Lack of automation can have a knock-on effect on most warehouse operations. Many warehouses and distribution centers were designed for a single purpose a decade ago. Throughout all that time, their managers have made only minor modifications to cope with dramatic business changes. Most likely, there needs to be more technology-heavy approaches, and most businesses in the supply chain are running on classical transaction-based ERP systems.
From our experience, we know that ERP systems tend to reduce flexibility. Their operational modules are quite limited, also because many companies don't update their ERP systems even after 15 years. Therefore, what people in the warehouse must do and can do is also heavily limited. To tackle issues with ERP system stiffness, many modern supply chains demand systems to support outbound operations, such as warehouse labeling systems.
In this article, we had a unique opportunity to get insights from Rolf Giesbertz, an expert in labeling system integration from Giesbus.nl in the Netherlands. The company excels in integrating barcode label systems from Loftware, a worldwide provider of end-to-end cloud-based labeling platforms. See more in the article below, and don't miss your chance to learn why warehouse labeling systems are so crucial for your business.
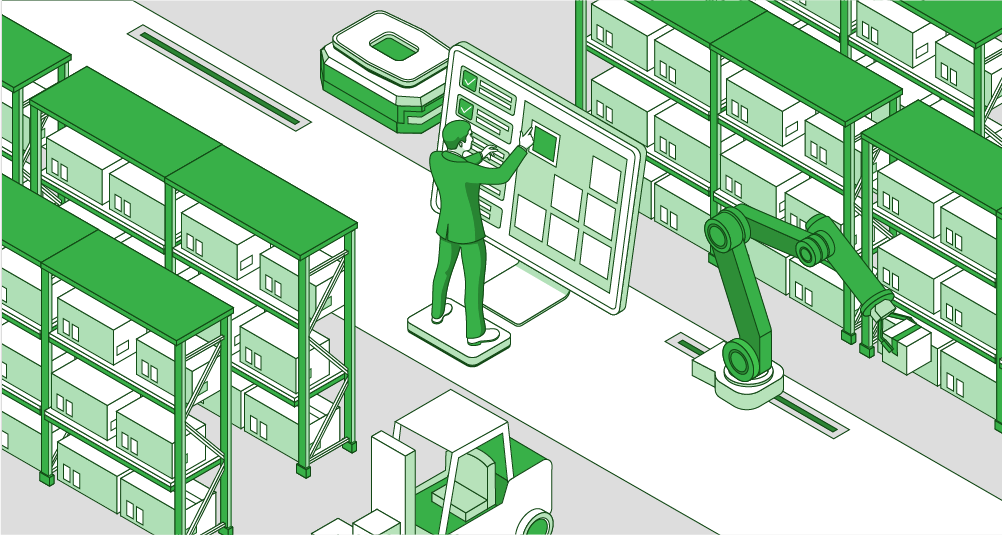
What is a warehouse labeling system?
A labeling system is one of the vast components of a warehouse automation structure. It assists with packaging procedures for inbound and outbound goods by labeling and marking them in a structured way according to the standards of systems integrated with it. Most commonly, a labeling system is integrated with ERP systems such as SAP, Oracle, or warehouse management system (WMS), but this doesn't mean these are the only solutions that can be integrated. Some companies, such as Loftware, provide cloud solutions with pre-built integrations, as well as Microsoft Dynamics 365 for Supply Chain. This way, warehouse users can print directly from the ERP system into their specific print environment.
Incorporating label-based automation is a valuable component of entire solutions, which can be a WMS system or ERP itself. In the long run, this approach has many benefits, such as increased accuracy, traceability, and compliance, while improving labeling quality, and speed, and improving the efficiency of warehouse workers.
What types of warehouse labels do we have? We recognize floor labels that support warehouse operations in general. Others, such as magnetic labels are often used on warehouse racks because they are easy to replace. There are hundreds of labels to identify products with various types of specific applications. See below for some examples:
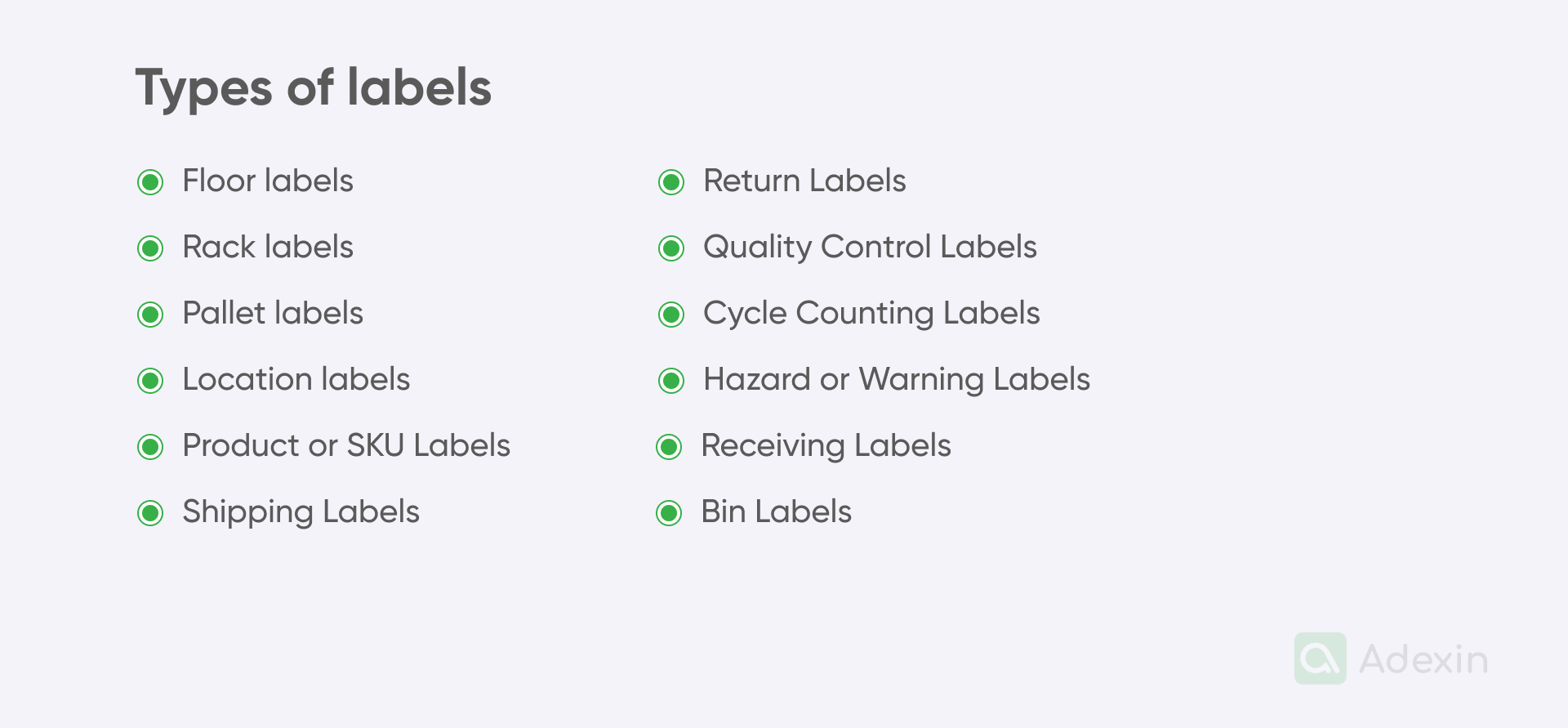
Why do you need labeling and barcode labels?
Since labeling isn't integrated with the ERP system, employees must perform manual tasks. Workflow procedures are more complex because producing and printing barcode labels in the warehouse is more complicated. Referring to whose actual Loftware's experience workflow applies to many less-advanced warehouses, we can see that this involves several issues:
Misplaced or lost inventory
Incorrect labels. If warehouse labels are incorrect or contain errors due to a lack of data retrieved directly from the system, items can be placed in the wrong locations. This issue often occurs during the inbound process if labeling is handled manually once goods arrive at the warehouse.
Lack of standardization. There may be inconsistencies between different departments or locations without a standardized labeling system. Navigating the warehouse inventory can be difficult, contributing to misplaced items.
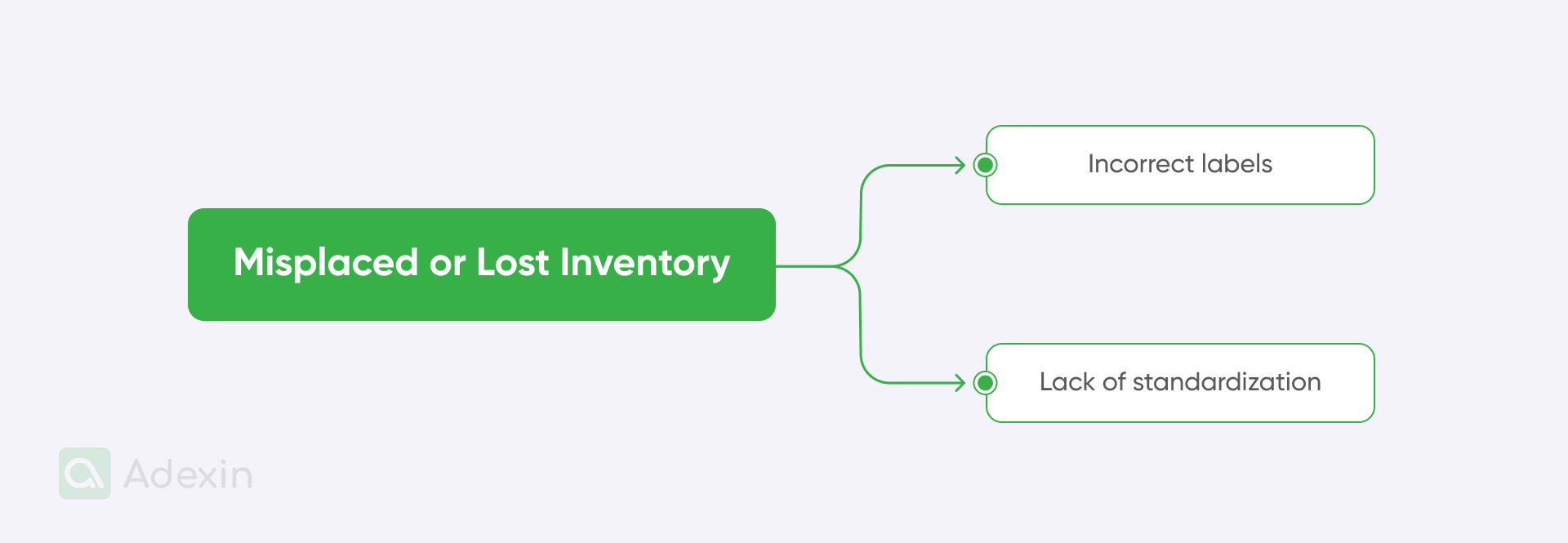
Low-quality rack labels
Confusing labels. Warehouse labels that are similar in appearance or difficult to read can lead to pickers selecting the wrong items. Most companies are unable to differentiate their appearance.
Incomplete information. If warehouse labels do not contain all the necessary information, which can result from manual data entry in Excel, such as item number, quantity, or location, pickers may make mistakes.
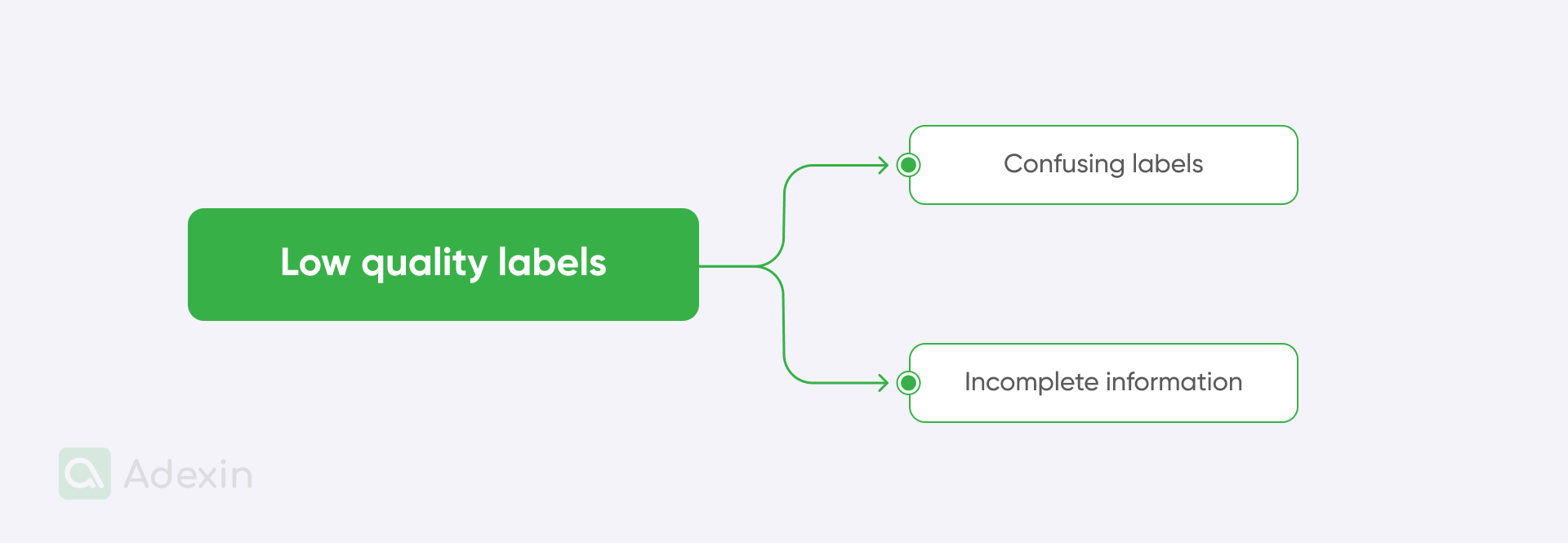
Picking errors
Increased labor costs. Workers spend more time searching for items when they are misplaced or difficult to find. It reduces productivity.
Manual inventory checks. To verify inventory accuracy, manual checks must be in place. Double manual checks are mostly required everywhere, and they are time-consuming and labor-intensive.
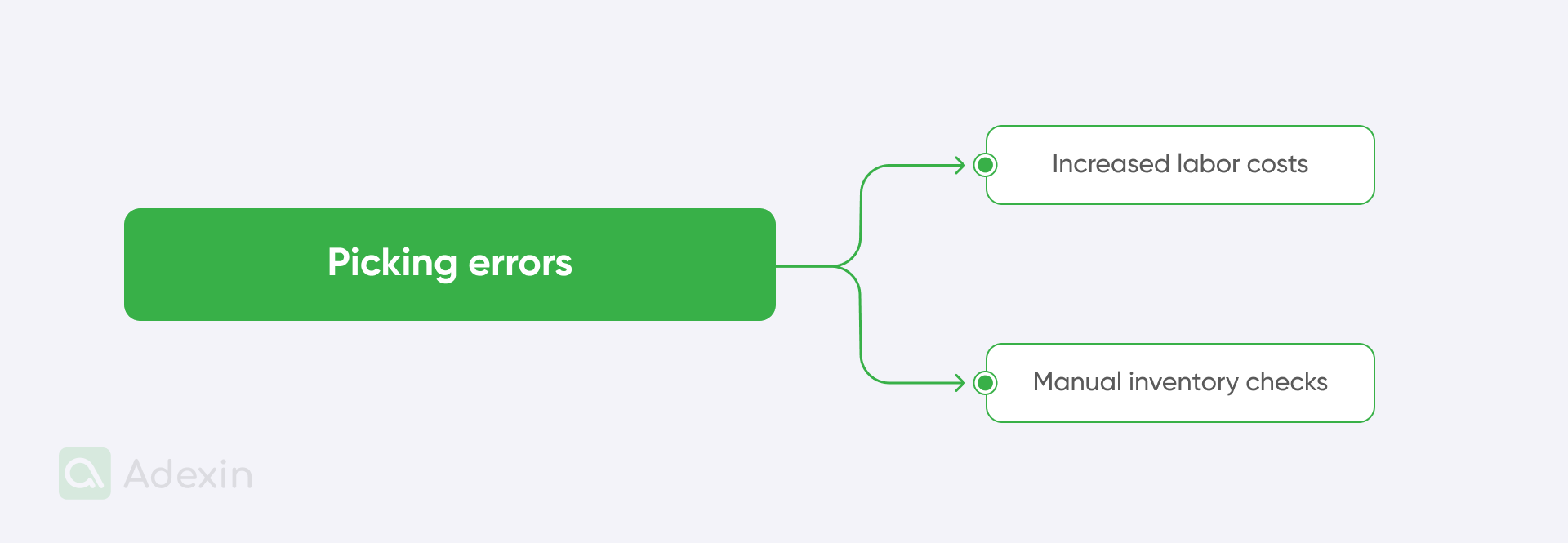
Damaged goods
Incorrect handling. If warehouse labels do not indicate proper instructions, items may be damaged during storage or transportation. It highlights the need for more advanced labeling systems.
Mishandling due to misplacement. When misplaced, they may be mishandled or damaged while being moved or searched for.
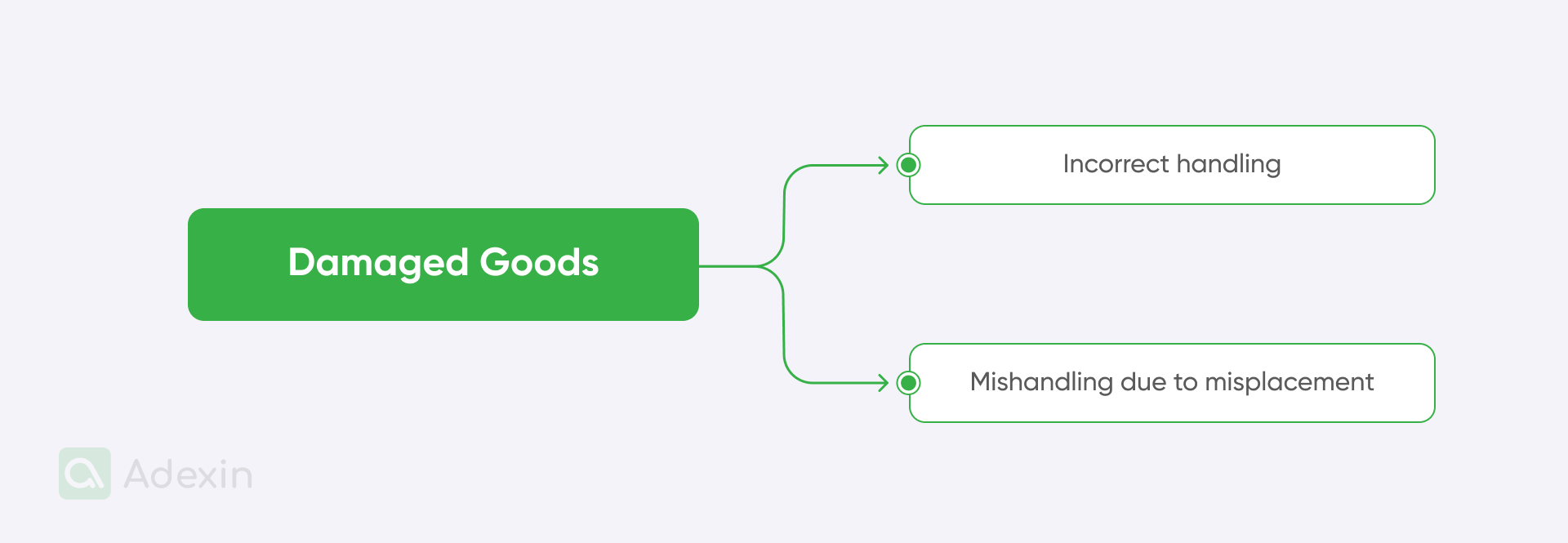
Inventory discrepancies
Inaccurate counts. If warehouse labels are incorrect or incomplete, inventory counts may be inaccurate, leading to discrepancies between physical stock and system records.
Stockouts and overstocks. Inaccurate inventory data can result in stockouts or overstocks, negatively affecting the business.
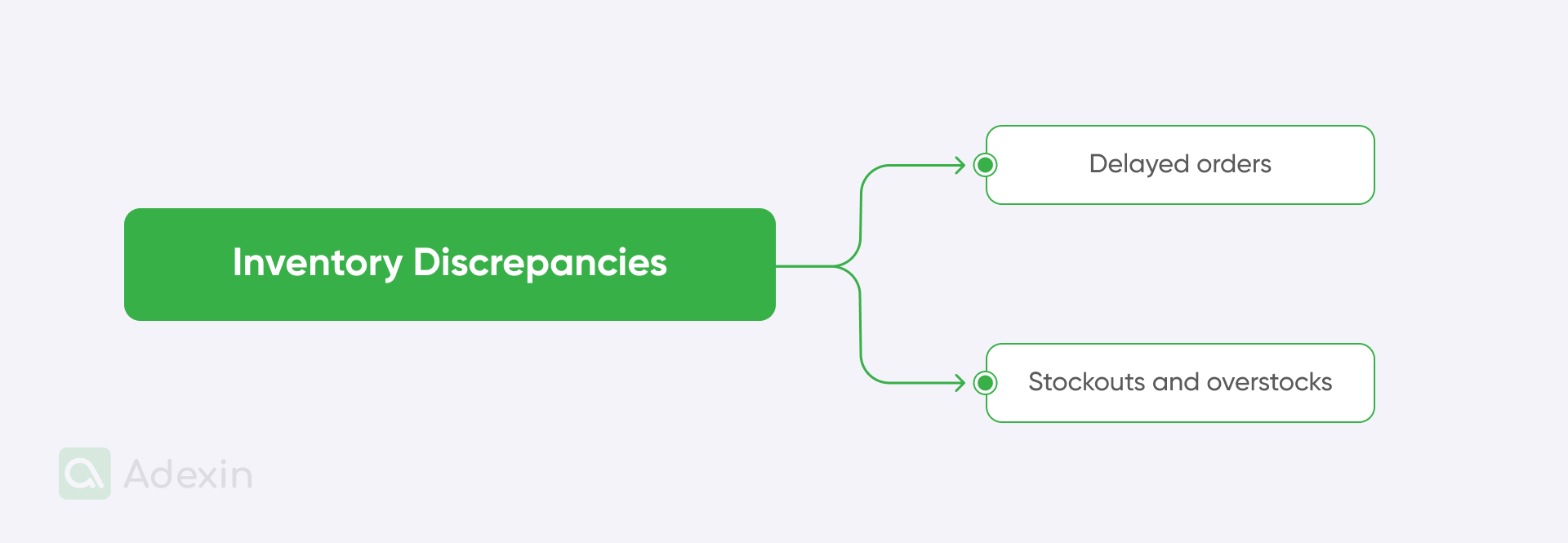
Reduced customer satisfaction
Delayed orders. If items cannot be located or are picked incorrectly, it can lead to delayed order fulfillment and customer dissatisfaction.
Incorrect shipments. Errors in labeling can result in incorrect items being shipped to customers, causing further frustration and potential returns.
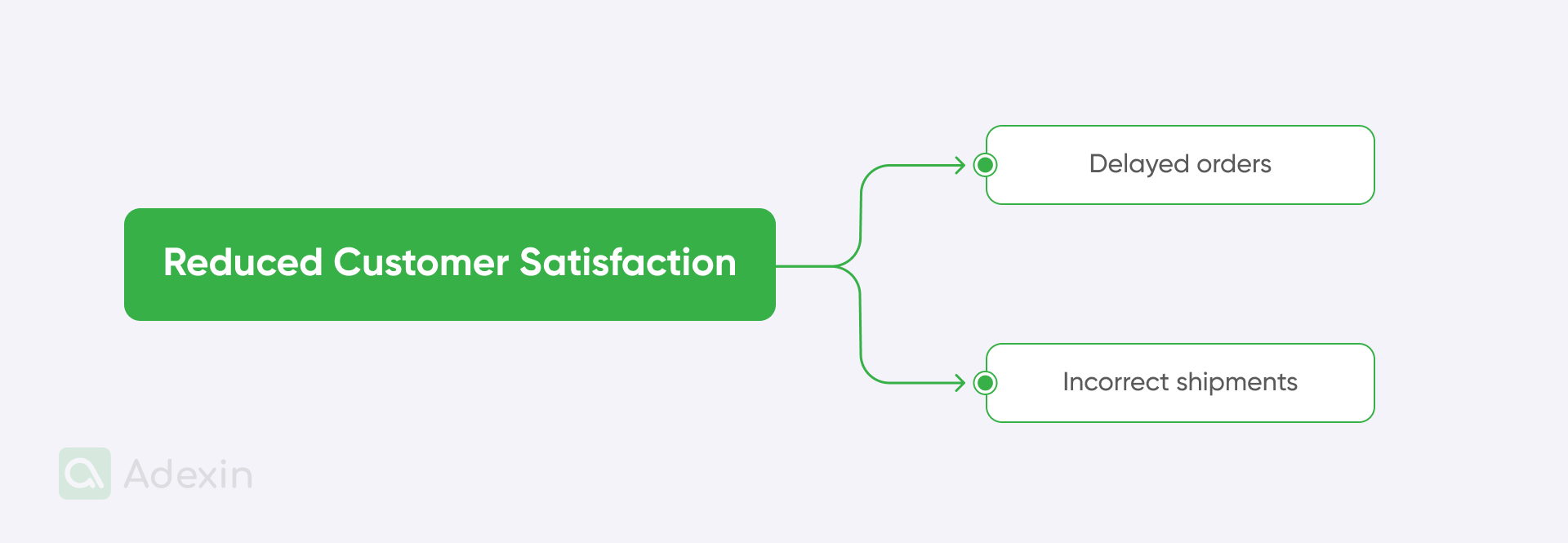
It is important to remember that the warehouse labels system often goes along with the need to implement a barcode system. Industry analysts at VDC report that companies are optimizing their supply chains to be more agile and responsive to customer demand while maintaining profitability. Many businesses are investing in barcode technology to improve operations and reduce costs, as evidenced by 73% of organizations confirming radio frequency identification as a critical investment criterion for their fulfillment centers.
Loftware NiceLabel cases experience
This article covers several cases where the lack of a properly deployed, structured warehouse label system can lead to warehouse inefficiencies. Here are also a few examples shared with us by Rolf Giesbertz integrator of Loftware NiceLabel:
Simplifying the printing process for Eurofast Group
"The aforementioned problems are very common in the supply chain. Looking again at our experience, I can recall a case from the Eurofast Group, which came with a request to simplify the printing process. For this purpose, we implemented 3 Novexx Solutions XLP 604 thermal transfer printers at the Eurofast Group. Driven by Software NiceLabel Cloud, we print all barcode labels linked to the SQL database of Navision Dynamics, again successfully providing a single source of truth. "
Rolf Giesbertz, Business Partner of Loftware NiceLabel
Loftware customer case on integrating ERP and WMS
Without a labeling system, most label information is exported from the ERP or WMS system to Excel format and printed manually. This process remains very time-consuming due to the highly diverse stock. In an example from a customer case with Loftware in a steel stamping facility, color-coded label process cards were used to identify bin contents. The manual production of these cards was time-consuming, requiring 4-5 hours of labor per card.
Using the NiceLabel solution, the Loftware customer successfully unified all label production and printing on a single platform. From now on, they can seamlessly integrate with ERP, ensuring a standardized workflow throughout the company. They created a system that integrates with their ERP database and offers a wide range of functionality.
Simplifying the labeling process for AllNuts
"From our experience, we have worked with AllNuts, a company from Belgium. This company was a producer and distributor in the food industry. They first approached us to review two ALX 924 Print & Apply machines, part of the Avery Dennison ALX 900 series, which are high-performance labeling systems used in industrial environments. They are designed explicitly for print-and-apply labeling tasks, typically used in packaging, logistics, and manufacturing settings.
We discussed with AllNuts how warehouse labels could be simplified. We evaluated their inventory management system, and shortly after, a link to Microsoft Navision was implemented with Software NiceLabel. This solution ensured that the text on the website matched the text on the barcode labels, providing a single source of truth. So, basically, we provided them with a great solution that simplified the labeling process."
Rolf Giesbertz, Business Partner of Loftware NiceLabel
Are you in search of a reliable tech partner?
Adexin can help with advanced logistics solutions
Contact usFinale takeaway
First, we thank Rolf Giesbertz and giesbus.nl for their input on this content. Summarizing the subject, we understand now that manual labeling costs you time, money, and customer satisfaction. What more can we say? Many issues with traditional ERP systems lack the flexibility to manage complex labeling needs. Integrating your warehouse labels system with your existing ERP is a good idea and might be cost-effective, but it can still limit your operations to some extent.
From our experiences, it is clear that it is often much better to develop a custom system integrated with a labeling solution like software. Most likely, upgrades to ERP don't give complete flexibility in operations. We know with 100% certainty that some ERP updates can go wrong and jeopardize all of your business. In terms of time and costs, it is good to get the journey with a custom software partner like Adexin, who knows how to develop an end-to-end custom WMS system or ERP system that will fully integrate with a proven labeling solution from Loftware. Contact us today to see how we can support your business.