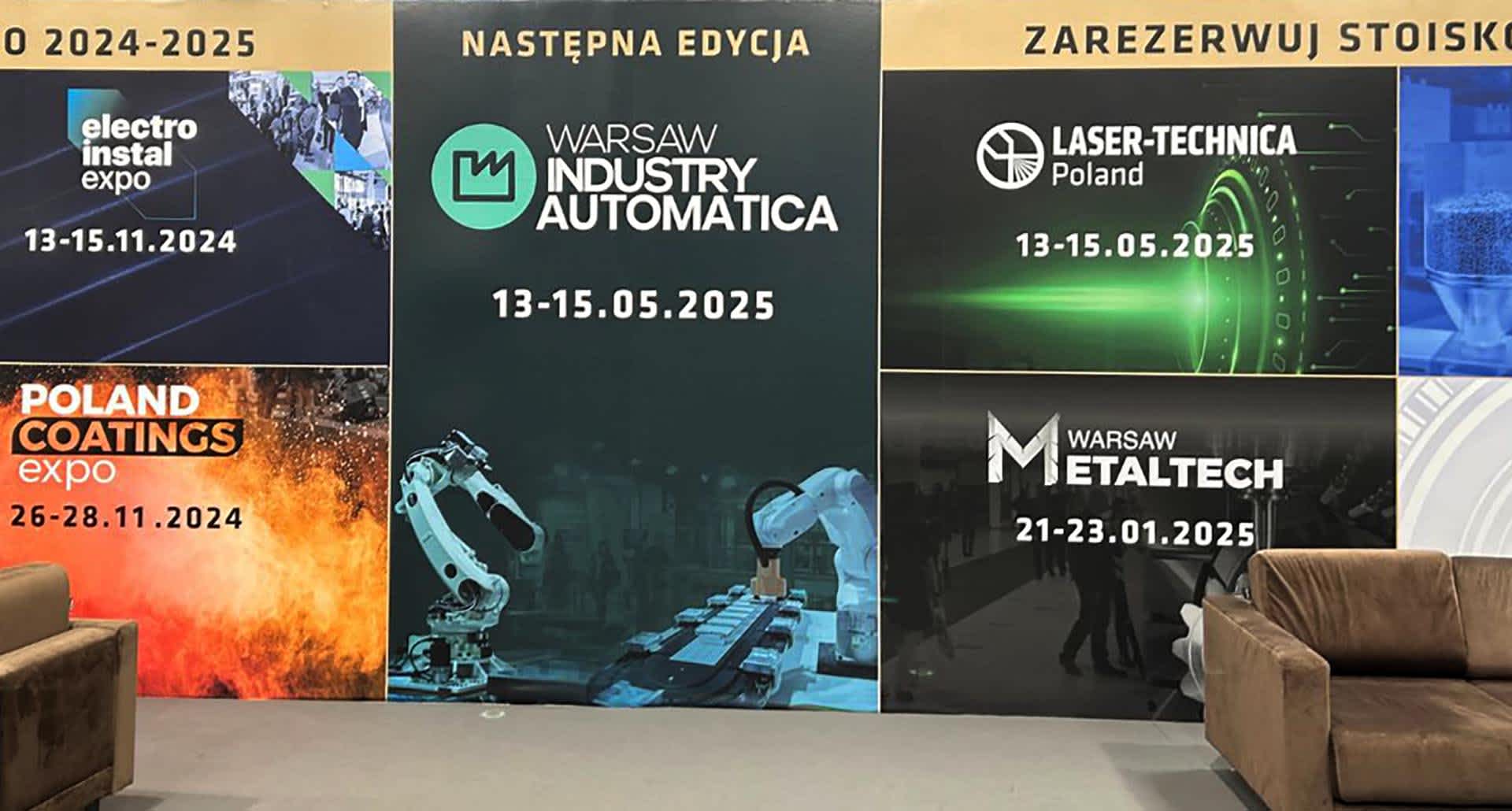
Do you know the main subject of and what the fair offers?
The main subject of the event was robotics and automation. Nevertheless, we had the opportunity to talk with many companies from the software industry. It gave us brilliant insights into where the software market stands in the area of manufacturing. But I will tell you more about this experience later in this article.
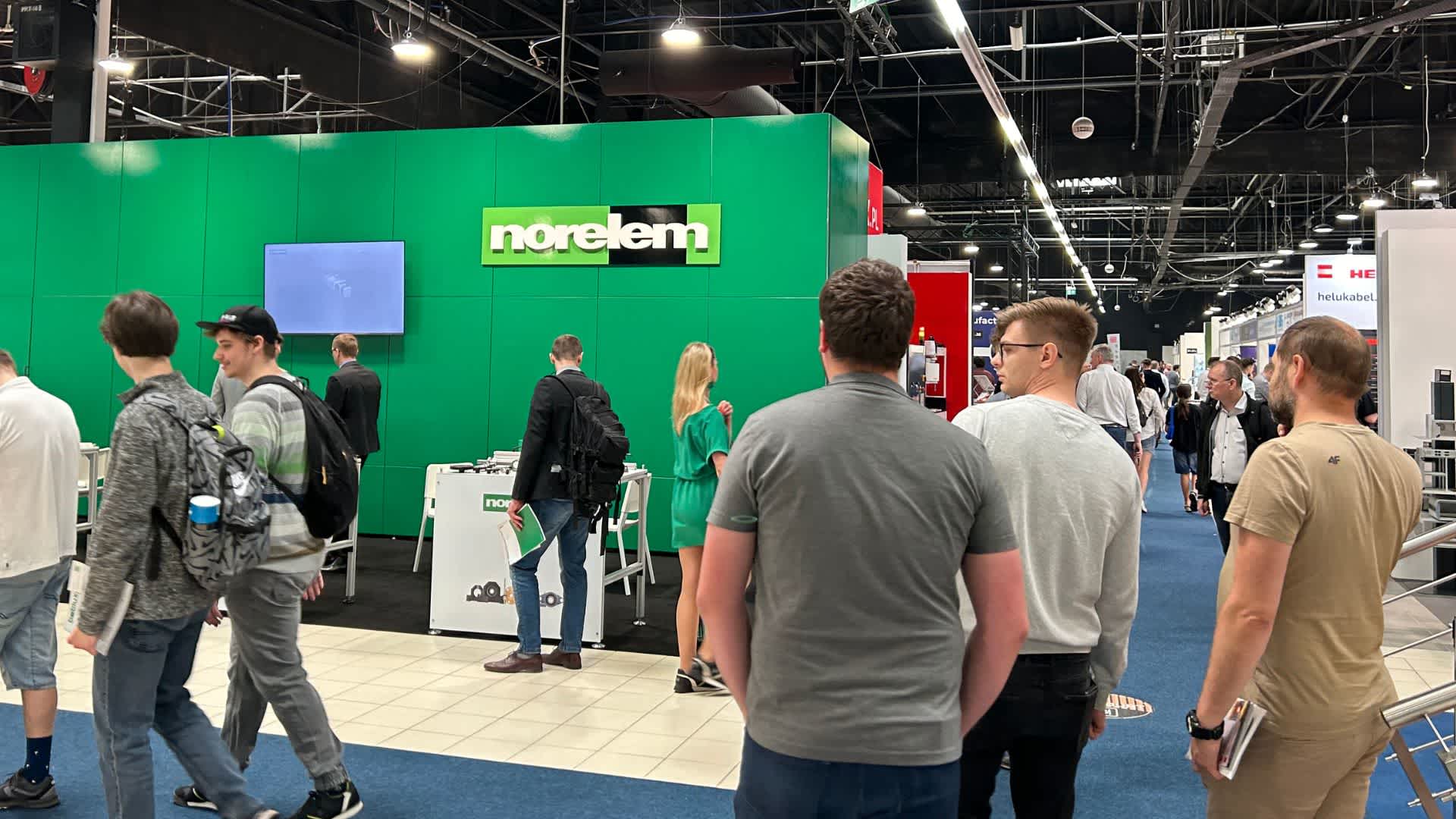
Exhibition space in Warsaw & Automation Industry Conference 2024
This year's edition organizer PTAK Warsaw Expo divided into two conferences, where keynotes from well-known businesses in European heavy industry, technology, robotics, custom software for service and maintenance, or internal logistics management with an inventory management system. Moreover, a significant number of providers of ready-made solutions for Business Process Management had the excellent opportunity to reach a broad audience.
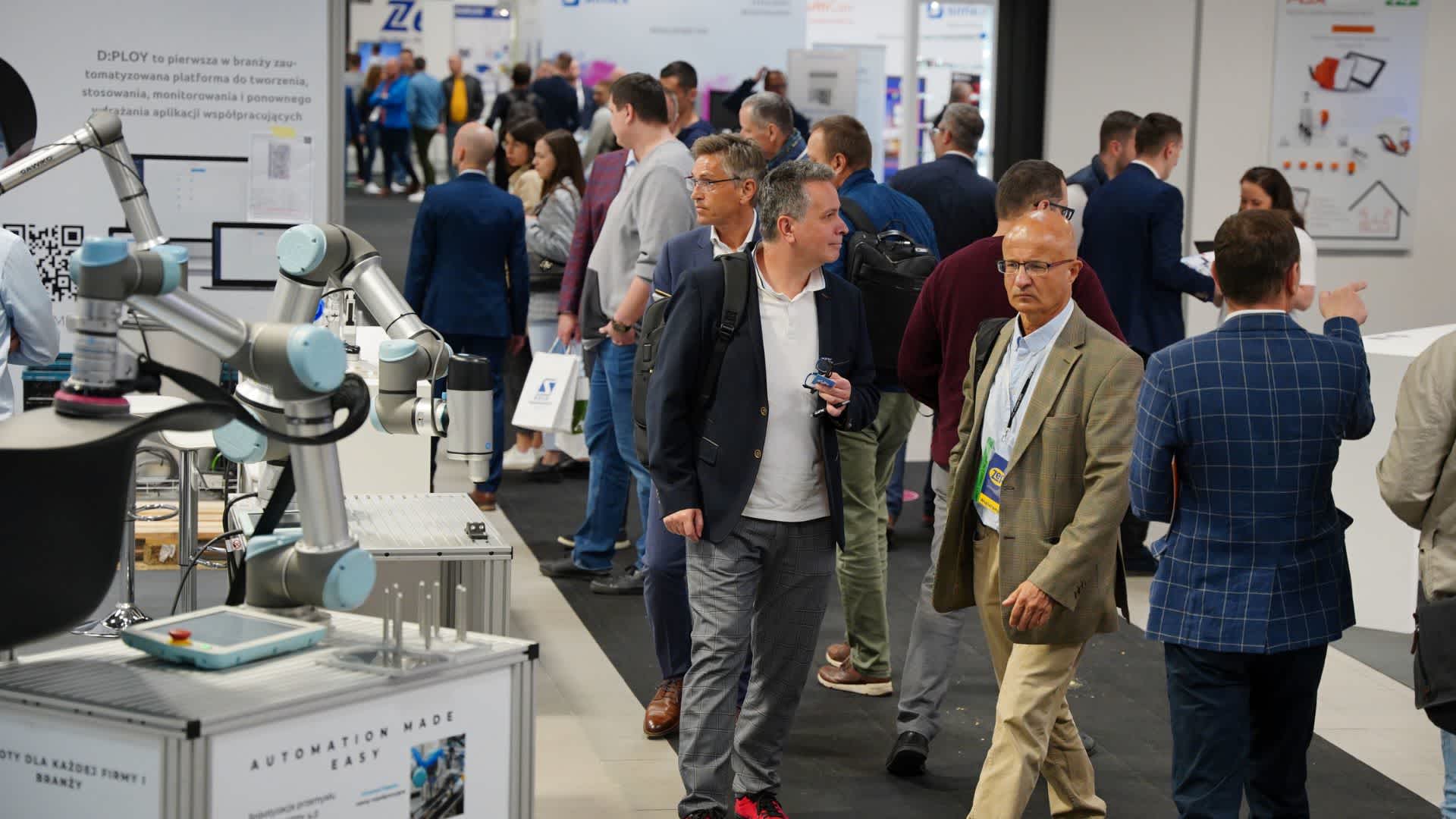
Automation and robotization in the world of Industry 4.0
During this part of the conference, technical experts from leading companies in the field of automation and robotics were highly appreciated, and critical topics related to technological advances, standards, and regulations were addressed. The conference program was divided into three thematic blocks. Each one was focusing on different aspects of industrial challenges and solutions.
1. Communication standards in industrial automation
The first block of presentations focuses on contemporary and forward-looking communication standards in industrial automation. Speakers discussed the latest trends in industrial communication. They also discussed the implementation of Time-Sensitive Networking (TSN) as a core technology for real-time communication. At this point, it was very important to discuss the industry's anticipated impact of 5G on automation and robotization.
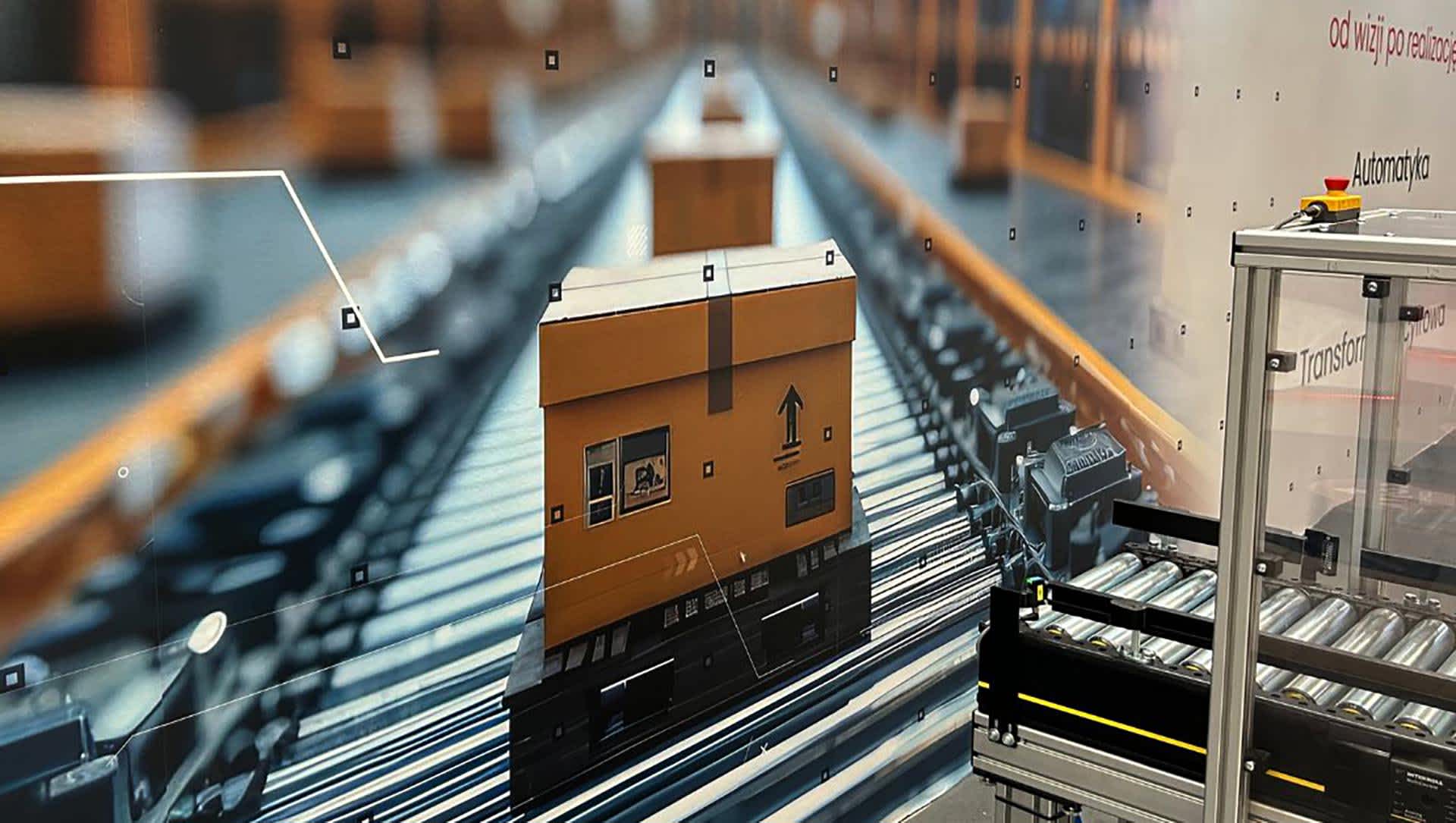
2. Implementation of robotization
The second block was devoted to methods for preparing and implementing robotization in industrial settings. It covers the design and implementation of intralogistics systems using AGVs and AMR vehicles or robot programming and simulation in a product lifecycle management (PLM) environment. This pretty much overdue term gets a slightly new meaning for Industry 4.0 and helps companies craft better strategies for increasing energy efficiency in industrial robotics.
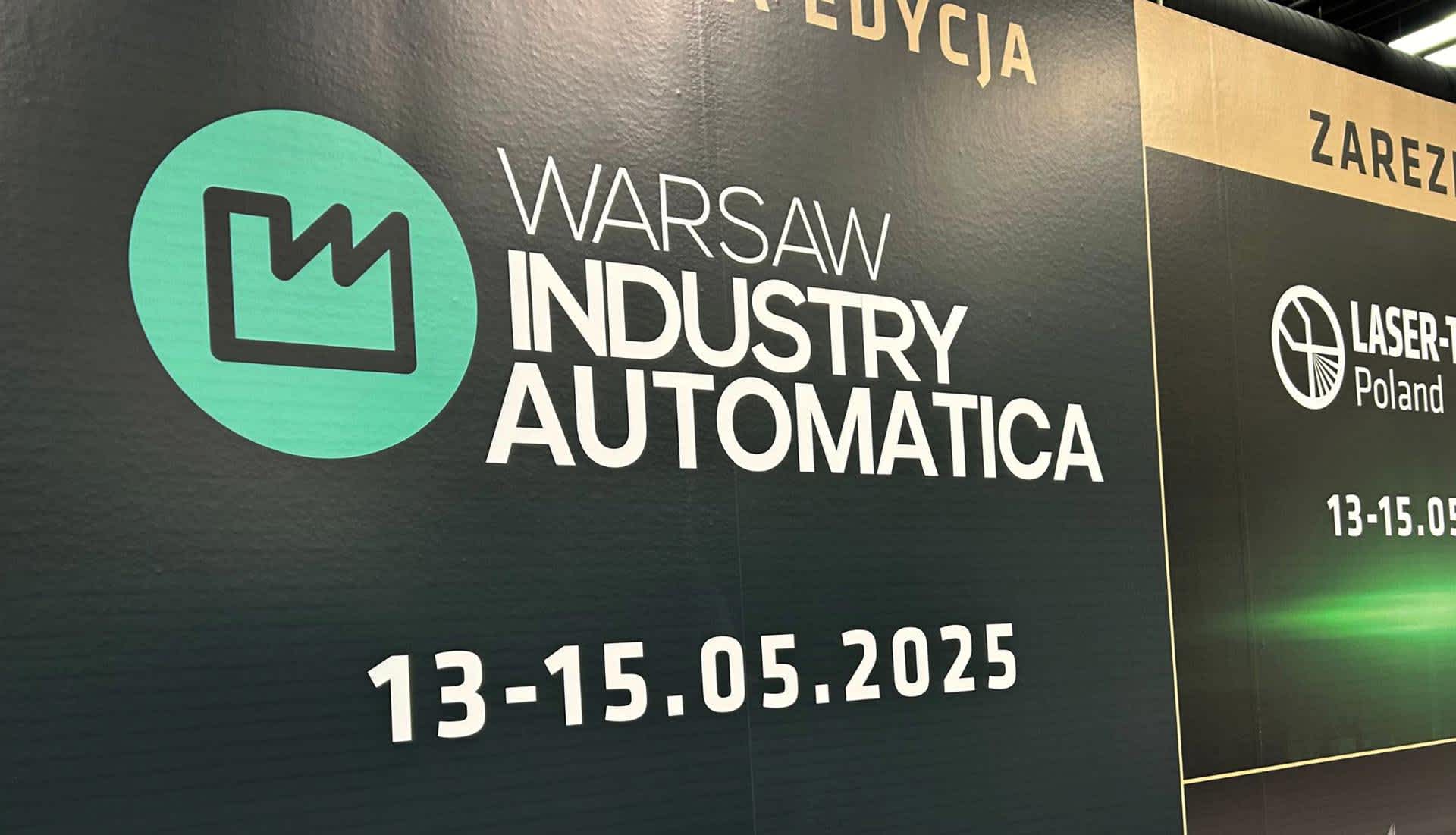
3. Safety and resilience of automation robotization
The final block of presentations brought us experienced team professionalism in safety and resilience in automation and robotization. It features insights on building and maintaining cyber security for IT/OT industrial systems presented by the Managing Director of Anzena Sp. z o.o. and Director of Machine Safety at ELOKON Sp. z o.o., They discussed the compliance requirements of the current Machinery Directive about robotization. All that underscored the significance of ensuring safety and regulation in automated manufacturing plants.
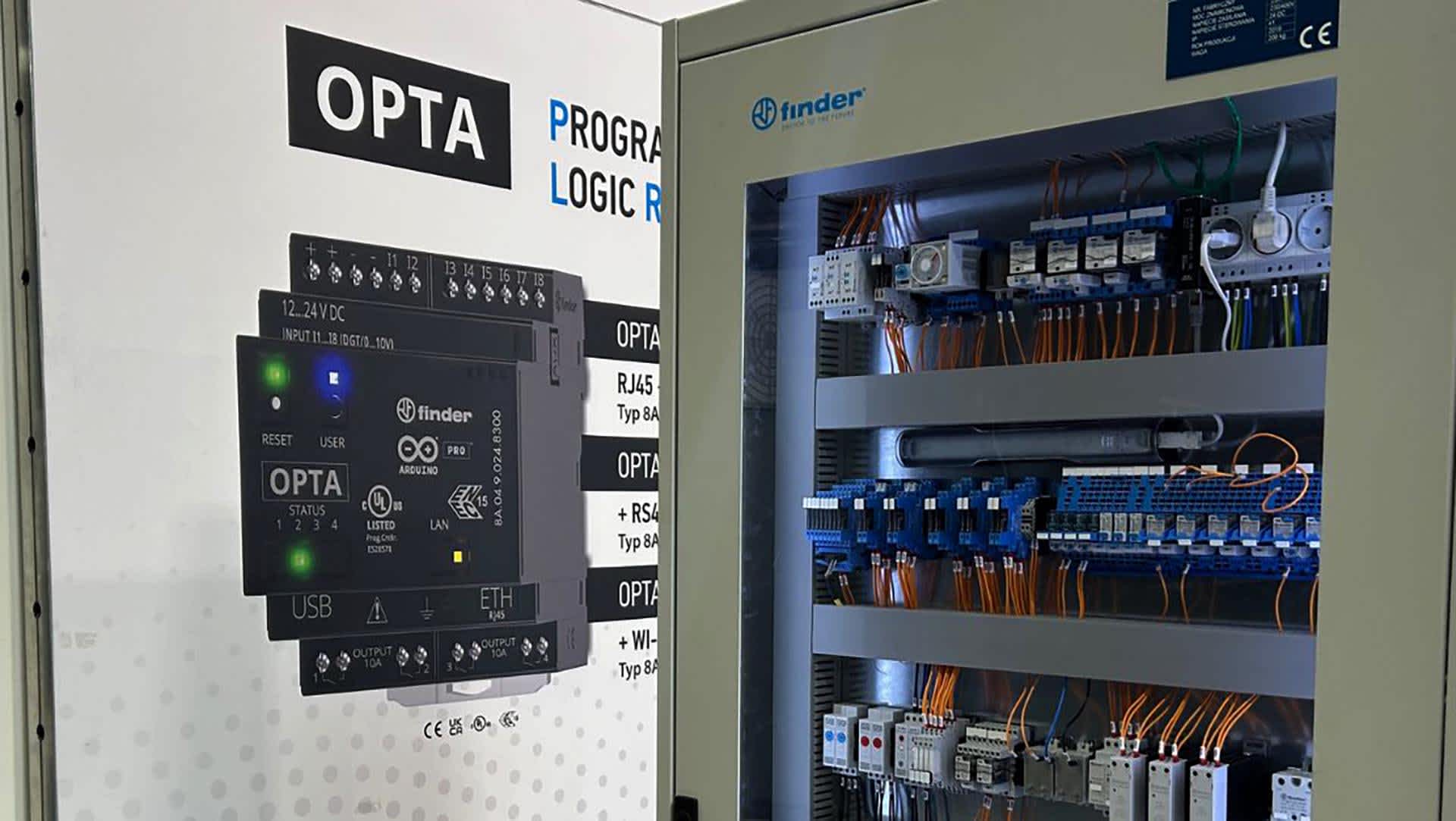
Robotics in automation. Trends and challenges
On the second day of the conference, speakers from companies such as FAIRP spoke. An expert from this robotics company explained the practical elements of robotization and the main trends and challenges facing the manufacturing industry.
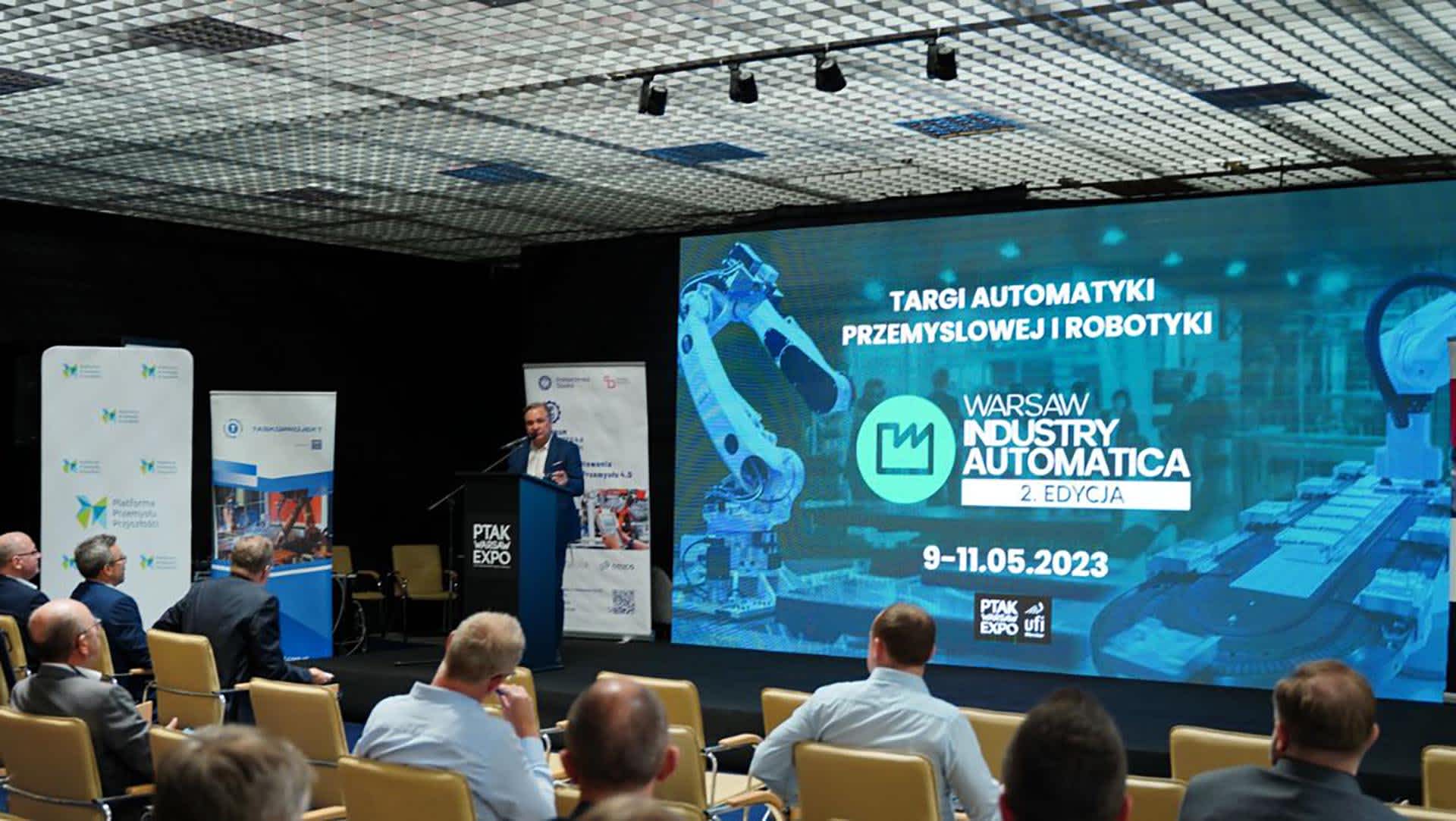
They explained that the rapid evolution of robotization goes beyond simply increasing the number of robots per 10,000 workers. This means that competitiveness cannot be increased with robots alone. You have to navigate a volatile market and face a difficult geopolitical landscape. In addition, aspects of the ongoing demographic decline were explained, which creates serious concerns for manufacturing leaders.
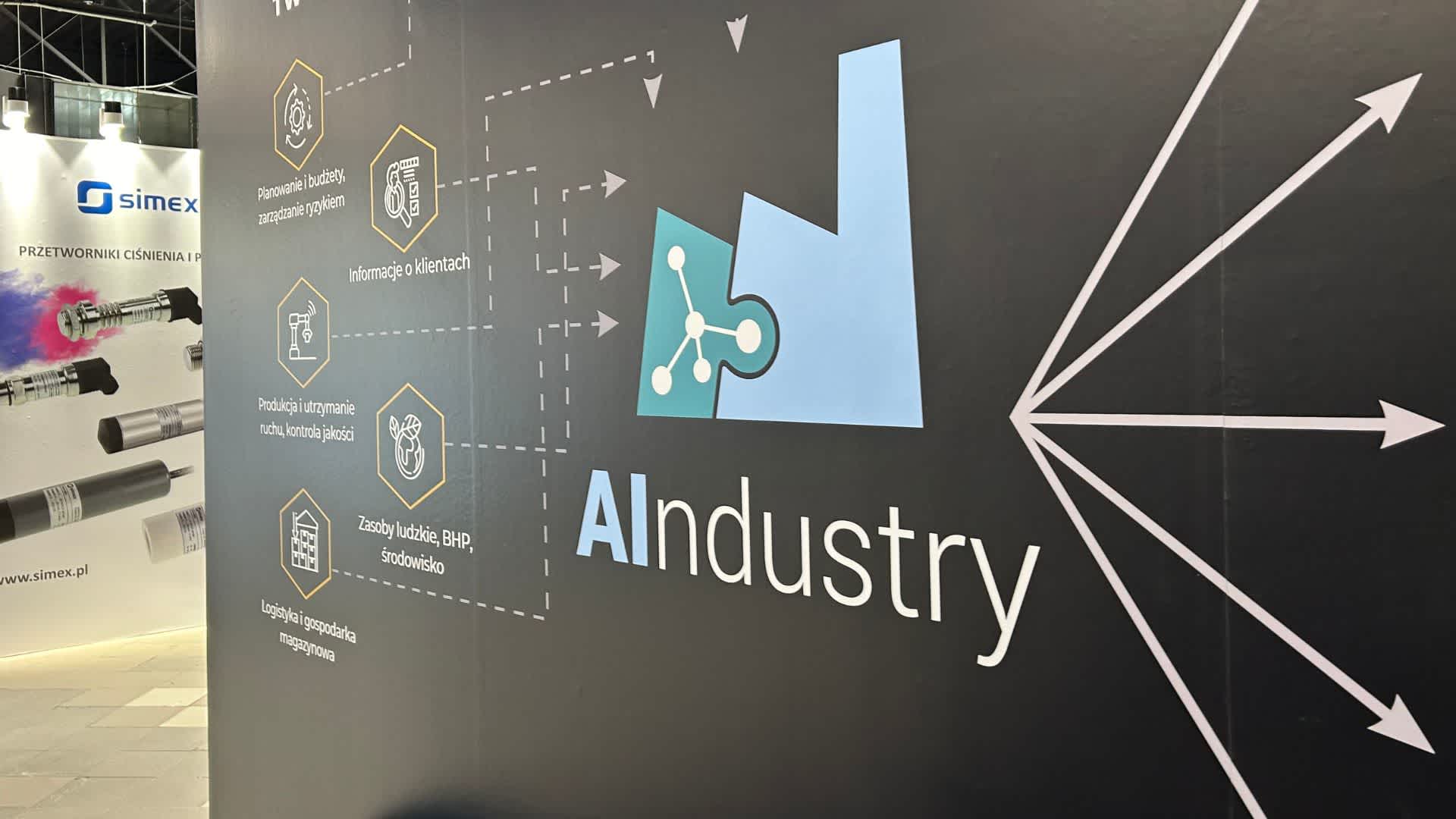
New exhibitors for high-tech
Other speakers from Dentec shed light on aspects of efficiency in manufacturing. In their presentation titled "How to Improve the Efficiency of Plastic Part Production - Robotic Overmolding - Case Study," they presented a case of a company that manufactures parts using overmolding technology, which offers several advantages.
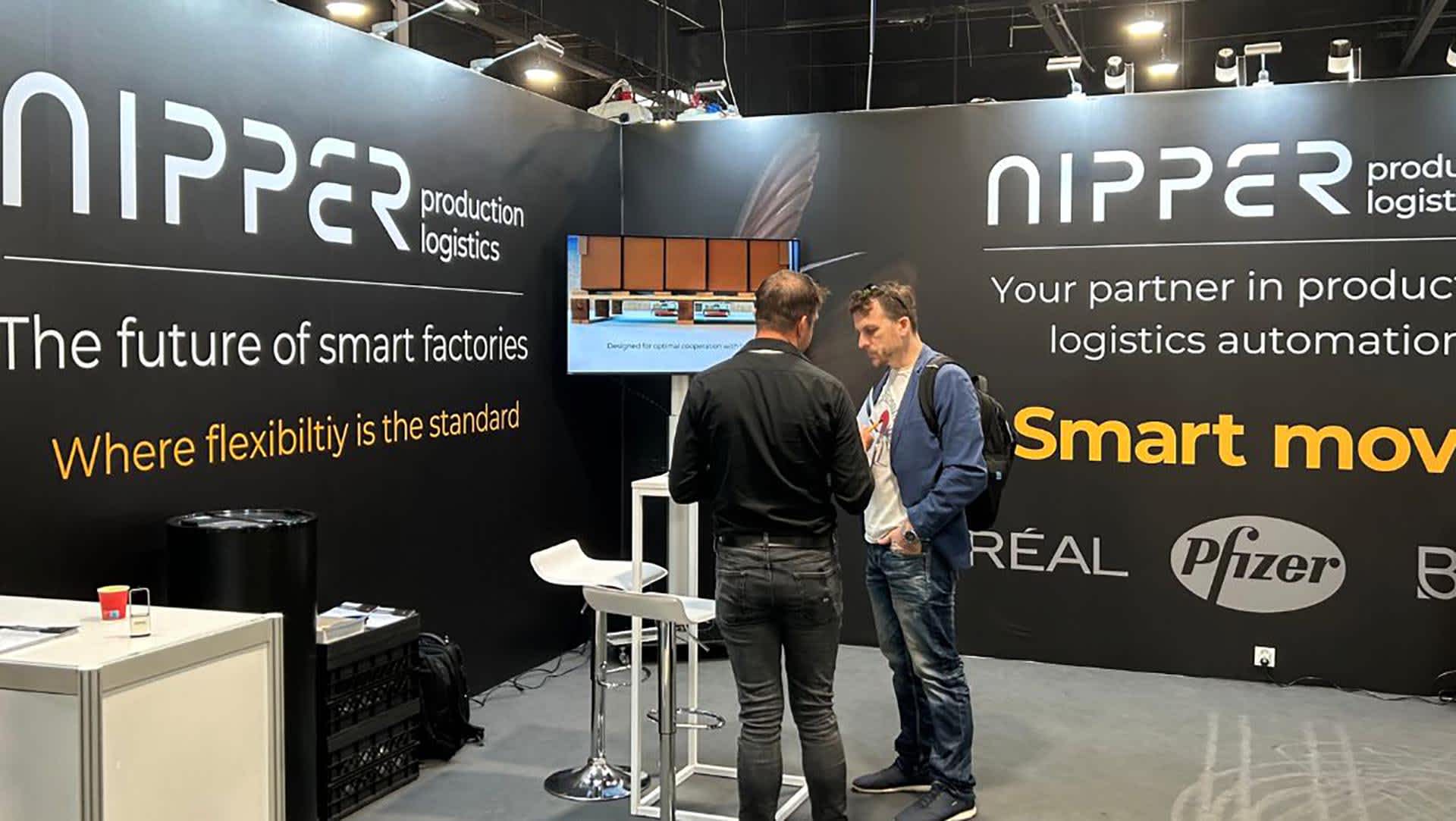
These advantages are particularly visible when feeding brass inserts into an injection mold. Visitors learned about managing and installing a console robot on a 350-ton injection molding machine and saw what business impact such an implementation had for the customer.
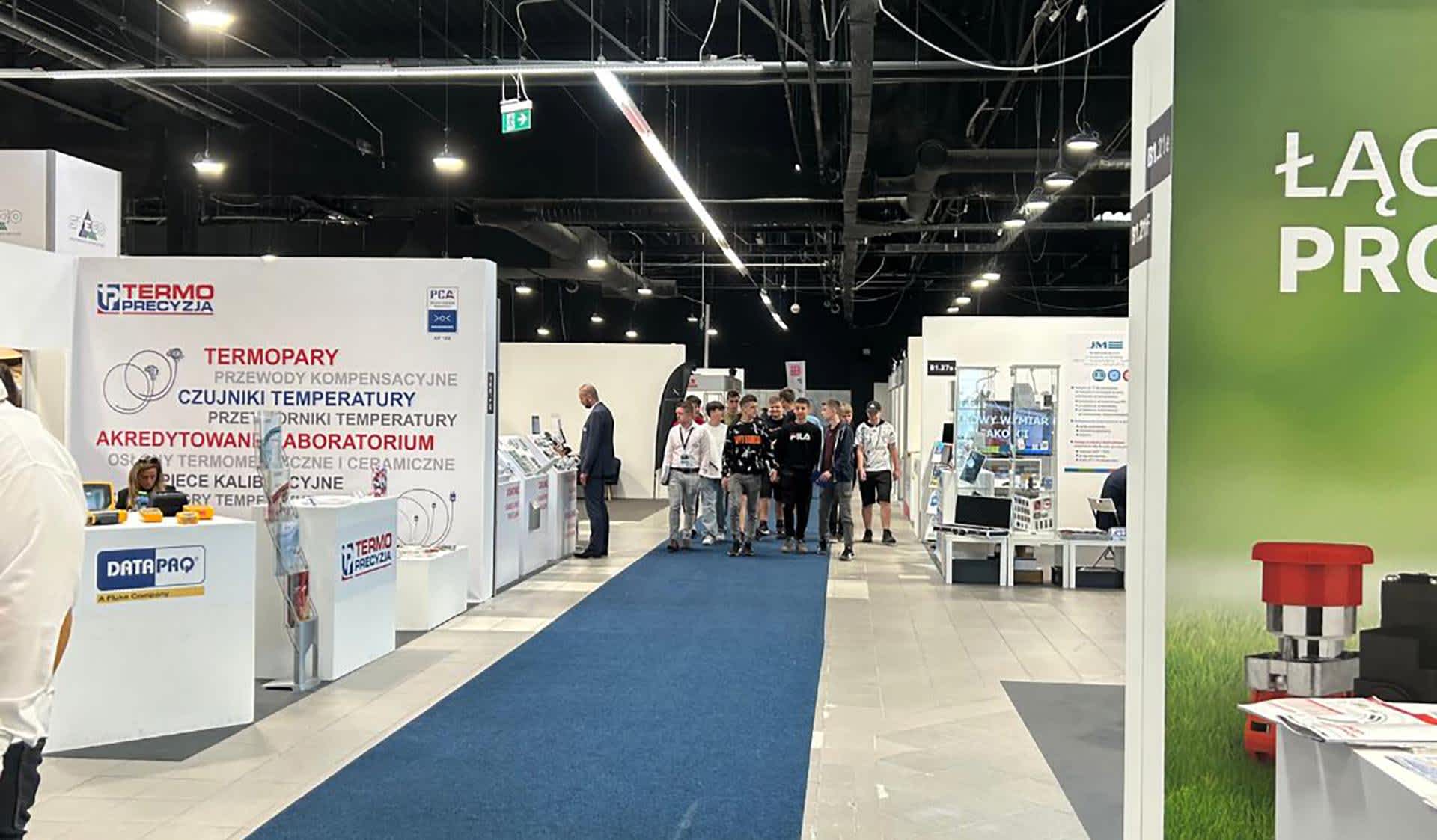
Manufacturing and software solution
During the event, we saw many companies delivering software solutions for logistics and manufacturing. While talking with companies supplying modern software for production and service & maintenance, we noticed a significant enthusiasm.
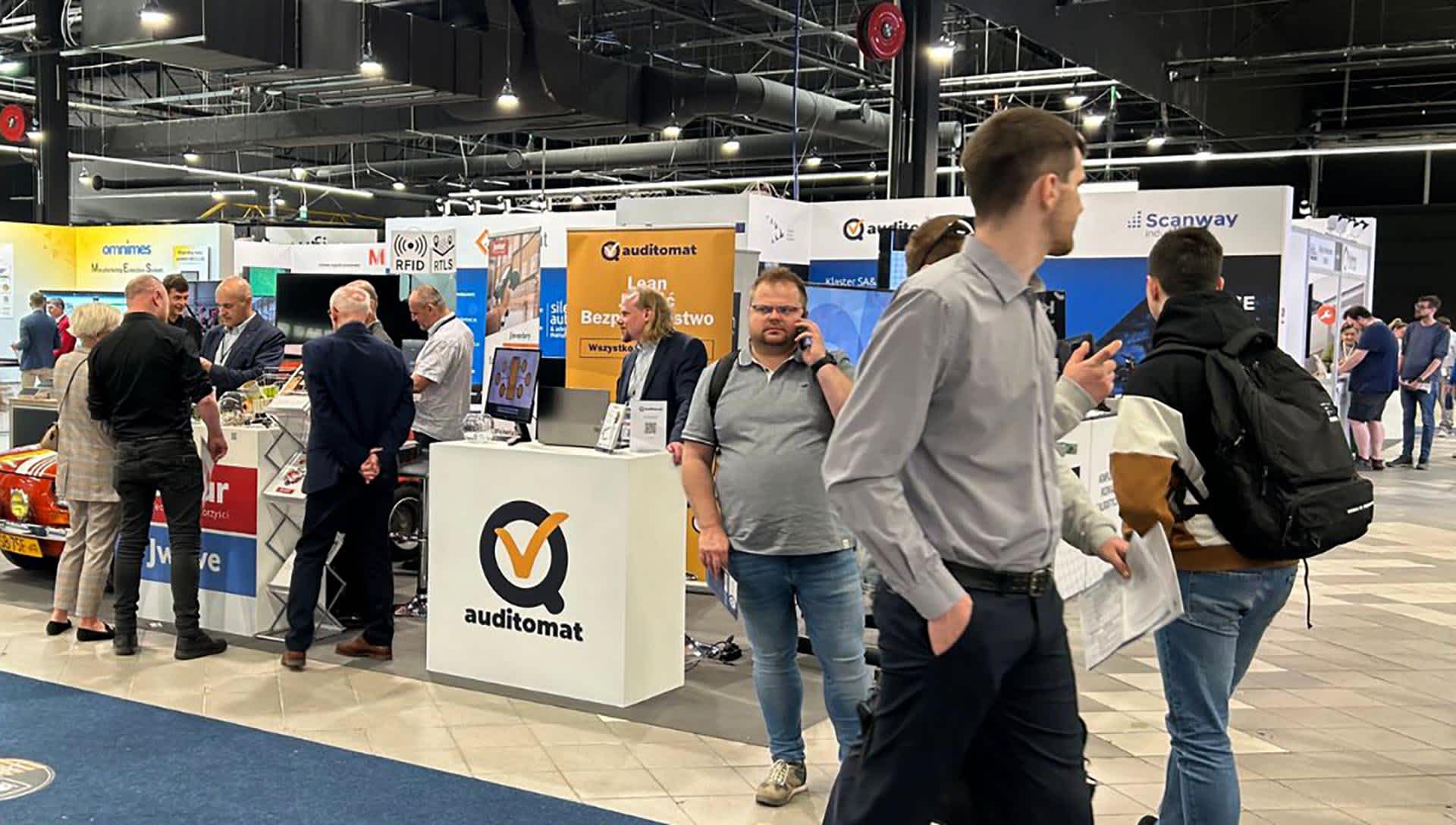
However, the notable difference arose from the perspective of companies using software for production. The gap between software providers and manufacturing companies remains largely consistent. Systems for manufacturing are often developed without insight into business operations, which is the biggest drawback of any implementation. It's incredible how many companies are dissatisfied with the overall implementation results.
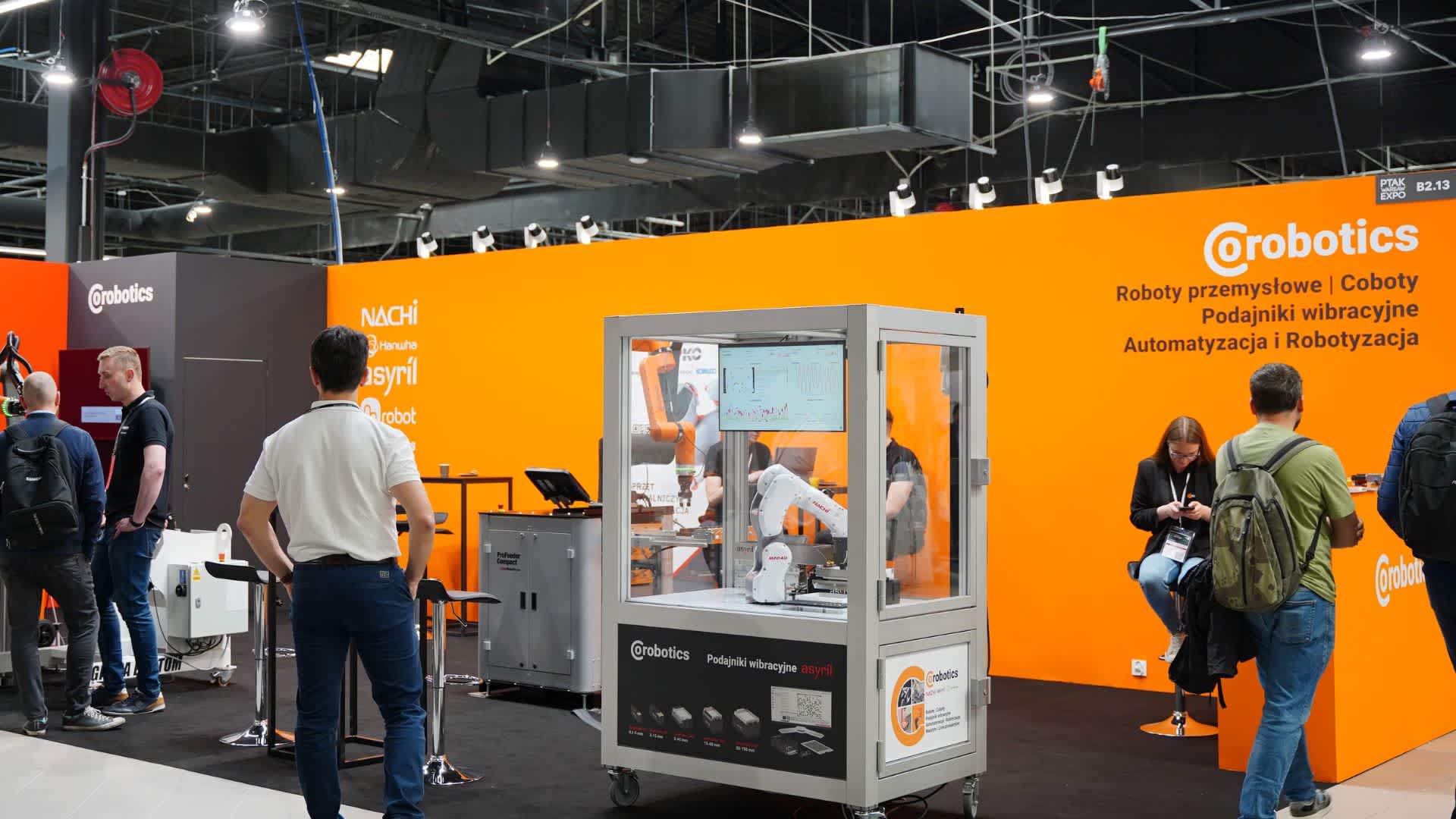
By visiting various manufacturing companies and having worked in the supply chain myself in the past, I can outline that the most significant drawbacks in system implementation stem from these reasons:
Complexity overload
Often, systems become overly complex in an attempt to incorporate every aspect of the manufacturing process. This complexity can confuse users and hinder effective adoption and integration.
Resistance to change
Implementing new systems can encounter resistance from employees accustomed to existing workflows. Resistance may stem from fear of losing their jobs or unfamiliarity with the latest technology. Yes, operational people aren't just computer savvy; they can disturb the process.
Integration challenges
Many manufacturing systems require digital transformation and integration with existing software and hardware infrastructure. Problems with incompatibility or difficulties synchronizing data between systems are leading to delays and disruptions to operations.
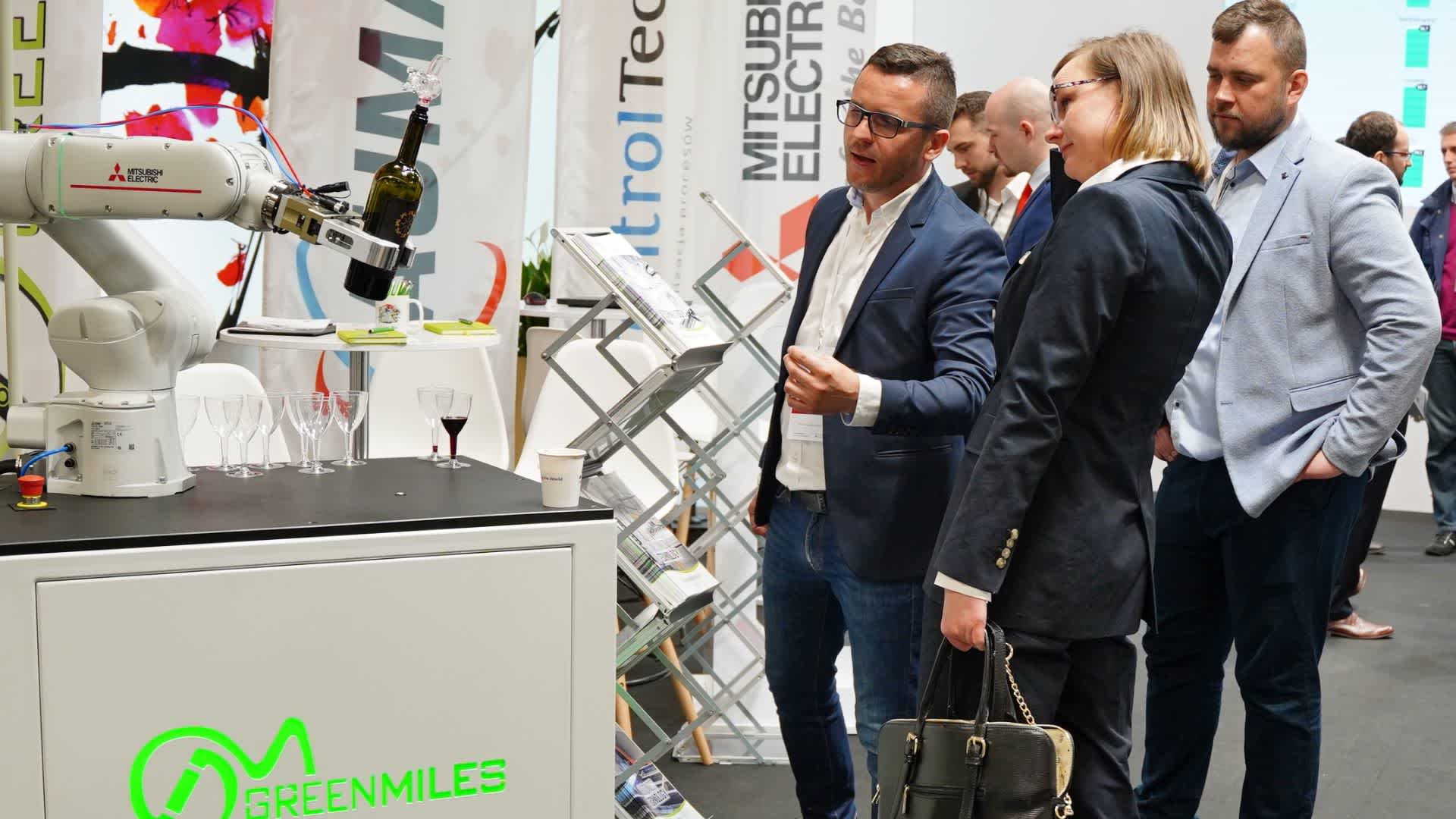
Cost overruns
Initial estimates of system implementation may understate actual costs. Unforeseen customization, training, and ongoing maintenance expenses can lead to budget overruns, affecting the organization's financial health.
Lack of user training and support
Inadequate training and support for end users can hinder the adoption and use of the system. Employees may leave and not return if frustration with the new system builds. All this happens without sufficient guidance on using the new system effectively compared to the old methods or making mistakes. Of course, there are other shortcomings, but it all boils down again to the fact that some processes become too complicated when introducing the new system.
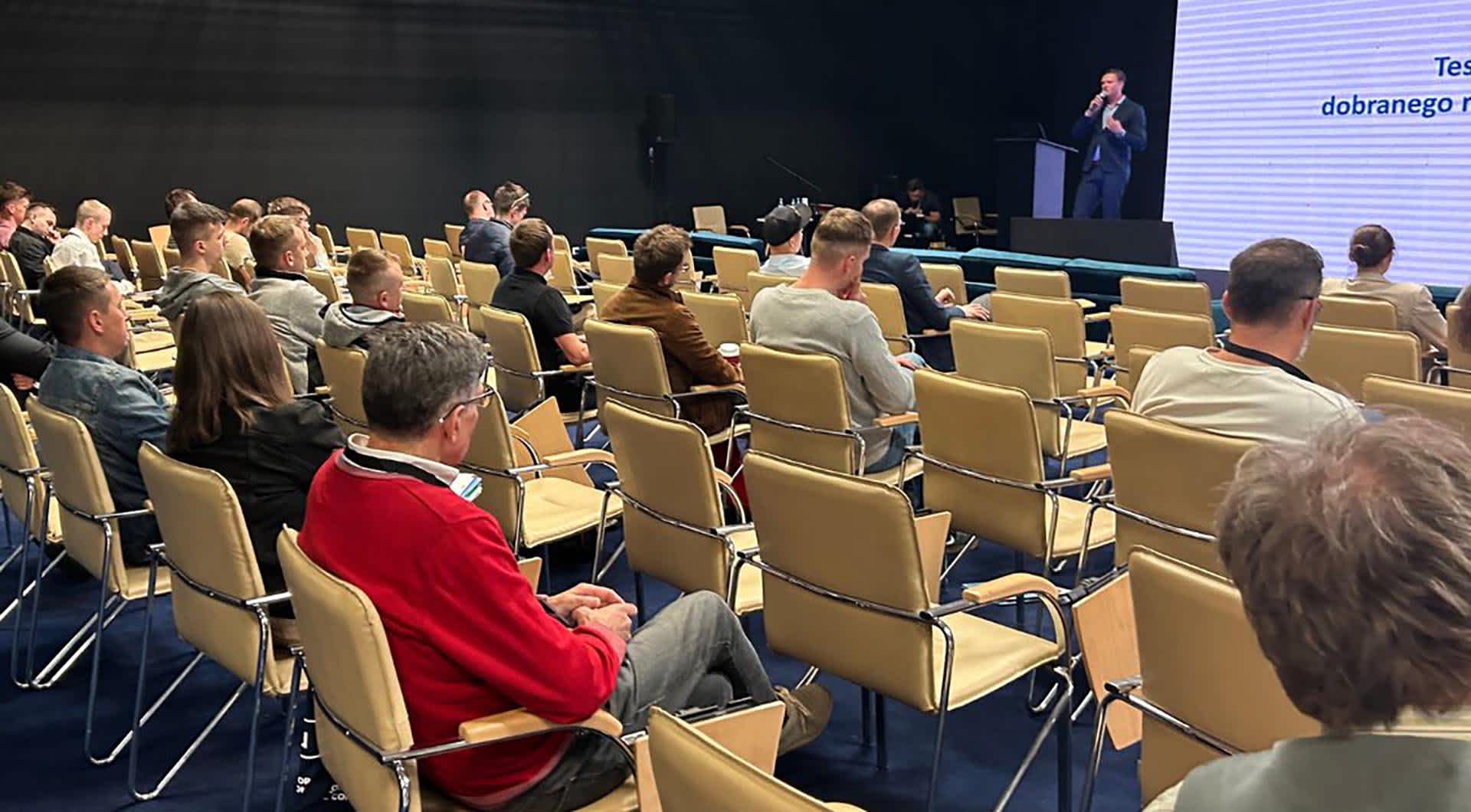
The latest solutions: but are they modern enough?
Today we see that companies have common issues across different industries. Regardless of business and industry complexity, companies face similar challenges when it comes to system implementation. One of the main ones, in my opinion, is the neglect of integration capabilities and the creation of custom software for the supply chain. During this event in Warsaw, it became evident that software providers significantly neglected the integration capabilities of systems with the supply chain.
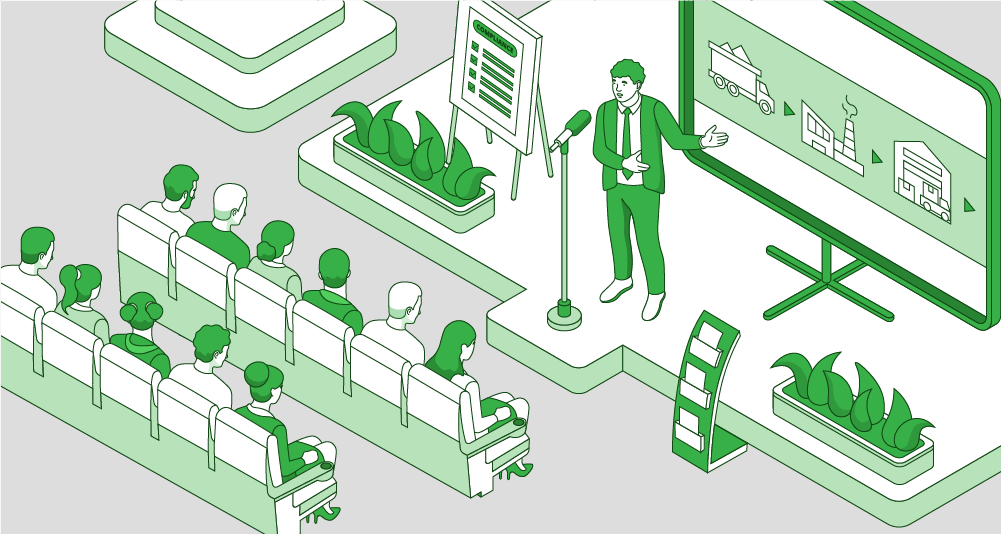
And let's take a closer look at the main points:
Supply chain for manufacturing
One provider offered a system resembling a Manufacturing Execution System (MES) but should have paid more attention to the value of integrating this system with the supply chain. Integration between manufacturing and the supply chain is crucial. While Advanced Planning and Scheduling (APS) can be implemented, integrating APS functionality with MES is equally important.
Holistic supply chain management
Businesses need a comprehensive view of all supply chain stages. Special supply chain technologies and solutions can help by integrating different systems into a single portal interface, providing a cohesive view and enhancing supply chain management.
The role of logistics
Logistics is crucial for delivering goods and raw materials to production plants. At the Warsaw event, companies focused solely on production plant solutions, managing inbound goods and transactions from dock to stock without offering a holistic view of the entire supply chain.
With the help of custom software, software development companies can provide all of this. They can integrate your legacy system and launch it on a brilliant platform for comprehensive manufacturing planning with supply chain visibility. Doesn't that sound like a resilient solution for your company? I'm sure it does.
Are you in search of a reliable tech partner?
Adexin can help with advanced logistics solutions
Contact usFinal takeaway on Warsaw trade fairs in Poland
Despite Warsaw's Industry Automatica event wasn't largest trade fair in the eastern European region, it provided valuable insights into the latest robotics, exchange knowledge about automation for the following sectors, and software solutions trends in the manufacturing industry. Key challenges identified include system complexity. Other emphases include resistance to change, integration issues, cost overruns, and insufficient training.
The event highlighted the critical need to integrate advanced manufacturing systems with supply chain capabilities. Custom software services can help integrate legacy systems and solve this issue.
If you want to optimize your manufacturing processes and improve supply chain integration, consider investing in custom software solutions that bridge various system functionalities. Contact us today to learn how we can help streamline your operations and make your business more resilient.