Summary
The Quality Management System (QMS) plays a key role in the transport industry, ensuring safety, consistency, and compliance with regulations and contracts. By using it in day-to-day operations, a company can manage documents effectively. QMS software offers benefits such as increased productivity, cost savings through digitization, improved distribution quality, increased accuracy in transport service management, and enhanced document security. We outline some of these in our article to bring value to your transportation business.
What is QMS?
Quality Management System (QMS) is a combination of processes designed to continually improve performance while addressing the needs of all involved parties. Whether talking about customers or suppliers, the supply chain implicates a certain degree of satisfaction for all stakeholders. Typical QMS documents include plans, policies, procedures, guidelines, and forms that define the system.
In the supply chain, the key role of the intermediary part is taken by transportation, where QMS is extensively deployed to improve different stages of the entire process. QMS is based on software that allows for better document management.
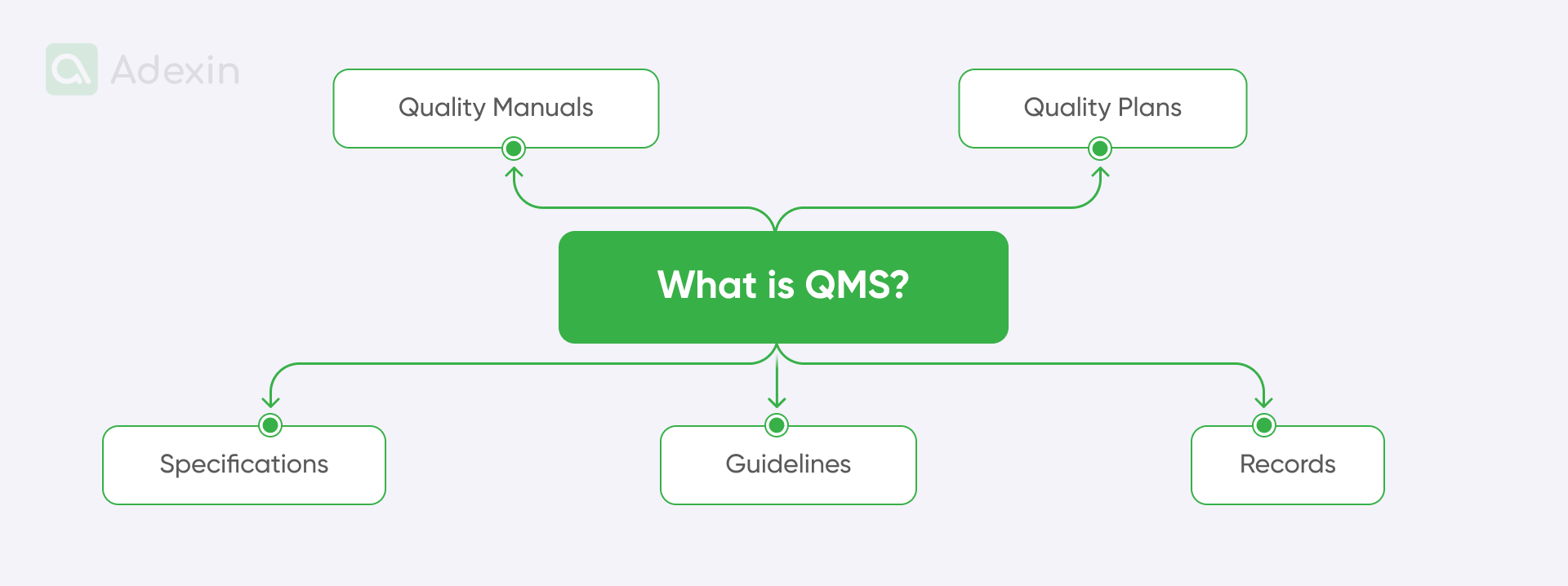
Here are the types of documents used in the Quality Management System:
Quality Manuals
These are top-level documents describing the organization's Quality Management System, both internal and external to the organization. These documents are referred to as "quality manuals."
Quality Plans
These documents outline the framework for applying the quality system to specific processes, projects, services, transportation contracts, etc.
Specifications
These are the types of documents that prescribe the requirements that products or services in transportation must adhere to.
Guidelines
These documents include recommendations or required practices for specific transportation or internal logistics operations.
Records
This category points out a range of documents that provide objective evidence of activities carried out or results achieved within a specific time frame.
What are the 4 types of quality management?
Quality management is very important to logistics, as well as the transport industry, and supply chain operations. By implementing QMS systems based on software for document management, companies can manage complex processes much more effectively.
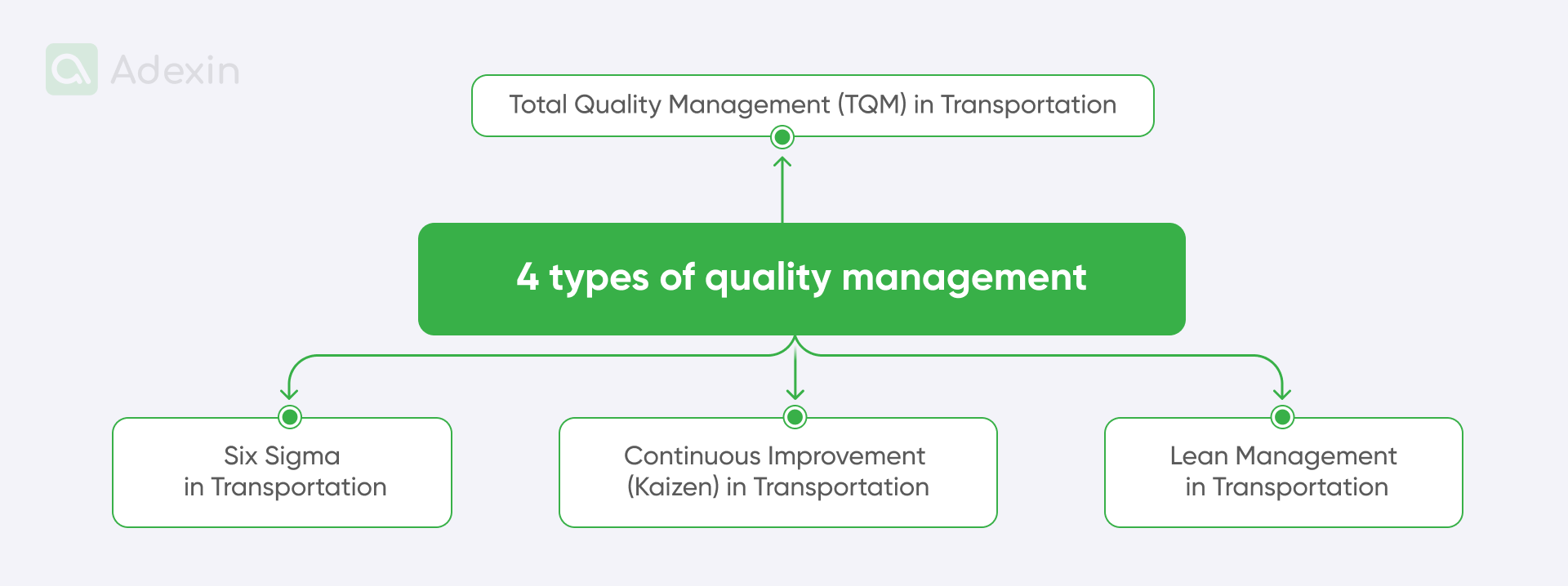
Here are the main benefits of QMS software for document management:
Increased productivity
Reduced costs due to the digitization of documents
Improved distribution quality as a result
Increased accuracy in managing transportation services
Increased security and greater document availability
Reduced strain on the work environment, including employee frustration due to poor data quality
Improved working environment with user-friendly solutions

There are several approaches to quality management. They are directly or indirectly related to transportation management, but in the long run, each of them should influence better results in overall operations.
Total Quality Management (TQM) in Transportation
TQM is a holistic approach that has broad application in transportation and logistics. It focuses on improving the quality of services provided in the transportation sector throughout the organization. At its core is continuous improvement, focusing on ensuring customer satisfaction.
It is about improving transportation at every level, from delivering goods to ensuring that they arrive on time and in excellent condition. An essential human factor of employee involvement is critical, as everyone, from drivers to logistics coordinators, plays a role in maintaining quality. TQM promotes commitment to quality at all levels of the transportation process. It also combines various models for effective document management and creating workflows, helping to control each process far better.
Six Sigma in Transportation
With its Define Measure Analyze Improve Control (DMAIC) cycle, Six Sigma is a robust transportation methodology. It begins by defining key performance indicators (KPIs), such as distance traveled, loading efficiency, and cost per kilometer. Critical analysis of the data identifies the root causes of problems, such as inefficient routes or loading practices. Once issues are identified, appropriate solutions are implemented, leading to significant productivity gains.
Training employees as truck drivers is key to sustaining these improvements, ensuring that the transportation process remains efficient and profitable. By joining a Six Sigma process based on QMS and digital documents, these benefits can be leveraged in the transportation sector.
Continuous Improvement (Kaizen) in Transportation
Kaizen is about making small, constant improvements to enhance efficiency and quality over time in transportation. In the long run, this entails regularly analyzing processes and gathering feedback from drivers, logistics teams, and customers to strive for better operability within the supply chain.
Areas for improvement are optimizing delivery routes, reducing transportation times, or improving communication among different stakeholders. Kaizen promotes a culture of continuous learning and innovation in the transportation sector.
Lean Management in Transportation
Lean management rules fit well with the transportation goal of maximizing value while minimizing waste. The approach involves identifying and eliminating various forms of waste in transportation processes. For example, this could mean reducing overproduction by optimizing shipment sizes and minimizing excess inventory by implementing just-in-time practices.
Lean management in transportation leads to cost savings and productivity improvements, which are vital in today's competitive logistics landscape.
Beyond these four quality management methodologies in transportation operations, many others require proper quality document management based on the software. This approach in your operations can lead to smoother logistics processes, cost savings, improved customer satisfaction, and a more competitive position in the industry.
What is the process of digitization?
QMS software allows paper documents to be digitized. This means that any document with printed text, a manuscript, or an image can be converted to a digital format. The process involves capturing a digital representation of a physical object in an algorithm. The solution requires optical character recognition (OCR) technology.
OCR technology is often embedded into QMS software as an extra feature that allows:
Pattern recognition in transportation
Optical character recognition (OCR) is key to automating tasks in the transportation sector. OCR programs learn from different fonts and formats to recognize characters in scanned documents. The technology is used to extract information from shipping labels, invoices, or receipts, as well as to manage all documents in QMS.
Feature detection
In transportation, OCR is based on feature detection. Predefined rules identify specific letters or numbers based on features such as angular lines, intersections, or curves. For example, in shipping labels, OCR can recognize Purchase Number (PN) or Sales Order (SO) as several lines meeting at specific points. That way, OCR is streamlining data entry and improving accuracy in logistics and shipping.
What is a QMS document management system?
QMS documents management system is about keeping document quality on through control and checking if the document is updated as well as if all fields are covered with required details. Regarding the corporate level, there are several formats for maintaining quality documents. This approach can be ensured with QMS software that can automatically document control and automated audits.
The management of QMS documents is validated by Quality System Procedure (QSP), a record that specifies or describes how an activity should be performed. It may include methods to be used and the order of operations.
The QSP relates to the formatting of the document, which may contain various headings describing attached data. A typical transport document may be written with the following titles:
Purpose
Scope / Field of Application
Definitions and Acronyms
Responsibility
Materials Required
Procedure
Documentation
References
Revision History
Appendix (if applicable)"Tables
Each heading may contain required information whose accuracy can be automatically checked within QMS software. Managing quality data in such a way is impossible with the typical environment of, say, MS SharePoint.
How can we increase quality document control in transportation with software?
QMS software can enable you to control documents without human interaction. It can highlight errors in transportation documents while maintaining the highest document quality.
Here are the methods for quality document control and records management in transportation using software:
Document Control
This outlines the fundamental measures for controlling documents and changes that can affect quality. For transportation documents, it ensures they are approved and distributed for use at appropriate locations. All changes must be reviewed and approved with virtual signatures by the same organizations unless specified differently by the requester.
Quality Assurance Documentation
This method is employed to maintain a satisfactory level of records management to support activities that impact quality. It includes incorporating operational logs into the system, documenting reviews, inspections, tests, audits, monitoring, and material analysis. Quality assurance should also encompass related data such as personnel qualifications, procedures, and equipment. This pertains to the inspection and test records of documents, where results should determine the level of acceptability and possible actions for rectifying discrepancies and errors.
How can we improve document control processes with document digitalization?
The Quality Management System is recognized as a major tool adopted by organizations to survive and succeed in transportation. QMS is tightly connected with a document management system (DMS).
To maintain improvement, it is important to provide well-defined and documented procedures contributing to consistent outputs. These are often easy to determine through workflows, where system administrators can track all changes and prevent discrepancies, thereby facilitating the execution of practical work processes.
It is essential to set up smaller management systems based on workflows. These workflows can be created in QMS software along with DMS. Here are examples of how it works:
Document approval process
The general document approval workflow involves the author submitting the document specification for approval via the DMS in a completely digitized form. As an optimal result, the total number of documents approved should be equal to the total number of documents sent for approval (when we assume that no records are rejected).
Usually, rejected documents need to be corrected and resubmitted for approval. In some cases, papers may require urgent revision and support due to customer issues. Such rework can potentially lengthen the approval process for documents and create room for process improvement. [1]
Document writing framework
One example of document set-up is preparing a dispatch document template for truck drivers. The document will be fully digitized, allowing drivers to fill it in manually on mobile devices such as tablets or mobile phones. Each field in the document template requires correct data to be entered.
The document can include a workflow from QMS that prevents drivers from entering incorrect values into the form. This means that drivers cannot use different characters and signs for shipping numbers, purchase orders, and other fields than those already recognized by the system.
How to implement a document control system?
The importance of effective document control within the transport sector is often underestimated. Indeed, in many cases, it can be the critical factor determining the success or failure of a company's strategies and other business initiatives.
The exponential expansion of data and the changing methods of recording and communicating information pose significant challenges for companies in developing robust document management frameworks to remain competitive in the market.
Here is the preliminary program framework for document control built-in QMS software functions:
Problems and Challenges
QMS software can detect text issues and missing parts.
Document and Archive Management
The software can automatically store documents in the required format and detect incorrect ones.
What Needs to Be Controlled: QMS can set up a to-do list for each document format to prevent manual errors.
Components of a Document Management System
QMS supervisors can set up document criteria using the software for each user and administrator, which will be automatically tracked.
Managing Deliverable Documents
QMS is capable of tracking deadlines for document creation and notifying users about expiration dates and other important details.
This means that QMS software can ensure document control with built-in functions, saving time for administrators. Here are other functions for document control that can be provided by the QMS system:
Reporting Progress and Success
Supervisors and managers can gain insights into metrics based on document performance and correctness ratios, such as balanced scorecards, KPIs, and dashboards.
Assembling Assurance
The software has the ability to conduct document audits and perform automated checks.
Standards and Procedures
QMS software can send prompts to users regarding document standards to ensure compliance is maintained.
Final thoughts
The QMS is integral to the success of the transport industry, providing a safety management system and enabling consistency in the application of process and safety rules in the workplace. It is also closely linked to preventing violations of law regulations and customer contracts.
Typical QMS software can support document control processes and procedures to define a control framework. Such software can support records management to establish effective and systematic control over the creation, receipt, maintenance, use, and disposal of records.
At Adexin, we help companies manage their documents to the highest quality standards. We can develop custom DMS and QMS software to capture and store evidence of business activities and transactions in the form of digital records. Our role is to provide the transport industry with document management tools to help them run their day-to-day operations. Contact us today to find out what we can do for your business.
Reference:
[1] Retrieved from: https://core.ac.uk/download/pdf/229266126.pdf