The objective of logistics management in a customer-driven supply chain is change management. This term entails an effective logistics approach based on decision-making and operational management shifts. In this article, we want to reveal how to improve logistics efficiency and successfully implement it based on 5 strategies.
Logistics efficiency through shifting in management
Logistic efficiency is explained by logistics management service, a complex task that includes many operations to secure end-to-end logistics processes. How you secure your operations can help you maintain efficiency in logistics or jeopardize your results.
What we have observed over the last years is that effective logistics is the objective of logistics management in a customer-driven supply chain that begins with change management. This is one of the first steps that open up the benefits of various strategies for improving effectiveness in logistics.
What is change management in logistics efficiency?
Change management is the process that describes a logistics company's approach to implementing changes that drive efficiency for both internal and external operations. It includes a very broad spectrum of operations, from human resources management to implementing new processes. Change management is often recognized in certain business areas, often resulting from acquiring new customers in logistics to align with their standard operating procedures (SOP).
There is always some kind of resistance to change among employees, sometimes even towards top-level leaders. I remember a situation where we couldn't effectively implement any change because the leaders of the operations teams preferred to deal with fixing the problems they knew how to fix rather than help us implement the new process.
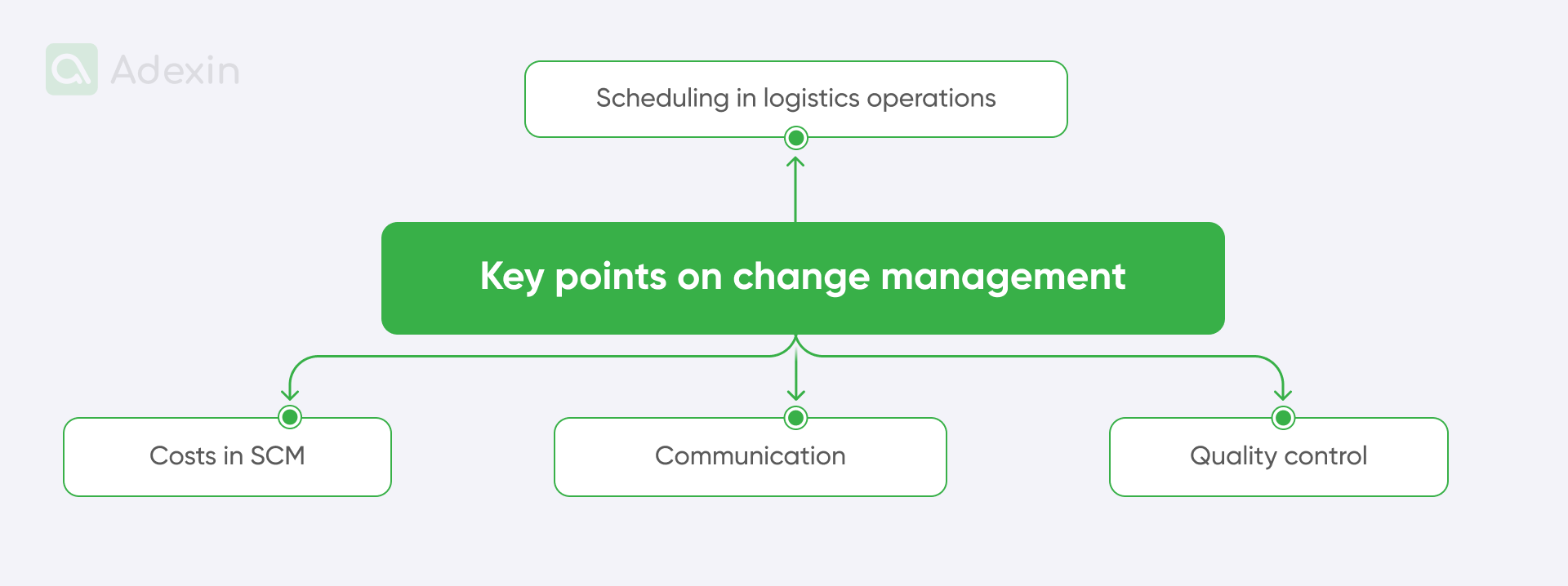
Here are key points on change management:
Scheduling in logistics operations
In many cases, a good schedule plays an important role in change requests. When there are disruptions to daily operations, it must not affect the project schedule. Simply put, if you ask your people to learn a process and they have a lot of work to do every day, there will be a visible scheduling problem.
Overall costs in supply chain management
Labor is usually the biggest cost of a project. This can be seen by the time spent on certain tasks. Learning to change also increases the time to complete the project and, in fact, the cost.
Logistics efficiency & communication
Change management requires active communication among all stakeholders, from top to bottom and around (regardless of whether you have flat organization management). Approved change requests must be effectively communicated to stakeholders at the right time to get higher supply chain efficiency.
Customer satisfaction through quality control
Change requests can affect the quality of the final project and affect customer satisfaction. You should know that no project cannot succeed without a good quality management system. People should have insight into what affects their performance, so add KPIs to exchange customer satisfaction.
Logistics is known for its conservative approach to certain operational aspects, particularly those related to decision-making processes or operations. In many cases, financial market conditions dictate this conservative approach to investments in innovations, changes in management, digital transformation, and all other related areas.
5 strategies to improve logistics efficiency
So, as we discussed above, change management isn't an easy task, but once you cope with it, you will definitely be able to implement strategies that can drive effectiveness in your logistics.
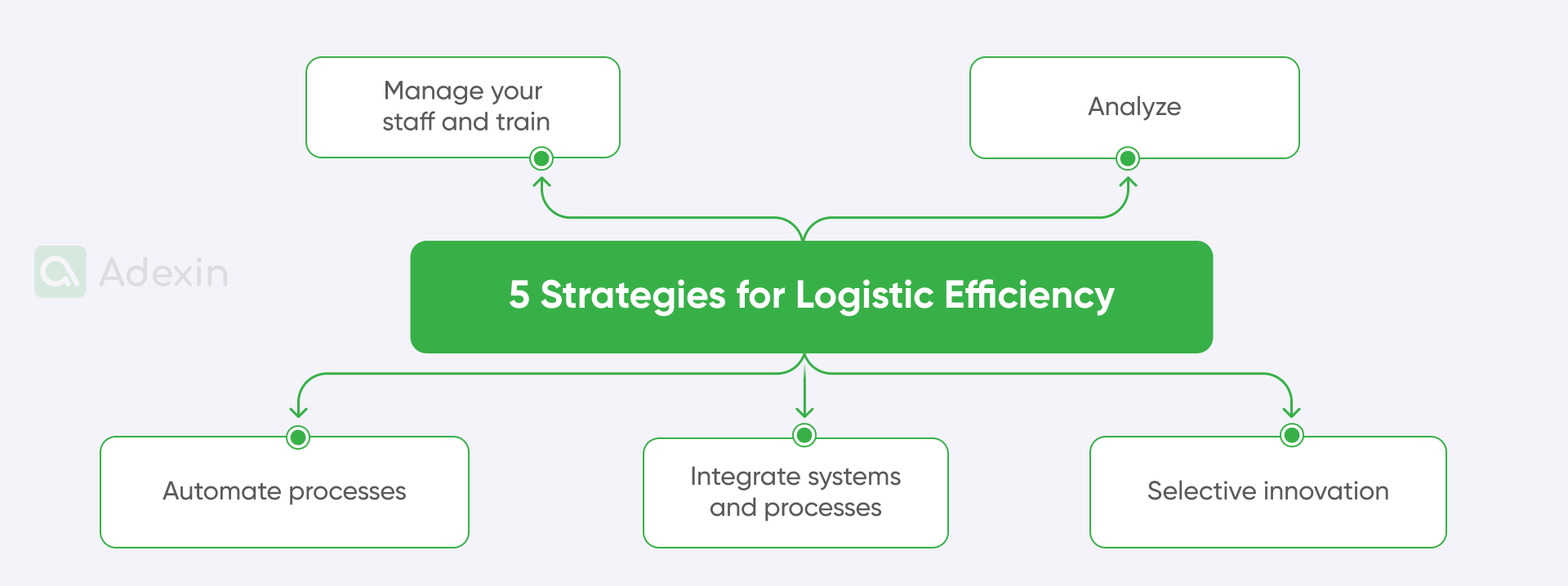
1. Manage your staff and train for better logistics efficiency
While working in logistics in the Netherlands, I first recall that the problems didn't come from processes but from the people. Personnel who are likely less motivated in logistics are those at the lowest level, and what is really ridiculous in this situation is that they are likely the most important.
If you don't have automation in the warehouse, your warehouse clerks must transport pallets from dock to stock. If they don't show up at work, your business is exposed to some dropdown in performance or even serious revenue losses. So, your business really depends on the warehouse clerk.
The issue is that most logistics companies don't pay their warehouse clerks well enough. So, there must be other ways to keep them motivated to increase logistics efficiency. One of the things that increases their motivation is paying attention to their performance, providing frequent training, and giving them responsibilities, which means ownership of processes. These are the management drivers, and when personnel are strictly responsible for certain actions, their motivation will increase.
Most companies don't see this and underestimate the value of warehouse clerks. This often boils down, in my observations, to a lack of motivation and even the absence of employees, which leads to firing them afterward. Is that a good approach? Is it better to replace the employee, give him more attention, and invest in him? Answers to these hard questions depend on your business situation, but we highly recommend putting people first.
2. Automate processes for higher logistics efficiency
Today, logistics is constantly evolving with trends such as digital transformation and warehouse automation. Modern businesses advise on how to shift their business to increase efficiency in logistics. However, the truth is that most businesses still heavily rely on traditional solutions known from the past, such as paperwork and a large amount of manual tasks. Logistics operations like receiving, away, and order picking often involve manual handling of paperwork and other manual tasks.
You can automate and transform your logistics by deploying autonomous vehicles and robotic pallet stacking systems, but we highly recommend focusing on areas that can bring fast benefits with minimal input. One such area is transforming how your business handles administration. So, first but not least, if you heavily rely on MS Excel spreadsheets, consider automating processes and managing document workflows to transition your business into a more digital environment. We can honestly say that if you rely heavily on paperwork, you won't be able to effectively transition to automation based on autonomous vehicles, robotics, etc.
Many of our customers have asked right from the start what they can do to remain more innovative. We say make a digital proof of delivery (POD) and implement a document management system for logistics. This is the first step and a great strategy to help grow your logistics efficiency.
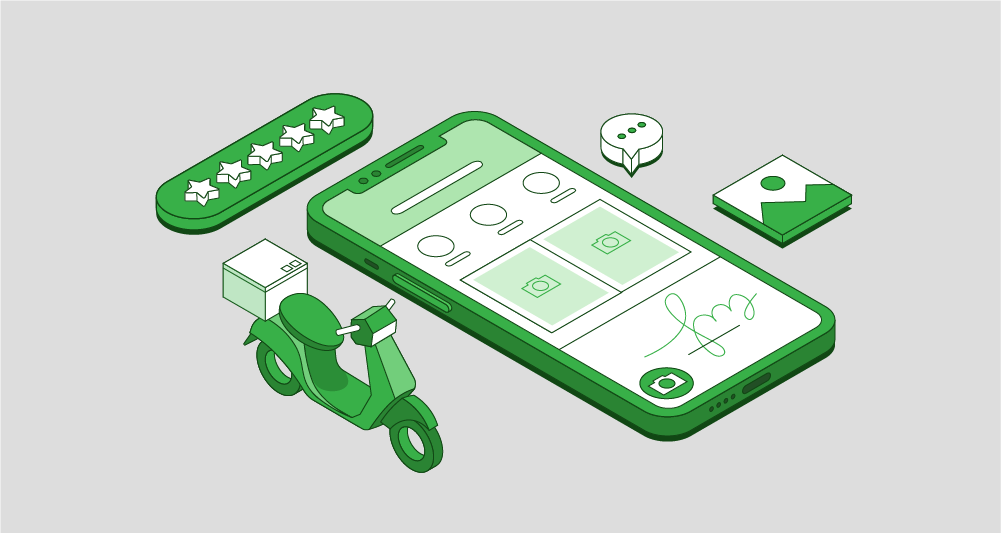
3. Integrate systems and processes for logistics efficiency
We have found through decades of working with logistics businesses that they have many systems in place that are not integrated. These systems are responsible for major processes within the company. For example, here are the systems that are often not integrated in logistics:
Warehouse Management Systems (WMS): These are the most commonly used software for optimizing warehouse operations, such as inventory tracking and order fulfillment.
Transportation Management Systems (TMS): TMS provides full alignment and tools for planning, executing, and optimizing transportation operations.
Financial Systems: To manage financial transactions, budgeting, and reporting, software for keeping payslips and invoices is necessary.
Enterprise Resource Planning (ERP) Systems: Software for managing core business processes such as order and inventory management.
Route Planning Software: This system allows you to optimize delivery routes to minimize costs and improve efficiency.
Loading Systems: This software automates the efficient loading and unloading of goods.
What about integration at this point, then? The software examples provided above are systems included in your parallel operations. However, these are often not integrated, requiring people to log in to different systems, download data from various sources, etc.
From one perspective, this setup is a good solution for security concerns. However, on the other hand, it generates a significant amount of manual work for your personnel and system issues when some faults occur.
To solve this, you can create a custom software platform with an automated single sign-on solution for users. This platform can act as a layer with a single interface for managing all logistics systems connected through APIs. This brilliant strategy doesn't require you to replace various systems but rather connects them to your custom and dedicated solution.
Need help with enterprise resource planning systems development?
Learn how we can boost your business processes
Explore more4. Analyze
Analytics aren't anything new in today's business, and logistics is no exception. Analytics in logistics help facilitate better demand forecasting, which can lower warehouse volumes, and improve inventory management and shipping processes, among other benefits. Therefore, analyzing historical data in logistics has many facets.
Reflecting on my experience in logistics, I've found that KPI analytics were very beneficial to businesses in terms of continuous improvement processes. During my time in the supply chain, KPIs provided weekly insights into the most important indicators for our customers.
Metrics such as weekly shipping or seasonal shopping patterns, like those during Christmas, provided better projections for future operations. Thanks to analytics, we consistently improved, reducing expenses by avoiding constant mistakes.
Effective analysis requires good tools. To analyze logistics effectively, you need to integrate all data sources. Afterward, it's crucial to pivot the data and identify trends that emerge from comprehensive statistics. This traditional approach is often used in MS Excel spreadsheets. However, businesses today require more robust solutions that offer predictive analysis, which can be built with custom software to provide truly agile solutions.
Here are the benefits can get and how analytics impacts efficiency:
Performance improvement. For example: once you reduce errors made by humans.
Identifying waste of materials. For example: with better material handling and measured goods flow, etc.
Reducing costs. For example: lower transportation and warehousing costs once you reduce fuel costs.
Improving profit. For example: better calculated customer demand and timely delivery.
Catching fraud. For example: theft prevention through exact GPS tracking.
Time savings. For example: by using processes such as reverse logistics and returns management.
Transparency. For example: by giving stakeholders insight into historical data.
Competitive advantage. For example: by reducing manual and repetitive tasks.
Regulatory compliance. For example: with better document management and contracts management.
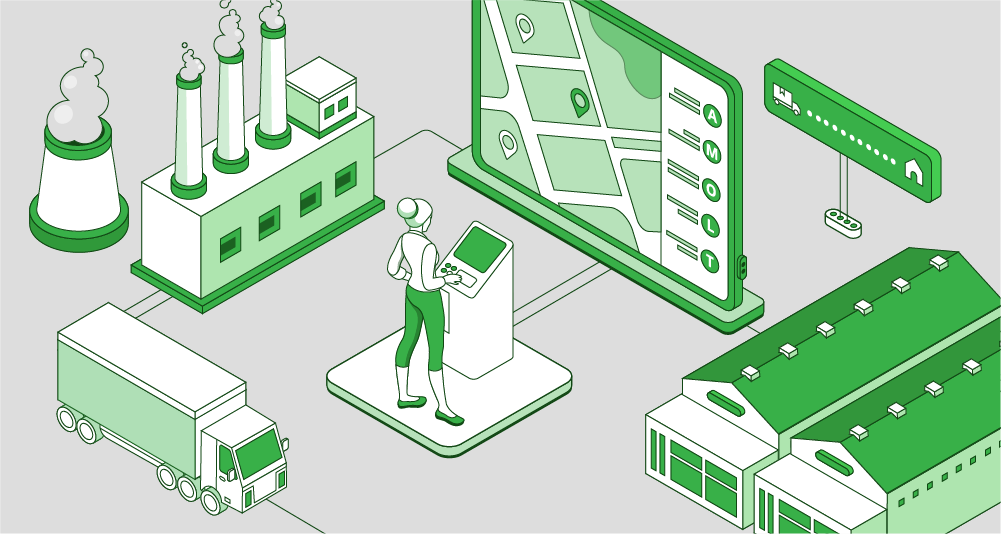
5. Selective innovation
This is our five-pronged strategy. If you're a small or medium-sized business, you must be selective with your spending. So, once again, don't feel compelled to adopt everything available. Consider the four strategies mentioned above. You may find them highly effective and cost-effective for your logistics efficiency. In essence, what we're emphasizing here is that selective innovation allows you to be more competitive when you precisely identify what your logistics require. That's an effective logistics strategy.
For instance, considering implementing a new warehouse management system (WMS) solution, consider what is truly valuable for your business. Do you need an off-the-shelf system or custom software? The range of options is broad, but purchasing an off-the-shelf WMS system in a SaaS model could mean paying for hundreds of features you may not need. Thus, a custom software solution might be wiser, allowing you to tailor it precisely to your business needs and maintain competitiveness.
Here we can share one of the most recent examples where we leveraged parking management. Our development was dedicated especially to the commercial market and was about a parking management system designed for the company that manages parking spaces.
We used an AI-powered engine that helps venue visitors better navigate. Despite its commercial usage, this highly dedicated solution for transit logistics significantly improves logistics movement between certain sectors in the parking lot. The application of such a solution can be easily applied to truck drivers who need to park at logistics centers while awaiting their time window for unloading or loading goods.
Adopting a selective innovation strategy ensures you get exactly what you need without falling behind your competitors. I've heard from many companies at trade fairs about the problems they face when they bite off more than they can chew. They thought they could adopt extensive systems that do a little of everything, but they ended up with systems full of errors that don't align with their business needs. One reason for this is that they aren't selective innovators.
Are you in search of a reliable tech partner?
Adexin can help with advanced logistics solutions
Contact usFinal takeaway
We wanted to give a glimpse of something you can benefit directly from. Don't overthink it, as nothing is too complicated. Despite the complexity of the logistics business, you can start small by implementing these strategies and grow faster. This is our proposal to help you improve your logistics efficiency.
Interested in learning more about obtaining agile logistics custom software that will help maintain effectiveness? Here we are. At Adexin, we eliminate bad ideas and focus sharply on robust solutions. Whether it's replacing MS Excel spreadsheets or developing more complex applications, we know how to achieve your goals efficiently and effectively in logistics. Get in touch with us today, and let's talk.