Summary
The idea of reverse logistics has become increasingly important in the supply chain, where sustainability and customer satisfaction drive intelligent decision-making. It is also commonly known that today, transportation meets new challenges arising from sustainability requirements. Effective reverse logistics systems help minimize overall costs and improve transportation. Within this article, we uncover various examples of the top reverse logistics companies and industries where reverse logistics plays an important role. Let's see how you can optimize your logistics.
What are examples of reverse logistics?
Sustainability and customer satisfaction further shape business practices. This is why reverse logistics is key in maintaining a supply chain and minimizing environmental impact. Reverse logistics is for all operations related to the reuse of products and materials.
We can outline reverse logistics, also called return logistics (RL), as the control of materials returned by clients. This management entails the flow of returns from customers to distribution centers or shipping back goods to production facilities. It also means that RL involves extensive transport planning operations.
Keeping in mind the dynamics behind how, why, and when clients return products is vital to understanding the complexity of reverse logistics better. Consumer returns are estimated to range between 3% to 50% of total shipments. It contributes to the total revenue of 3-5%. Once we consider all material movement between various stakeholders, we can easily discover what are examples of reverse logistics. [1][3]
Here are some most commonly known examples of reverse logistics:
Returns of products from customers
This part includes the process of receiving and managing products returned by customers. Customers may want to return their products because of defects, dissatisfaction, or a replacement request. Proper handling of returns in transportation is essential to maintaining customer satisfaction. Therefore, end recipients should have a clear path to return goods easily.
Recovering unsold goods from partners
Some contractual agreements with distribution partners often obligate the return of unsold goods. This process involves the recovery of the items based on the contract terms between the manufacturer or supplier and the distributor. It requires good quality transport management to avoid damaging brand-new goods.
Returnable packaging material
Reusing packaging materials for environmental sustainability is very popular in the Fast Moving Consumer Goods (FMCG) industry by returning KLT boxes or in high-tech, often using reusable antistatic bags. These sustainable business practices include reusing packaging materials whenever possible and involving large inputs on transport.
Refurbishing products
Refurbishing goods is an important step in extending the life of products. Very often, the high-tech industry is recovering its products. Repairing and improving the appearance of items that come back to customers also involves smart transport planning from the customer to the recovery center and back to distribution.
Repairs and maintenance
This part of reverse logistics is very similar to refurbishing, but at this point, items are returned to the end customer after reparation or maintenance check. As a final result, the customer is receiving back its previous item. When it comes to transportation, it also requires a certain workload to ensure that the product will be back to the customer in one piece.

Return defective products
This sort of reverse logistics is very popular among companies with extended manufacturing capabilities. Most likely, it is about fixing errors of not completely good products to maintain some part of the assembly. The recovered product is shipped back to distribution. Therefore, this approach requires cost-effective transportation management.
Aftermarket sales
In cases where there is excess product due to returns or overstock, companies may choose to sell these products on secondary markets. It allows them to recover some of their investment and reach a wider customer base. It involves establishing new routes in the supply chain and some redelivery directions to improve transport goods flow.
Recycling
Many companies these days have implemented strategies for the proper disposal of end-of-life products. It is key to environmental responsibility. Recycling and safe disposal methods help reduce the environmental impact of waste. If companies have well-established ways to return, it brings the businesses a return of money from recycling. That means goods are often transported directly from the customer to the recycling facility, which requires a sophisticated planning system in place.
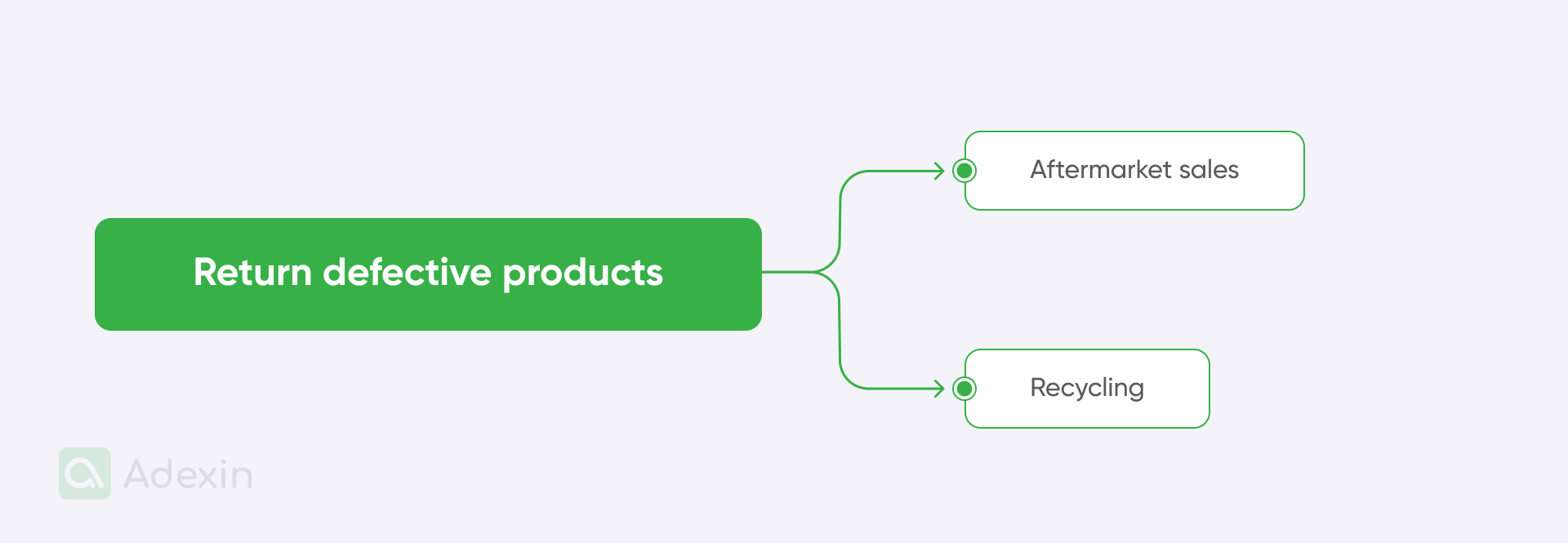
Role of reverse supply chain
There is no doubt that applications of reverse logistics have their place in the military. It is a visible, reliable solution for many logistics companies. Strategic Distribution Management Initiatives taken towards the supply chain involve directly reverse logistics. RL is also one of the tactics for a sustainable supply chain. To better understand supply chain dependencies for RL, it is quite important to see what are the stages in the process involved.
Reverse logistics process in the supply chain includes these stages:
Initialization
The consumer initiates and requests a return from the supplier. There are many reasons for this: customers may change their minds, products may not work or fit the description, returning packaging is part of the contract, etc.
Processing
The supplier processes the return and decides what action to take. Typically, companies create a returns policy to determine how they handle returns (B2C) or include an appropriate section in the contract (B2B).
Shipping
If a return is approved, the goods are shipped back to the supplier. While B2B scenarios may be very different due to their volume, transportation in B2C is usually arranged by the retailer, and customers have a choice of pickup options.
Inspection
The supplier receives the returned items and inspects goods for acceptance or rejection (mostly if the goods don't comply with the customer agreement).
Action
Returned items can be repaired and sent back. Very often, these are reused, resold, or recycled. Many stores in e-commerce offer credit or refunds.
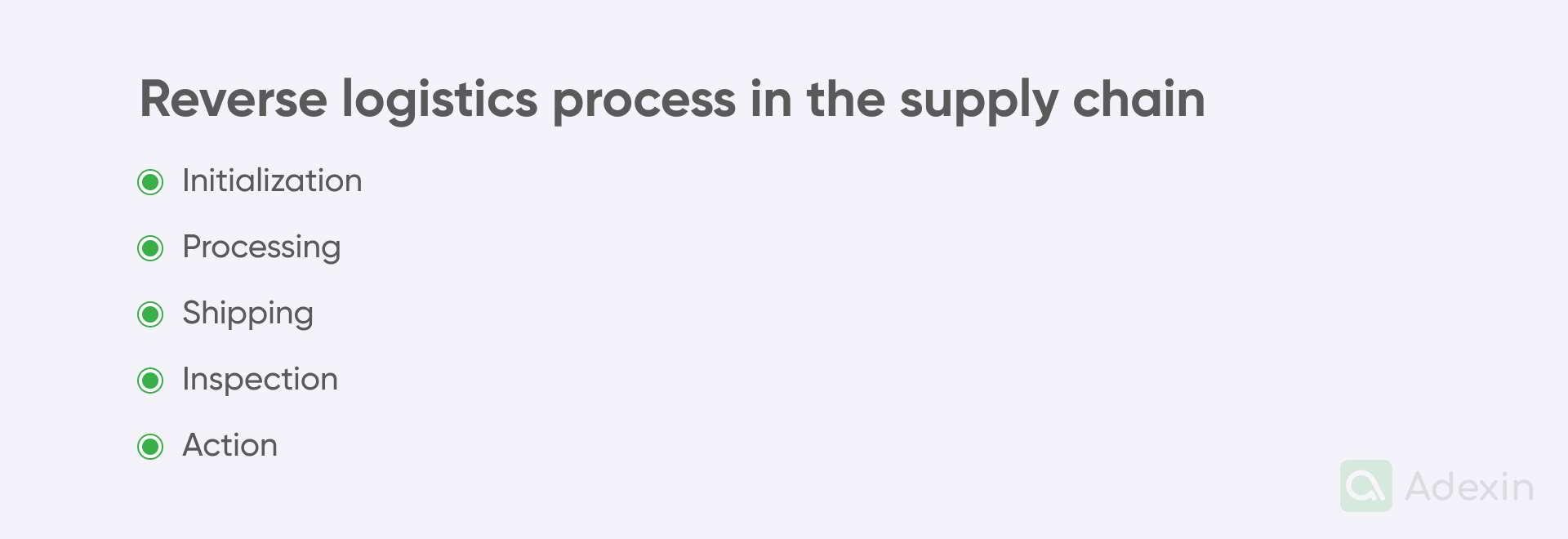
What are companies with reverse logistics?
There are several examples of companies that are using reverse logistics. Due to the nature of their business, these companies strategically rely on this kind of material flow. Regardless of the industry, all warehouse and distribution facilities that use returnable packaging material and modular packaging systems are eager to process shipments in reverse logistics to retrieve their packaging material and ship another volume of goods.
Here are examples of returnable packaging materials in reverse logistics:
• Metal or plastic pallets
• KLT boxes
• Steel pallet racks
• Trolleys
• Carton boxes with foam filling (often very expensive packing material)
Reverse logistics is not only about packaging material. All the packing modules used by a particular industry highly depend on the product characteristics. So, in the end, this is what shapes the reverse logistics process. Although it's very popular in e-commerce, reverse logistics can be observed in various industries.
Here are the industries and companies that use reverse logistics:
Food and healthcare industry
Reverse logistics is finding applications in the food and healthcare industries, which are strictly categorized as Fast-Moving Consumer Goods (FMCG) sectors due to the short life cycle of their products and high requirements for storing and transporting goods. These goods often require low temperatures and need to be shipped and stored in refrigerated conditions. Food and drugs, as well as other medical applications, must be shipped specially, with KLT boxes and protective packing materials to prevent temperature fluctuations and damage. Reverse logistics can also help minimize the remaining 40% loss of products in the food industry during the retail and consumer stages. [3] A notable example in the healthcare sector is Stryker, a medical company that constantly provides new specialized equipment to hospitals for surgeries. Thanks to the high quality of their materials, medical items are often returned from hospitals that haven't fully utilized them, allowing Stryker to recycle them.
Hi-tech industry
In the hi-tech industry, reverse logistics is closely related to e-commerce and encompasses most of the goods flow. It is used simultaneously for both B2B and B2C, providing a rapid way for retail customers to return purchased goods. At this stage, goods flow can involve these operations:
• Returns
• Recalls
• Repairs
• Repackaging
• Recycling
The returns process is relatively time-consuming and labor-intensive, involving multiple touchpoints along the way. It requires strict return control with extensive involvement from customer services to handle the entire process.
A prime example of successful reverse logistics deployment in the hi-tech sector is the Seagate company from the United States. They are renowned for producing high-quality hard drives for entertainment and supplying DELL computers and healthcare equipment. Seagate offers cost-effective options for purchasing new goods when returning old products of the same brand, which are later refurbished and often sold as new ones.
Military
Reverse logistics is no less popular in military units. It often involves operations that require a continuous supply system for providing and exchanging spare parts across various locations. This system is also frequently used for humanitarian purposes, where various goods are shipped to areas needing immediate aid. However, due to the underutilization of the entire aid, such as food supplies, these items are often returned to military distribution units.
A notable example of reverse logistics in the military is North Atlantic Treaty Organization (NATO), where many countries utilize it to support maintenance operations for equipment, vehicles, and more. One of the prominent applications of reverse logistics in the military was evident during military operations in Afghanistan, where NATO units consistently supplied spare parts to their allies.
Cost-effective management with reverse logistics software
Reverse supply chain has become an essential component of the logistics business. It is largely due to the increased complexity of transportation requirements, which involve the flow of goods and a system for returnable packaging materials. This complexity has driven many companies to opt for custom software development that supports transportation. Only companies capable of offering real-time data tracking, maximum transparency in internal operations, and goods traceability can effectively manage reverse logistics.
Cost-effective management within reverse logistics is facilitated by software, as it enables the tracking of primary operations and goods flow. Here are the areas where custom software can support reverse logistics:
Access to comprehensive digital Returns Management Platform.
Automated returns monitoring.
Technology for convenient access and collaboration.
Insights into the causes of returns.
Data analysis for future returns management.
Predictive data.
Improved brand reputation and customer retention.
Optimize your returns logistics based on system features
Reverse logistics can also help prevent business problems that arise from global crises like the COVID-19 pandemic in 2019. Keeping this situation in mind, we have seen a dramatic increase in online sales in e-commerce, leading to a significant surge in returns. Only on the US market, it was up to 30% alone. It had a direct impact on a much higher volume of goods flowing through the reverse supply chain. [2].
Refers logistics software systems can significantly help optimize business operations:
Optimizing Returnable packaging
Goods are often returned in packing material that is very expensive (KLT boxes, steel pallets, etc.). Keeping track of these helps save costs and also plan deliveries more precisely. Many goods cannot leave the warehouse if they don't have the required special packing materials. Labeling boxes with barcodes allows tracking and tracing the same boxes as goods.
Optimizing Shipping planning
Before goods are shipped to recycling or recovery centers, it requires the collection of a higher volume in distribution. RL software capabilities should allow for detailed shipping planning and forecasting to better manage warehouse space and free space on the trailers.
Optimizing Load
Process optimization with RL software involves packing material planning at the unit level, allowing for better space management for loading and routes.
Optimizing operations with data collection
Using RL software, you can flexibly optimize returns based on product number RMA, monitor customer behavior, and classify customers.
Tips for reverse logistics startups
Many logistics companies that want to dive into effective planning should consider implementing reverse logistics. Here are a few tips for reverse logistics startups:
Clean return policy
Make sure the return policy is well-defined, with all information easily accessible. Don't forget to inform your customers about return deadlines, situations, and available options.
Streamline the process
Make returns effortless by providing prepaid labels and consumer-friendly online portals. These can reduce issues between purchasers and sellers and increase buyer loyalty.
Take advantage of technology
Consider taking advantage of the era for efficient returns based on software development, including inventory control systems, barcode scanners, and RFID tags to save time and improve accuracy.
Analyze and optimize
Frequently evaluate and optimize the overall performance of returns logistics by monitoring key metrics. Thanks to this, you can identify areas for development and ensure a better customer service experience.
Get a 3PL partner
To exceed your operability, you can partner with a third-party logistics company (3PL) that specializes in reverse logistics. You can use their know-how and resources while focusing on your medium-sized retail business.
Final takeaway
Effective management of returns logistics is made possible through software that offers compatible features. These can be deployed by digital returns management platforms, which automate returns monitoring.
These are not the only options that can help you optimize your reverse logistics. You can request various features that can match your exact business needs. You can benefit much more from transport management solutions also for other business areas by using custom software development.
Adexin is helping companies in the transportation sector with solutions that can improve your transport operations. Whether you want to optimize your reverse logistics or other areas, we have expertise in the transportation industry with proven solutions that have helped many companies. Contact us today, and let's see how we can optimize your business operations for transport with custom software development.
References:
[1] Reverse Logistics Strategies and Their Implementations: A Pedagogical Survey; Retrieved from: https://libres.uncg.edu/ir/uncg/f/J_Bhadury_Reverse_2004.pdf
[2] Reverse logistics Managing supply chain disruption amid COVID-19; Retrieved from: https://www2.deloitte.com/content/dam/Deloitte/us/Documents/process-and-operations/reverse-logistics-pov.pdf
[3] Reverse logistics and its application to the FMCG sector in Kenya; Retrieved from: https://fieconsult.com/reverse-logistics-and-its-application-to-the-fmcg-sector-in-kenya/