More than half of surveyed companies are affected by rising problems related to customer retention. This trend was closely examined by The Business Continuity Institute (BCI) in the UK. What does this mean for today's businesses, and what is the root cause of it? There is no doubt that companies may face severe financial problems. In this article, we share valuable insights from the latest BCI Supply Chain Resilience Report 2023 as we try to explain why digitalization and custom development in logistics, supply chain, and transport matters for SMEs as well as large enterprises. Explore the findings and prepare for what lies ahead in the year 2024.
The need for audits drops to 29% thanks to digitization
A major question among business experts arises from how to keep customers loyal. Companies cannot retain customers without providing them with a reasonable competitive advantage. In many cases, the primary factor is keeping prices low. It boils down to the point that most logistics, supply chain, distribution, and transportation companies struggle with extremely low-profit margins to keep businesses up and running. It is one of the factors that help companies better understand the business continuity of key suppliers.
When analyzing the procurement process, low margins are one factor that keeps customers under the roof. It impacts their financial operations and forecasts directly. Therefore, nearly one in five respondents (19.5%) of logistics companies in the supply chain indicated the need to assure most customers of the business continuity arrangements. Additionally, 13.3% said they consistently had to provide such assurances. However, more than a third (34.5%) mentioned that they had to provide such evidence only occasionally (19.5%) or rarely (15.0%).
Many companies use software to conduct checks to confirm business retention. It has resulted in a shift towards acquiring customer information, with more than 42% still relying on supplier documentation and nearly 38% preferring face-to-face communication. The need for business audits has dropped to 29% of all respondents.
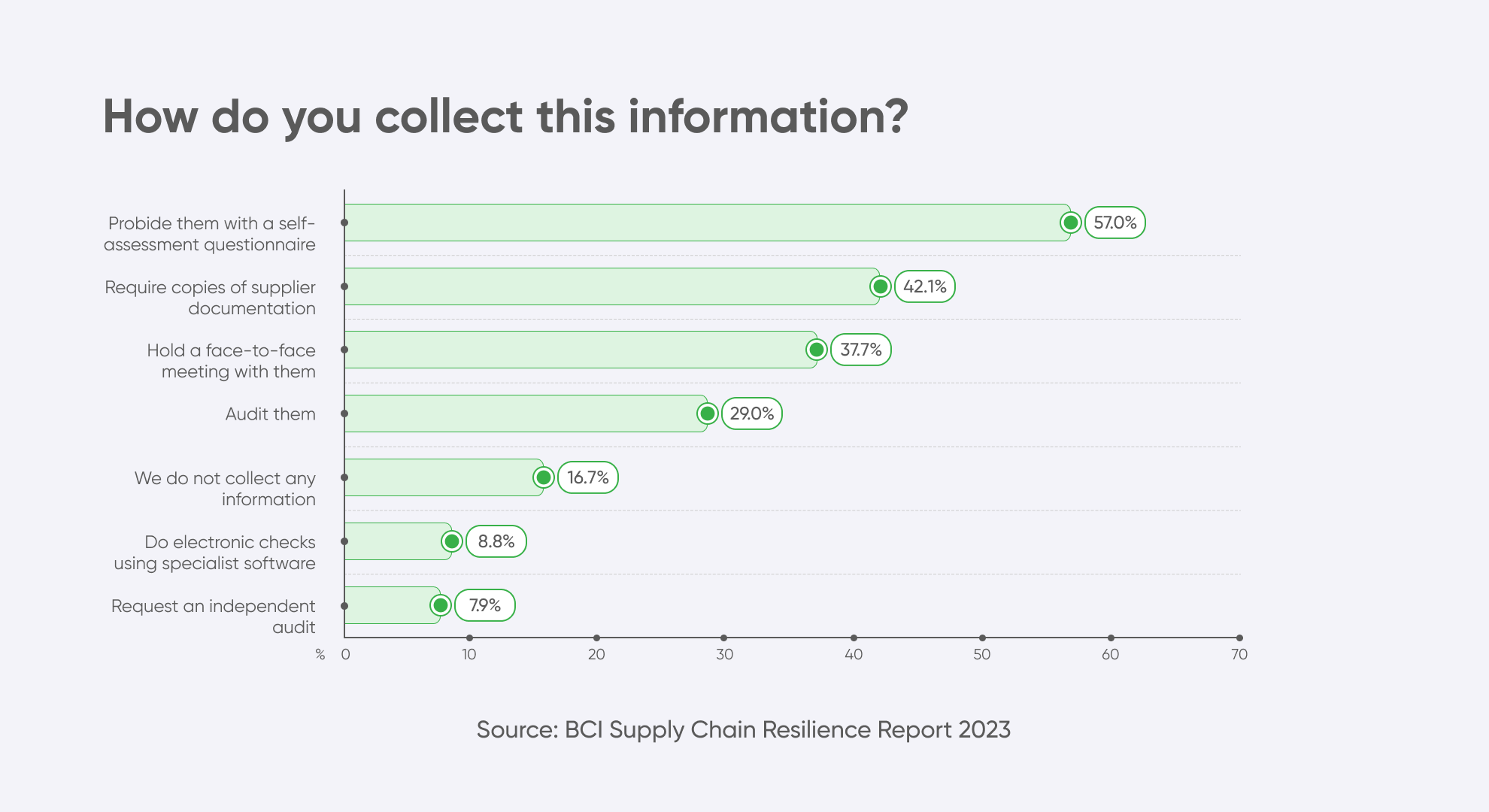
Such requests are accompanied by audits conducted across the supply chain network and business operations to identify pain points in qualifying future business continuity. Of course, audits can be conducted for all types of administrative and operational operations to gain greater insight into future collaboration. Nevertheless, not all companies will participate in the process using either method. Very often, this approach can be enforced by contracted assurance in advance.
12.6% of organizations neglect critical information on continuity of supply
Many factors influence business operations. Organizations that shift their operations to digital tools are also proven to be much better at decision-making. They collect data on their suppliers with much higher accuracy, and by maintaining data quality, they establish a better decision-making process.
However, there is still a high number of companies that neglect to use data or even collect any data on their business operations. Therefore, it becomes tough to predict further steps in their business and validate financial ability and forecasting.
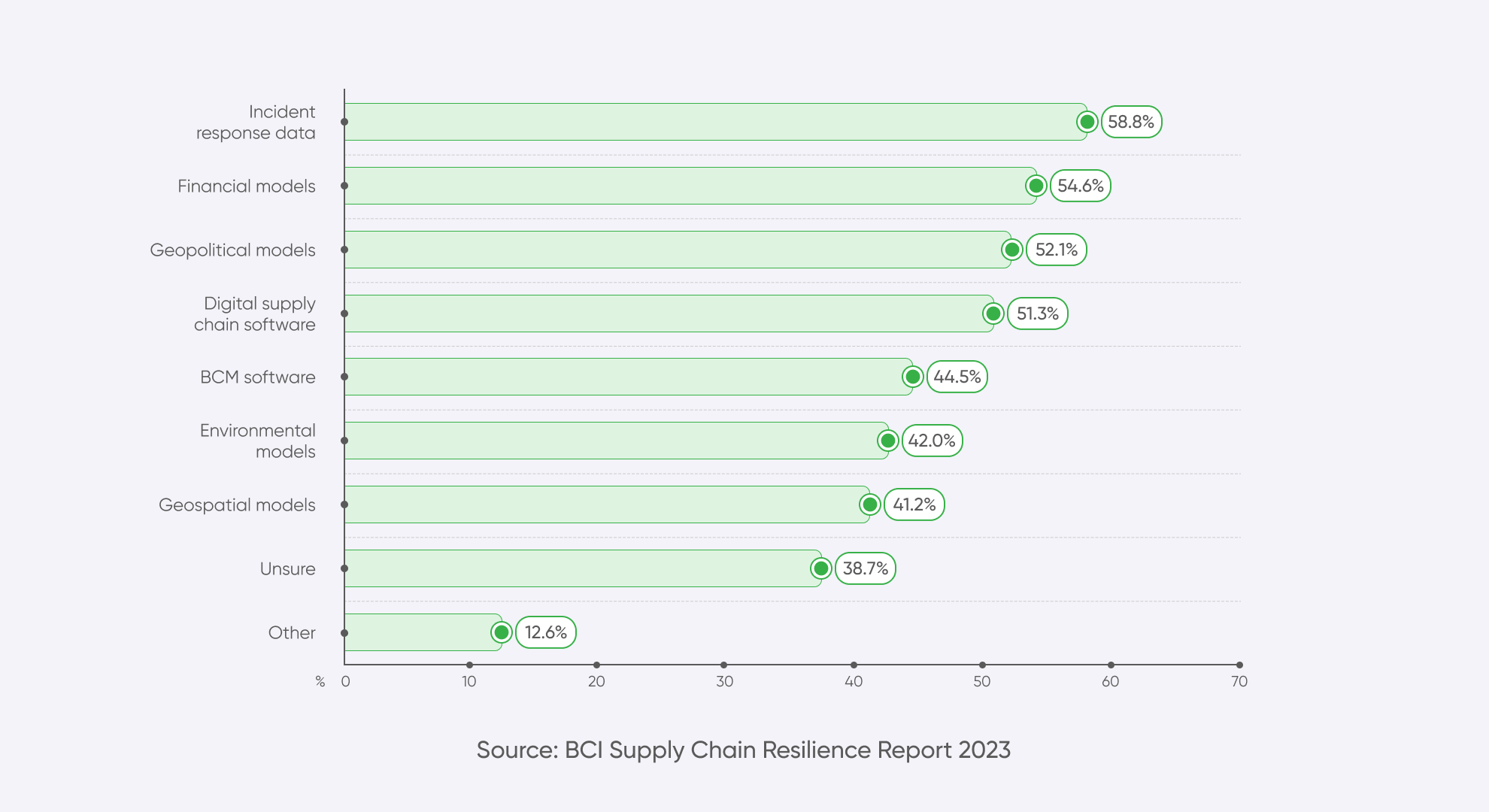
Except for the scope of data, a set of business capabilities is required for internal assessments that influence customer retention. That means companies should remain innovative and, again, keep costs competitive in the market.
Here are four main factors that affect customer retention:
Customer satisfaction. In today's competitive business, it is important to keep the customer satisfied. Lack of or inadequate practices can result in the loss of customers. Customer service is not defined by accounting practices but by customer perception.
Innovation. Taking advantage of technological advances and innovative approaches can further improve customer satisfaction and retention. Firms should offer more efficient services and solutions tailored to meet the changing needs of clients.
Relationship management. Strong personal relationships between accountants and business clients increase retention.
Service standards. Implementing higher service standards improves retention. It includes promptly responding to phone calls and emails, but also the operational part of service delivery.
40.7% of companies use technology to enhance operations
To keep customers, companies need to develop better internal business practices. The four elements above are causing customer retention issues from the inside out. As an example of service standards, we can consider situations related to hiring personnel in logistics, supply chain, or transportation, which have been significant issues over the years, not only due to personnel shortages.
One of the situations leading to problems related to hiring qualified personnel is the rising requirement for higher salaries. Low margins prevent businesses from meeting their personnel needs, often resulting in declining service quality. Today's warehouse clerks are mostly low-qualified personnel handling most of the work. Still, inconsistencies in their performance suggest that warehouse management tasks for personnel should be simplified as much as possible.
Many processes have been digitized to address the challenge of low-qualified personnel. Today, nearly 40.7% of logistics, supply chain, and transportation companies are leveraging technology to enhance operations. This trend is equally crucial for small and medium-sized businesses, which are at a higher risk of losing customers due to poor service delivery.
Companies are utilizing technology to record, measure, and report on supply chain disruptions that impact performance. The image below illustrates the use of technology for this purpose.
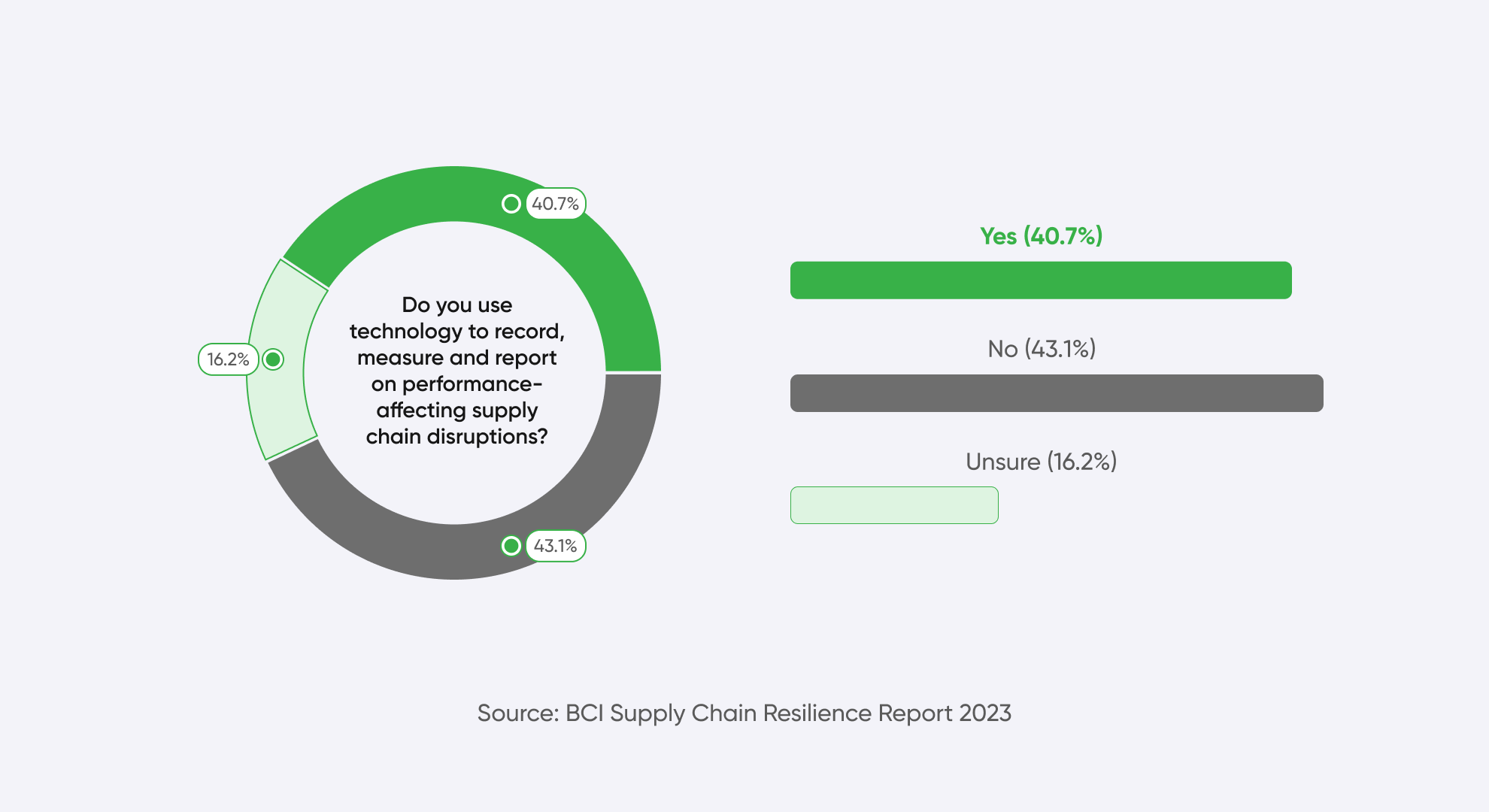
Logistics companies often adapt technology to simplify processes by using custom software, which also facilitates data collection. Moreover, custom software development enables companies to have unlimited operational capabilities that can be built on demand to enhance business operations in supply chain operations and beyond.
Here are several ways custom software can support logistics and supply chain operations:
Process automation. Automates tasks such as order management and inventory tracking. The company can reduce errors and speed up operations.
Real-time tracking. Provides real-time insight into the movement of goods. Helps optimize routes and minimize delays.
Inventory management. Custom software manages inventory levels. It boils down to reducing shortages and excess inventory.
Supply chain collaboration. Facilitates communication between stakeholders. Collaboration can improve coordination and responsiveness.
Data analysis. Analyzes supply chain data. Companies can gain capabilities that provide insight into decision-making.
Are you in search of a reliable tech partner?
Adexin can help with advanced logistics solutions
Contact usFinal takeaway
According to the BCI Supply Chain Resilience Report 2023, companies that neglect technological development are at risk of low business resilience and lower customer retention. They can expect a big drop in orders and serious financial problems. To better engage with customers, companies should use digital solutions that can help with data collection and decision-making.
Adexin is a custom software development company that improves supply chain resilience. We have over ten years of experience providing software to various logistics, transportation, and supply chain companies. Contact us today to find out what we can do for your company.