Efficiency in logistics is always moving in parallel with technology and automation. It's about minimizing human manual impact in favor of deploying modern solutions that are leading to improvements in performance. Among those, logistics businesses can excel once they implement software instead of MS Excel. It's a simple replacement but can automate and digitalize most of the actions related to logistics, such as transport booking, freight procurement, reporting, and much more than you can even believe.
As a manager, whether a small or medium-sized business or more significant, let's say, enterprises that offer fulfillment processes, like DHL or Raben from the middle of Europe, the sort of logistics problems remain the same, so you see where you need to put higher pressure on performance and logistics efficiency improvement. This article will provide some examples of how companies can improve their logistics efficiency through various strategies. We will also show how you can handle it internally through a good partnership with third-party custom logistics software solution providers. Let's see how to achieve this and make your business efficient. Read the article below!
Leading indicators of efficiency in logistics and supply chain management
Logistics efficiency can be perceived in different ways, and activities in this direction can lead to the same results due to different strategies, it is important to choose your unique algorithm. As a manager, you really focus on setting up key performance indicators. For you, it is evident that at the end of each week and each quarter, you want your business to remain efficient in terms of what was agreed between you and your customers.
KPIs in logistics outline truly where you need to focus on improvements. So, we may say that typical logistics businesses focus on certain KPIs that indicate performance. By understanding your KPIs, you get a clear view of where you need to focus more to gain more efficient logistics operations. Below, we share a KPI hit and improvement strategies to prevent them and increase efficiency in your logistics.

1. On-time shipping for logistics efficiency
On-time shipping is the KPI hit that indicates late Shipping versus on-time Shipping, which evaluates the total number of shipments that left the warehouse, contrary to the shipments that were not shipped on time. There are multiple reasons for that. Your outbound team can, for example, damage the pallet during loading, so they need to restack it before Shipping. It can take up to even 30 minutes to do so. Your shipment will be delayed, so delivery will be delayed.
It has multiple consequences, as your carrier will probably charge you more for the late load, and they can even leave without your pallet on the trailer. The shipment can be delayed to the next pickup. So, you got a serious KPI hit that time, and this is where you need to dive into an investigation to evaluate the root cause and search for where and how to make it more efficient and prevent damages. You have a KPI hit that drops your performance to 2% based on the entire volume of the shipped pallets.
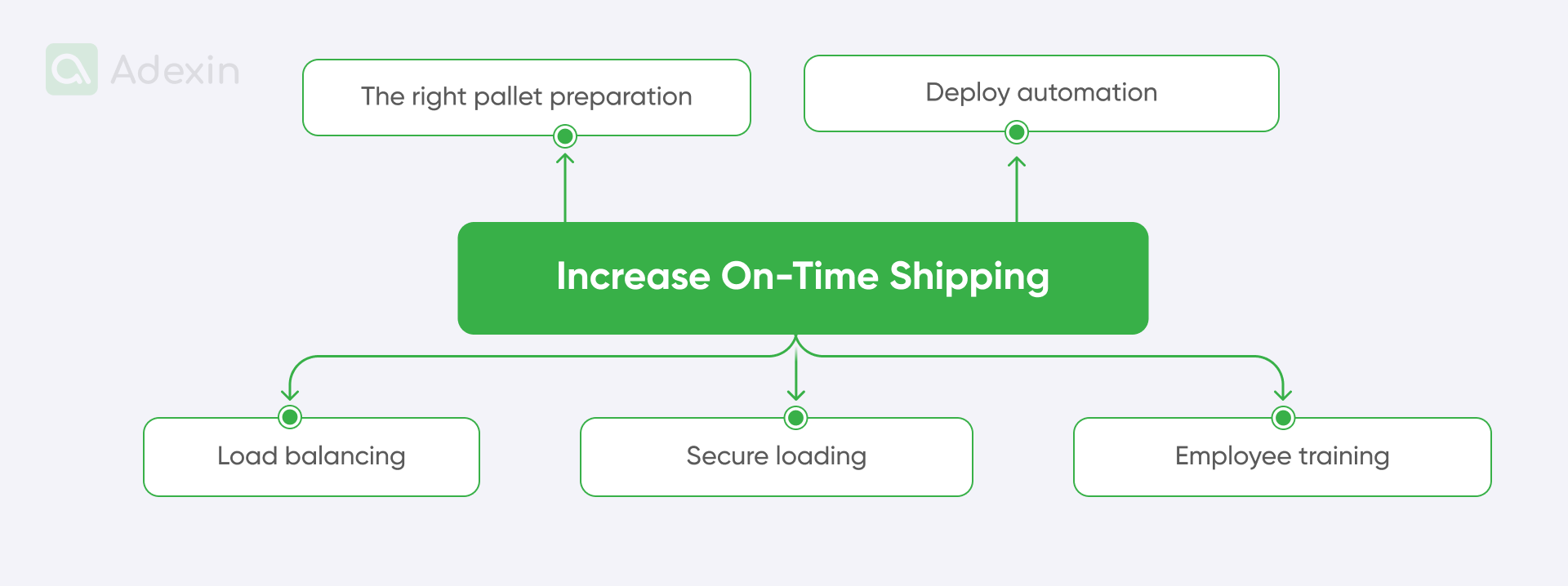
Having in mind all the above, how can we increase on-time shipping efficiency? Optimize your loading process at the docks:
The right pallet preparation. Ensure the pallets are in good condition and of appropriate size and weight capacity. This will prevent them from breaking and help the forklift driver fit them into the trailer or container more easily.
Load balancing. Distribute weight evenly across the pallet to prevent instability because it can fall on the side once the forklift lifts it.
Secure loading. Use proper strapping and sealing methods. You can shrink wrap or use other securing methods to prevent items from moving while loading.
Employee training. Regular training on safe and efficient loading techniques is crucial. People need to know how to handle the loading process from beginning to end.
Deploy automation. Robotic arms for pallet staging allow you to build excellent pallets. The robot's sensors can make pre-load inspections, where they inspect pallets and products for damage before loading. As robotics run on software, they can run random pallet audits to conduct random checks of loaded pallets to identify potential issues. Robotic arms are situated on ergonomic workstations, where people have less access, and this creates a comfortable and safe work environment to reduce fatigue and errors. Actually, robotics arms and supportive software can secure the end-to-end process from the right pallet preparation and secure loading to load balancing, lowering the need for people involvement and thus lowering the need for training.
2. Incorrect destination to improve logistics efficiency
This KPI hit is about wrong delivery, and the most popular root cause for this is mixed shipping labels. So, your shipment could be delivered to someplace you don't want because carriers thought it was the right place to unload. It doesn't matter; your customer doesn't care about it. Mostly, it is about paperwork where admins or clerks from the operations support group don't pay enough attention to taking care of your shipping documents. In other cases, the carrier can also deliver your pallet to the wrong destination, leading to another KPI hit, which might also be late delivery. In this case, we have multiple root causes: mixed documents, wrong shipping labels on the pallets, or poor carrier shipping service. As you may see, this issue comes from a minimum of three different groups of operations, so there is quite an extended field for searching for improvement to increase logistics efficiency.
Avoid incorrect destination KPI hits and get better logistics efficiency through:
Label verification. You should implement a double-checking process for labels.
Reverse logistics and returns management. Invest in return policies and processes.
Barcode scanning. Use barcode scanners to verify label accuracy.
Label printing quality. Ensure clear and legible labels every time. Sometimes, codes are poorly printed, so people try to check data manually. This takes time and is error-prone.
Label placement. Labels should be in the same spot on the pallet. Standardize label placement on pallets and keep them, for example, in the upper corner of the pallet.
Better carrier selection. You should evaluate carrier performance better and choose reliable partners. You need to check how responsive their customer service is and look at other records on shipping accuracy.
Get better service level agreements (SLAs). Establish clear expectations with carriers and validate them with KPIs for higher logistics efficiency.
Get better performance monitoring. Track carrier performance and promptly address issues using custom features in your Transport Management System. Don't know how to do it? Ask us at Adexin, as we have a long track record of helping logistics companies increase their efficiency by improving logistics management processes through software development.
Get custom technology with a warehouse management system (WMS). Utilize a WMS system to track inventory and shipments.
Get a competitive advantage with a transportation management system (TMS). You can optimize transportation planning and execution with a transportation logistics management system. As we said above, get your partner for custom software development and start this process even now to lower errors in your business.
Get your labeling software. You may also invest in accurate and efficient label-generation software. Software for labeling like NiceLabel (known now as Loftware) is quite expensive. However, you can get this feature with your custom TMS system at once. So, think about the benefits you may obtain with one custom software development partner.
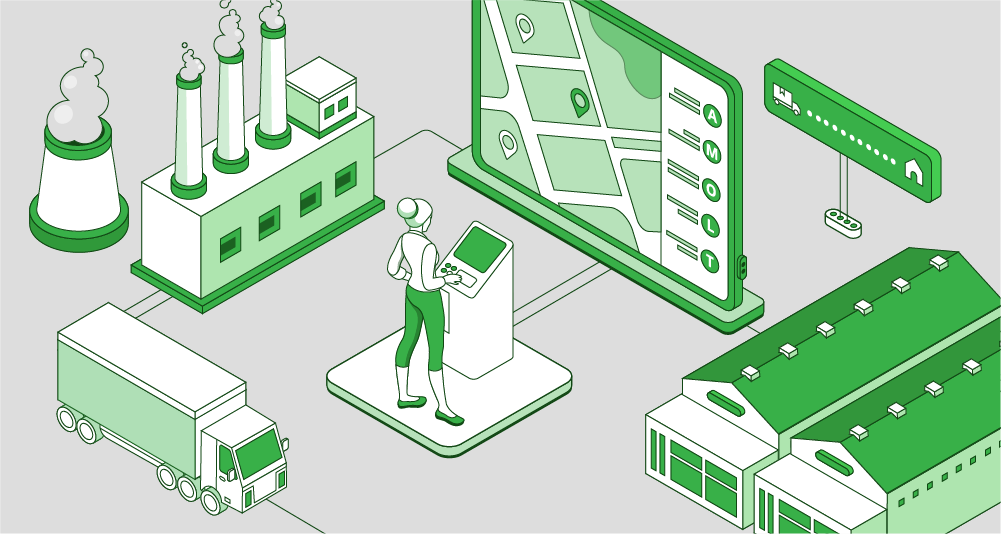
3. Documentation errors as a drawback in supply chain efficiency
Documentation errors KPI hit refers to inaccuracies or inconsistencies in the paperwork associated with logistics operations. Here, your clerk from the office can bring many reasons for handling docs poorly. However, carriers and all other stakeholders can also contribute to the root cause. These errors can occur at various supply chain stages, including order processing, shipping, receiving, and returns, so there are so-called touchpoints everywhere.
Human manual errors can happen everywhere where documents are produced, reprinted, corrected, and so on. Common examples include incorrect product descriptions, quantities, shipping addresses, or missing documentation altogether, but the most serious is a mixed tracking number. Just imagine how often people send emails with long 14-digit tracking numbers when one or two digits are incorrect. All people in the entire chain of emails are confused. Such errors can lead to delays, customer dissatisfaction, and, frankly lowered customer experience, and of course, financial losses because your customer doesn't care. They'll give you a KPI hit "Documentation Errors' because they know your team has failed.
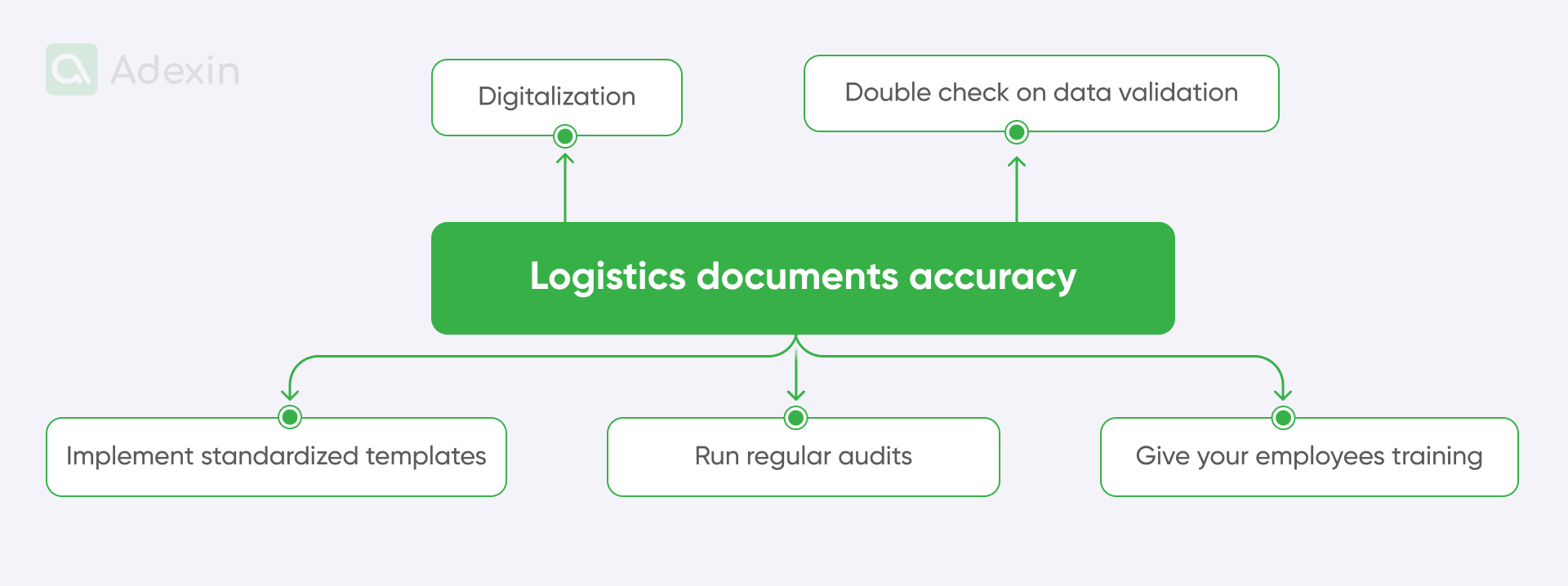
Get your strategy for more accurate shipments with document accuracy and management including:
Implement standardized templates. Make sure that your people have ready-to-use templates that provide consistent formatting and information capture, with, for example, OCR, to identify issues. So, for this purpose, you may need a DMS system.
Double-check on data validation. Your admin clerks should implement checks to prevent errors during data entry. Nothing will do this better than an auto-check run by document management software integrated with order management or inventory management systems. Such a DMS system can evoke queries from inventory stock to check if your people haven't filled in incorrect values in the documents. The system can check the factual status against data on the document to prevent discrepancies.
Digitalization. As mentioned, you need to explore more profoundly electronic documentation solutions to reduce manual handling and errors. In this case, you can even hire a custom development software partner to help you transfer your data to digital format and provide shipping document management systems, for example. At Adexin, we developed a blockchain-based custom DMS system for one of our clients, eTEU. So we know how to set up your business and move to a more digital format.
Run regular audits for logistical efficiency. Last but not least, you need to conduct periodic reviews of shipping documents to identify and correct issues. If you require this, your DMS system can do it. The advanced software can scan every document to capture discrepancies.
Give your employees training for higher logistical efficiency. Provide clear guidelines and training on document handling to your people. Even software cannot do everything. Admin clerks need to know and understand shipping documents and other processes, such as customs, to know what they are doing.
4. First-in-first-out (FIFO) violations
Yes, this KPI is entirely connected to the manufacturing industry, but it is not always. Simply said, your team needs to utilize goods for production that came first to the warehouse, and when it's a distribution center, they need to ship goods that were inbounded first in the first place. All operations are traced on behalf of your customer (of course, all that depends on the contractual agreement), so if they see what's going on in the warehouse, they can assess that your internal movement was wrong. You cannot run away from the responsibility of this situation in front of your customers.
What is the root cause? Let's say wrong staging during the receiving process. You may receive two pallets; one is with FIFO, and one has no status at all. So, your people in WHS are obliged to shrink space, and they start with the staging process and mixing FIFO boxes with everyday items. You get a new pallet that way, which is moved to the racks in the warehouse. Next to it, they don't take FIFO items but take them from other pallets when it's urgent shipping. You get a KPI hit for FIFO Violations.
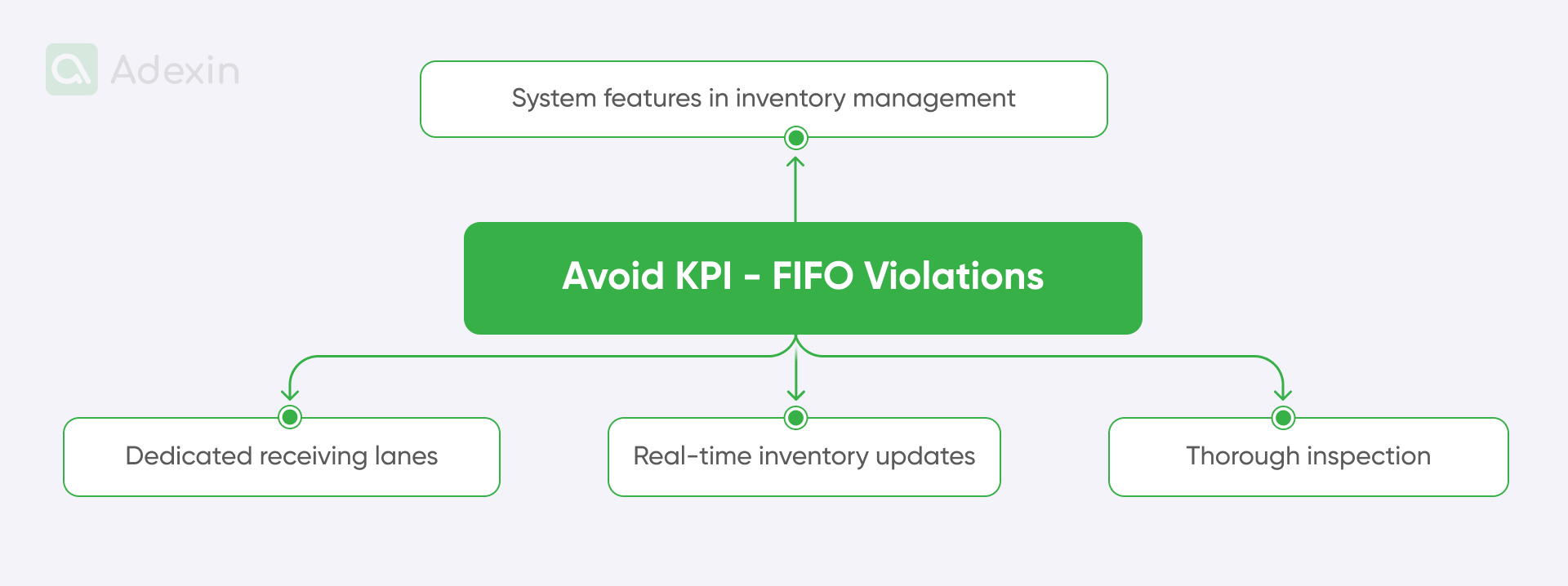
What can you do to avoid this KPI? See the strategy we propose to minimize the impact of FIFO violations:
Dedicated receiving lanes. We highly recommend creating separate lanes for FIFO and non-FIFO items.
Thorough inspection. Verify the accuracy of incoming goods and their FIFO status. It's worth noting that the software can also handle inspection. You can use the software to make cycle inspections during cycle counting to check if the right stock is stored where it is supposed to be on the racks.
Real-time inventory updates for better order fulfillment. Here, you can implement a system to update inventory records immediately upon receipt. It is possible only within an IM system.
The system features in stock management. We at Adexin can build an inventory system for you that will include system features to divide stocks dedicated to FIFO. This means that all shipping you'll have, according to FIFO principles, will be handled system-wise to exit goods dedicated to higher customer satisfaction in the first instance. Its feature can also be easily used for manufacturing to deliver, let's say, raw materials with a FIFO schedule to production lines. All that inside of the inventory management system made by Adexin.
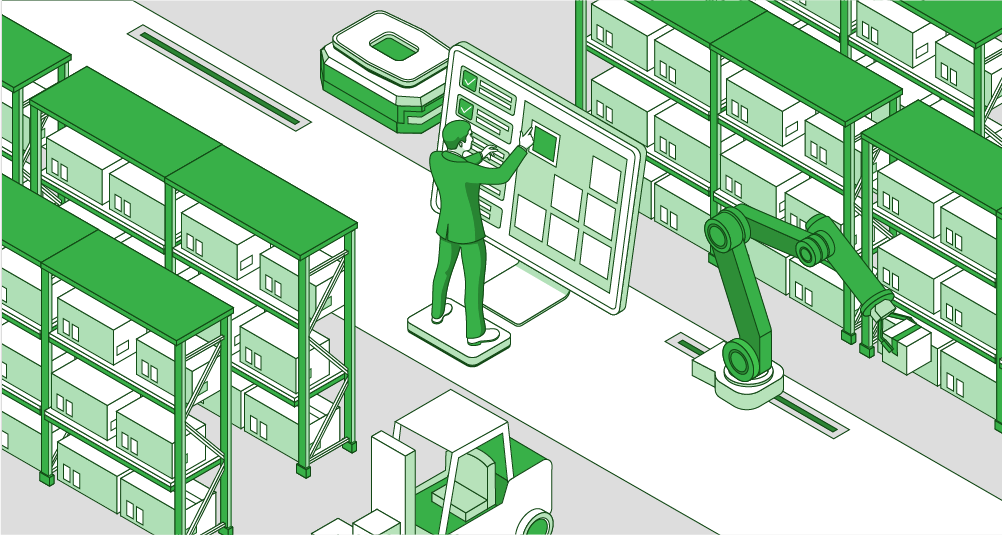
5. Inventory discrepancies: get your custom inventory management
This KPI hit "Inventory discrepancies" arises when the actual quantity of a product on hand differs from the recorded quantity in the inventory system. Some companies don't have well-settled processes, and mostly happens during the receiving process, where your people handle goods from containers or trailers, and they record the wrong quantity. It is the root cause, which can result in stockouts, overstocking, inaccurate sales/demand forecasting, and financial losses (again, you get a KPI for Discrepancies). Frankly, discrepancies can be caused by various factors, such as inaccurate order entry, theft, damage, or errors during physical inventory counts. Still, again, the most common is during the receiving process. This whole situation leads to multiple mistakes along the way in the delivery process. Your customer gets the wrong quantity, and they complain to you.
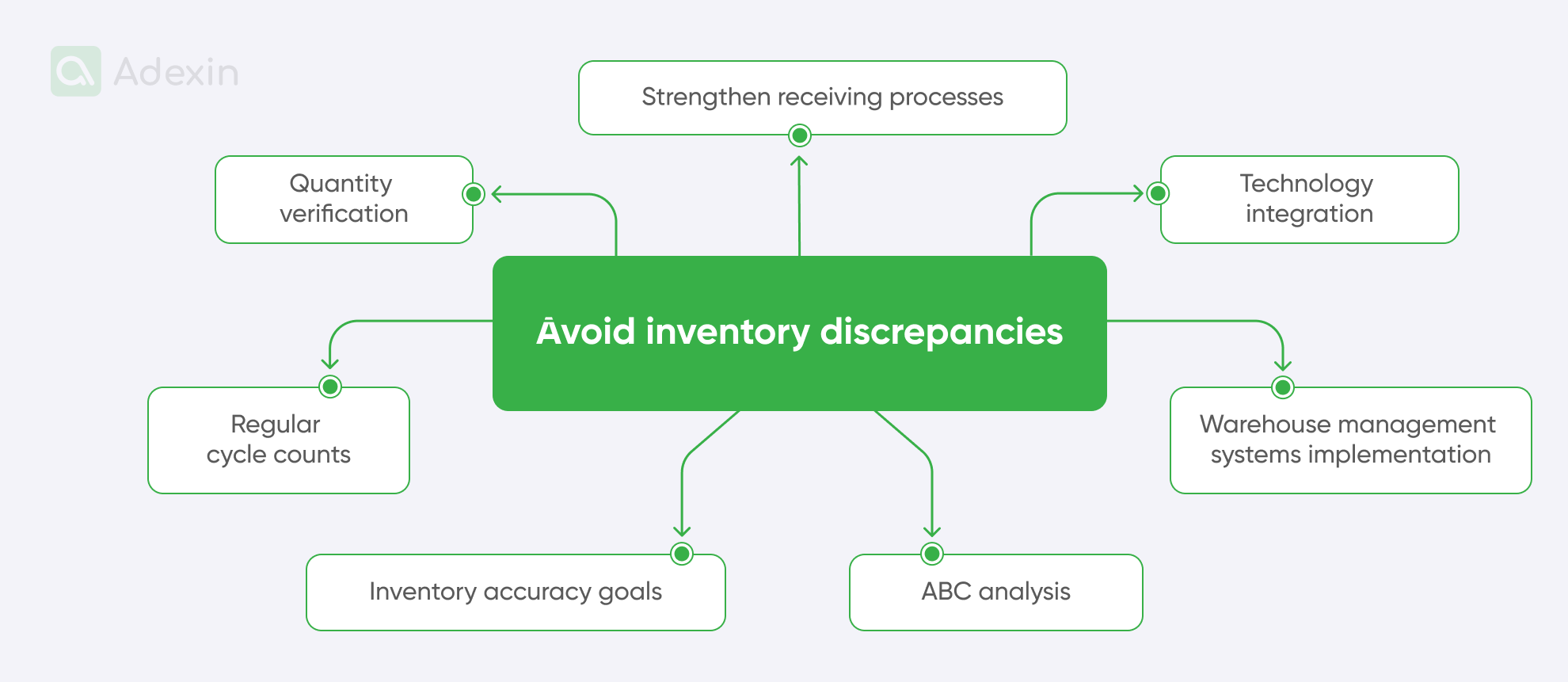
Let's look into this draft of the purpose by strategy for limiting the occurrence of "Inventory Discrepancies" KPIs:
First, strengthen receiving processes with detailed receiving procedures. Your warehouse must establish clear and standardized delivery procedures. No matter what kind of goods you're handling, you need to outline step by step what to do next to avoid errors and mistakes.
Quantity verification and logistical efficiency. Here, we propose implementing rigorous quantity checks upon receipt. The best option is to create an efficient logistics process for double-checking that includes random audits. It can make people at the first line of the receiving process aware that all they do can be quickly verified. As a result, you can encourage people to make an extra effort to avoid errors.
Technology integration to improve logistics efficiency. Obviously, we advise using barcode scanners or mobile devices to improve accuracy and speed. These should be integrated with inventory software to handle contactless receiving processes and increase accuracy.
Regular cycle counts. Use custom software to conduct frequent physical inventory counts to identify discrepancies early.
Inventory accuracy goals for logistical efficiency. Set clear targets for inventory accuracy and monitor performance. It means you can create a bottom line to help verify all the processes based on percentage indicators.
ABC analysis for effective logistics management. This is not a new solution, but ABC analysis can prioritize inventory control items based on value to determine counting frequency. So, you keep an eye on the most expensive items internally and maintain good quality control.
Warehouse management systems implementation. Well, this is what we can propose as the first and last solution simultaneously. As a software house at Adexin, we always advise considering a warehouse management system to automate inventory tracking. With us, it can be even better and more efficient with custom features we can provide.
Other common issues based on KPIs are Damaged Goods, slow Response Time, or Incorrect Shipping information in the system. Knowing the root cause and analyzing historical data can help you better solve these issues and implement strategies for efficient logistics management.
Are you in search of a reliable tech partner?
Adexin can help with advanced logistics solutions
Contact usConclusions on logistics improvement
Well, let's summarize. By implementing these strategies and leveraging advanced technology, a warehouse can significantly improve inventory accuracy, reduce transportation and warehousing costs, and increase overall operational efficiency. As you may see, there are many benefits. So, a well-organized receiving process, regular cycle counts, and a robust WMS are the foundation for an effective inventory system and logistics management in general.
To not exceed that content, we believe we have proven our experience here in increasing logistics efficiency. If you're ready to optimize your inventory management or other parts of logistics, contact Adexin today. It's time to discuss your specific needs and learn how our WMS, TMS, and DMS solutions can transform your warehouse operations and strive for better efficiency.