Managing logistics is unstoppable, tackling challenges and research potentials. Therefore, we are using data space from KPI measures. However, this is not the only source of knowledge to run successful logistics operations. These days, there is always custom software for logistics behind many successes, but what really makes companies really effective in logistics and supply chain management is always a combination of more complex elements. Let's take a closer look at the logistics management landscape and how to handle customer demand as a logistics and supply chain manager and other professional or supply chain logisticians.
What is logistics management? Core elements and processes
Logistics management combines all activities experienced operations managers need to handle in a warehouse to provide effective distribution and transportation means to the end customers. By looking into examples of logistics management, we understand that logistics management is defined by the elements divided between the selective sections of logistics and supply chain business. Here are the core elements that tell us what managing logistics is about and what kind of logistics management process it involves:
1. Inbound process in logistics and supply chain management
Inbound transportation is tightly connected to moving goods and materials from suppliers to a company's warehouse or production facility. So, this is a process defined in simpler words, such as “dock to stock,” that requires an effective management process. Whatever is delivered to the warehouse needs to be received, inspected, and stored within a warehouse or distribution center.
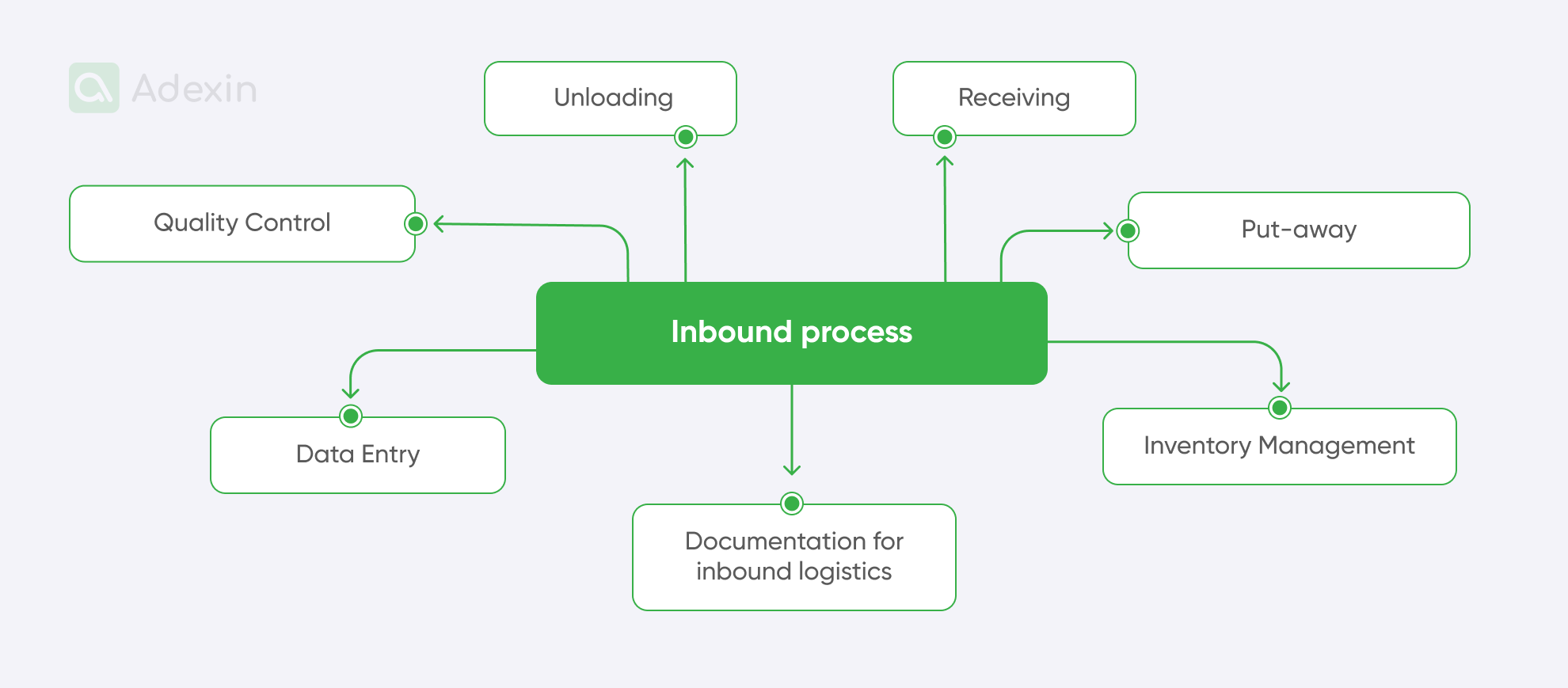
The first tier of the inbound process encompasses activities such as:
Unloading:
Unloading within inbound logistics covers this when goods arrive at the facility on trucks, trailers, or containers and are unloaded at the docs.
The receiving team places goods in special areas, whether the goods are designated to special storage areas such as returns, dangerous goods (DGR), or newbuild stock (depending on the industry-specific).
Receiving:
Goods are placed at the receiving stations if it is about efficient handling of small items or directly received from special areas to the warehouse.
Delivery is verified based on purchase order or other documentation.
Managed the quantity of goods based on inspected and received system-wise with barcode scanners.
Put-away:
The goods are moved from the receiving area to their designated storage locations.
Items are scanned again by the warehouse workers and entered into the inventory management system.
Storage locations are assigned based on product type, quantity, and warehouse layout. Need to scan locations to confirm the placement of pallets.
Quality control:
Along with the receiving process, incoming goods are inspected for defects, damages, discrepancies, and missing.
Other steps can also include segregating non-conforming items and processing them accordingly (returned, repaired, or disposed of).
Data entry:
Data entry with product information, including quantity, lot numbers, expiration dates, and serial numbers.
Purchase order information is updated straightforwardly to reflect the goods received.
Inventory management:
Goods are added to the inventory system. Here, the process includes checking stock levels to update them to reflect the new inventory.
Inventory locations are assigned and tracked within inventory systems to meet customer demand.
Documentation:
All relevant paperwork is processed and filed, such as invoices, packing slips, and some inspection reports regarding food production or other sensitive or high-risk, high-value goods.
This process includes careful document checking and might also include preparing some internal documentation. It is not always paperwork, as these days a lot of forms and documents are handled digitally. For example, a form that leaves comments for order pickers, etc.
Well, moving forward with this topic, it is important in logistics to determine what is reflected by effective inbound transportation. Internal transport, in that case, is crucial for maintaining a steady supply of materials for the production line in the manufacturing facilities, minimizing transportation costs, and ensuring timely production or distribution.
2. Outbound process in logistics and supply chain management
Outbound logistics operations include transport scheduling, with close attention to all the actions that are handled inside the warehouse. In that case, companies are integrating logistics management software that can connect warehouses with transportation. So, based on the WMS system, companies can gain insights into transportation from the TMS system. But outbound is mostly process handled in the warehouse, and it is about loading planning, dock planning, preparing goods for Shipping, if needed, then assembly on the VAS (Value-Added-Service area), packing, sealing pallets, Labeling, preparing shipping documentation, dock personnel planning, what we’ll explain more a bit later.
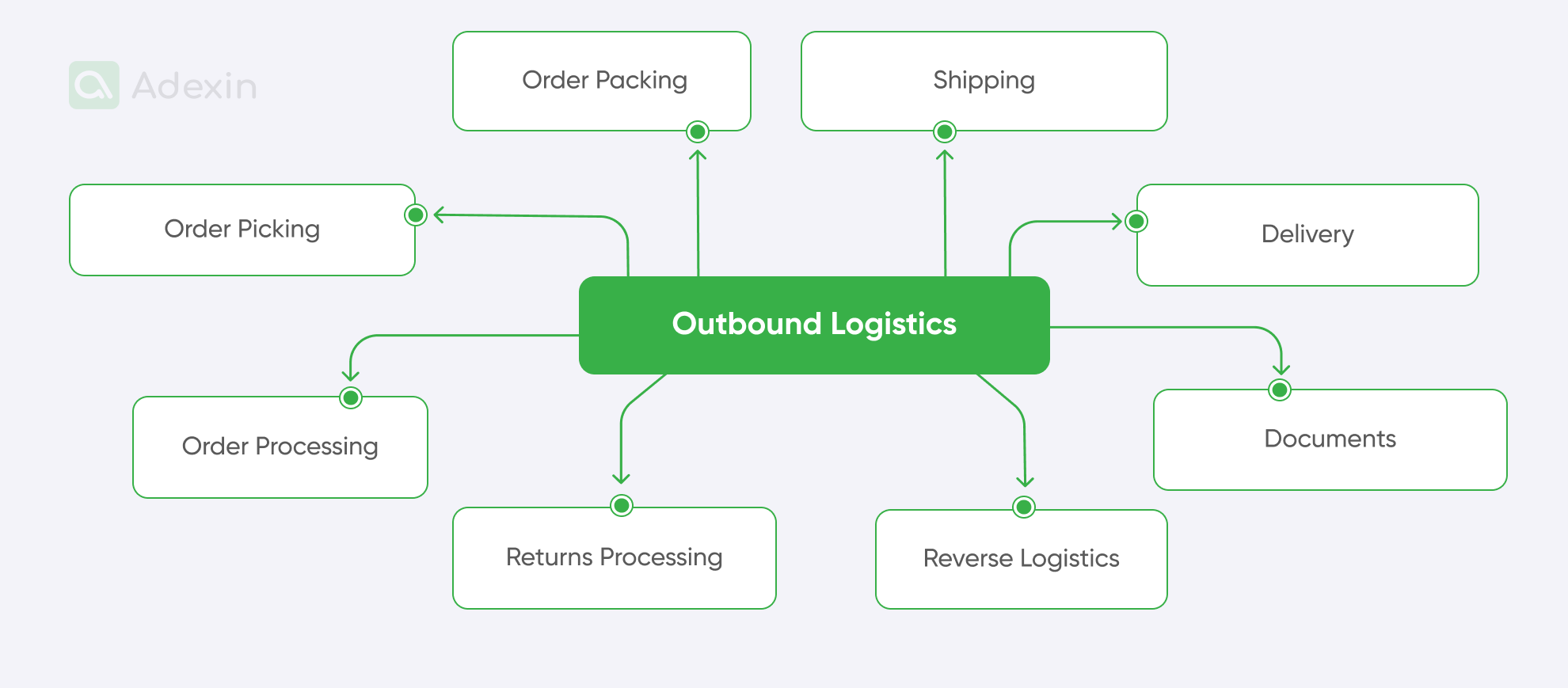
Summarizing the key stages of the outbound process, we see it as follows:
Order processing system:
Step one is about order receipt and verification.
Next, your team should action order entry into the system.
The system will most likely confirm the quantity after checking the inventory availability.
Software like the WMS system can manage order allocation and reservation.
Order picking:
Retrieving products from storage locations based on the order.
Accurate picking and quantity verification later on.
Order packing:
Packaging products securely for shipment.
Adding packing slips and other necessary documents.
Shipping:
Selecting the appropriate shipping carrier and method.
Generating shipping labels and documentation.
Loading products onto the carrier.
Supply chains delivery:
Transporting products to the customer's destination.
Handling delivery exceptions (e.g., address changes, delivery failures).
Documents:
Preparation of shipping and delivery documents. There are specialized platforms for this purpose for small and medium-sized companies. At Adexin, we have developed a DMS system for one of our customers. So, a shipping document management platform helps logistics manage their shipping documentation in a fully digital way and enhances positive customer experience.
Returns processing:
This process involves managing customer returns and issuing refunds or replacements. Therefore, logistics requires warehouse operations management and full system integrations.
Reverse logistics:
Reverse logistics refers to the process of moving goods from their final destination back to the manufacturer (reverse flow) or a designated facility for return, repair, recycling, refurbishment, or disposal. Unlike traditional logistics, which focuses on efficient forward movement.
3. Transportation planning in logistics and supply chain management
As explained above, transportation planning must be integrated with the warehouse to provide good dock scheduling for picking goods from, let’s say, the distribution center. But the planning of the transport goes far beyond that only collection schedule trucks, trailers, and containers. Good logistics management is also lined with entire journey planning, where route planning, fuel usage estimation, and truck driver planning allow for reduced costs and prevent delivery delays.

Top-notch transportation planning involves a complex interplay of various factors, including:
Demand analysis. Understanding the current and future transportation needs of a region.
Network planning. Designing efficient transportation networks, including roads, railways, public transit, and airports.
Mode choice analysis. Evaluating the logistics efficiency of different transportation modes for specific needs.
Infrastructure development. Planning and implementing transportation infrastructure projects.
Policy development. Creating regulations and policies to support transportation goals.
Environmental impact assessment. Evaluating the environmental consequences of transportation projects.
4. Intralogistics functions in logistics and supply chain management
Intralogistics is undoubtedly the part of logistics management that helps control and optimize the flow of goods and mobile equipment in a warehouse, distribution center, or even manufacturing facility. It is also linked to managing internal transportation equipment such as EPT and forklifts to manage the storage process more effectively. Last but not least, it also related to the flow of goods between facilities, so if your warehouse and manufacturing plant are in two different locations, there should be a process in place, mostly based on supportive software that can help with First-in, First-out (FIFO), JIT (Just-in-Time) processes. All that is about improving production planning through chain management and fresh logistics network design.
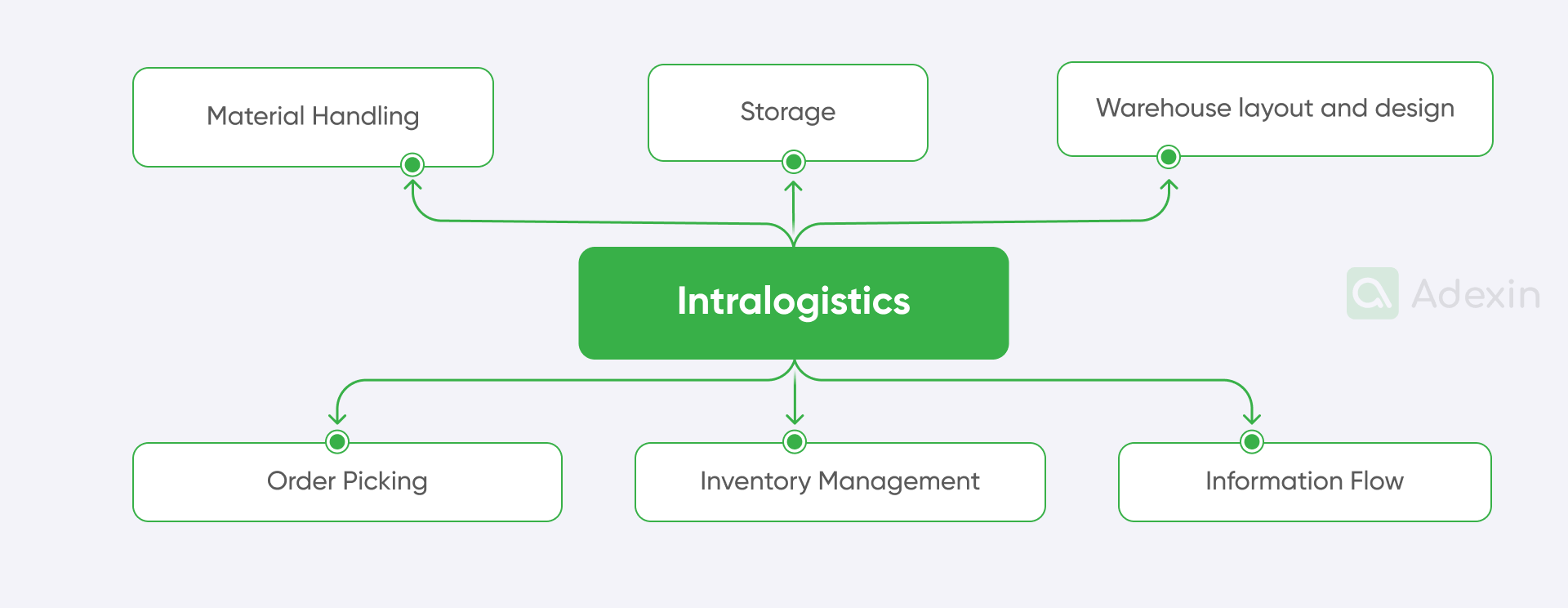
Let's look at the key components of intralogistics:
Material handling. Is the physical movement of materials within a facility, including equipment like conveyors, forklifts, and automated guided vehicles (AGVs).
Storage. Efficiently storing products in a way that maximizes space utilization and accessibility.
Order picking. Accurately and quickly selecting products to fulfill customer orders.
Inventory management. Tracking and controlling inventory levels to optimize and prevent stockouts. Storing goods and preventing aging stock, damages, poor handling, and missing stock items.
Information flow. Managing data flow related to products, orders, and inventory.
Warehouse layout and design. Optimizing the facility's physical layout to improve efficiency and productivity.
5. Material handling in logistics and supply chain management
Material handling encompasses the movement, storage, and control of materials and products throughout the supply chain. It involves various equipment and processes, from manual labor to automated systems. Effective material handling is crucial for optimizing warehouse operations, increasing efficiency, and cost savings.
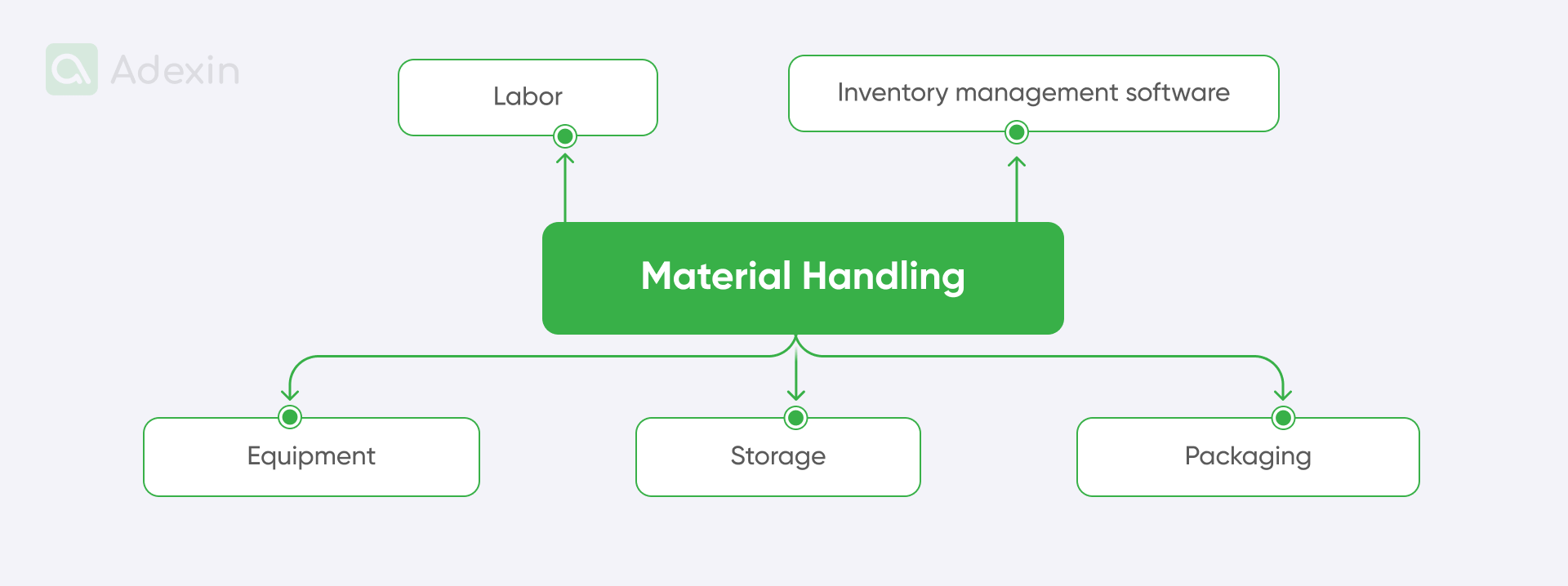
Let's look at the key components of material handling:
Equipment. Forklifts, conveyors, automated guided vehicles (AGVs), robots, and other machinery used to move materials.
Storage. Racks, shelves, bins, and other storage solutions for organizing and protecting products.
Packaging. The process of preparing products for transportation and storage.
Labor. The human workforce is involved in material handling tasks.
Inventory management software. keep all data digitized and easy to access.
6. Financial planning in logistics and supply chain management
Financial planning involves managing financial resources to achieve specific goals. It includes budgeting, forecasting, financial analysis, and investment planning. Effective financial planning is crucial for the long-term success of any organization.
Key aspects of financial planning:
Budgeting. Creating a detailed plan for income and expenses.
Forecasting. Predicting future financial performance.
Financial analysis. Evaluating financial performance and identifying areas for improvement.
Investment planning. Allocating funds for growth and expansion.
Risk management. Identifying and mitigating financial risks.
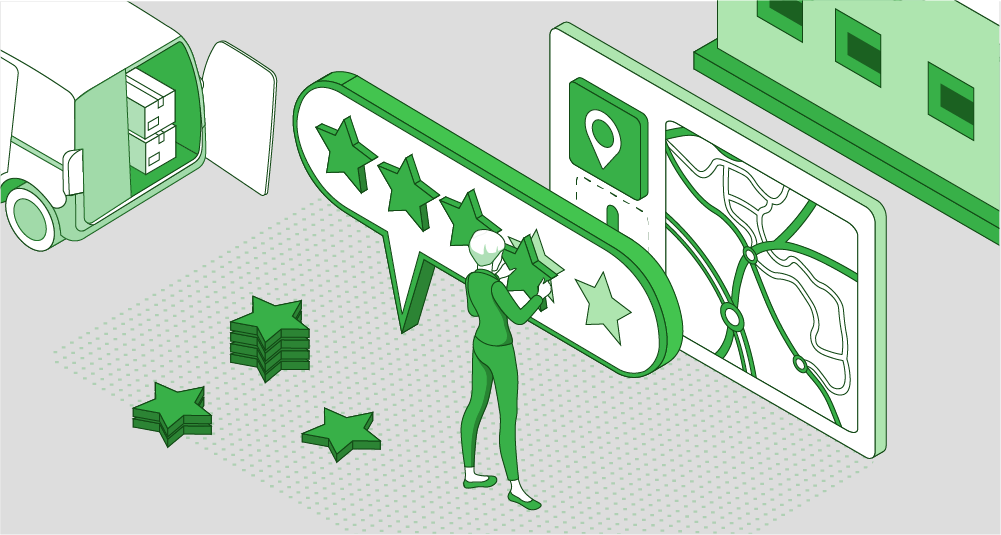
7. Personnel in logistics and supply chain management
Personnel management, also known as human resource management, focuses on effectively managing employees within an organization. It involves recruitment, hiring, training, performance evaluation, and employee relations. Effective personnel management is essential for creating a positive work environment, improving employee satisfaction, and achieving organizational goals.
Key areas of personnel management:
Recruitment and selection. Finding and hiring qualified employees.
Training and development. Enhancing employee skills and knowledge.
Performance management. Setting goals, providing feedback, and evaluating employee performance.
Compensation and benefits. Determining employee pay and benefits packages.
Employee relations. Building positive relationships with employees.
8. Warehouse management in logistics and supply chain
Warehouse management involves the efficient planning, control, and execution of warehouse operations. It encompasses various aspects, including infrastructure, storage systems, and layout. Effective warehouse management is crucial for optimizing space utilization, improving order fulfillment, and reducing costs.
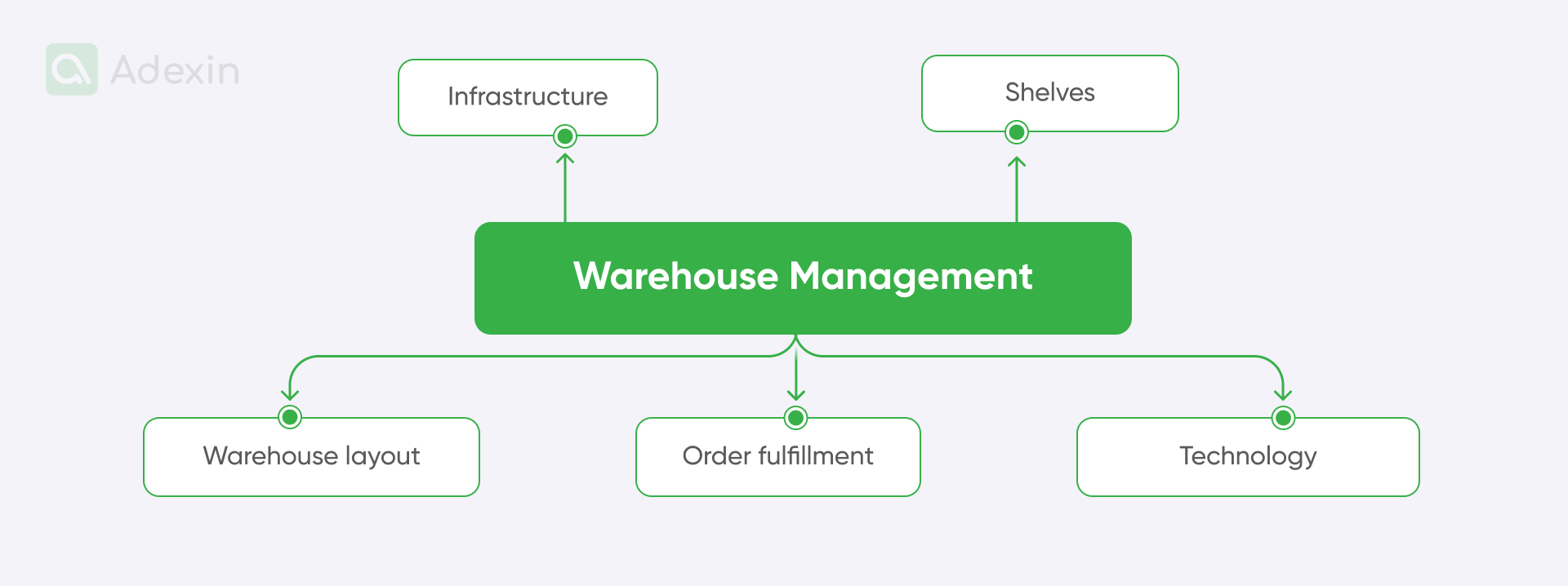
Key components of warehouse management:
Infrastructure. The physical structure of the warehouse, including the building, floors, walls, and roof.
Shelves. Storage systems are used to organize and store inventory.
Warehouse layout. The arrangement of storage areas, aisles, and equipment within the warehouse.
Order fulfillment. Processing and shipping customer orders efficiently.
Technologies. Utilizing warehouse management systems (WMS) and other technologies to optimize operations.
Need help with warehouse management system development?
Learn how we can boost your logistics processes
Explore more9. Customer service in logistics and supply chain management
Customer service is the backbone of successful logistics operations. It involves effectively managing customer interactions, meeting customer needs, and building strong relationships. In logistics, customer service extends beyond mere delivery; it encompasses proactive communication, problem-solving, and exceeding customer expectations.
The importance of customer service in logistics:
Customer satisfaction. Meeting customers’ requirements is paramount in the competitive logistics industry.
Building trust. Strong customer relationships built on trust and reliability are essential for long-term business success.
Competitive advantage. Exceptional customer service can differentiate a logistics provider from competitors and maintain customer loyalty.
Problem resolution. Effective customer service involves quickly and efficiently resolving issues that may arise during transportation.
Feedback mechanism. Customer interactions provide valuable insights for improving logistics operations and covering customer requirements.
All those elements implicate diverse operations that require a careful logistics management approach at every stage. For example, you need a Freight Transport Logistics Action Plan once you handle transportation planning in logistics. Statistical coverage and economic analysis of the EU logistics sector have shown that each company needs to take precise cost composition and profit margins into account due to low-margin revenue from transportation. So, if you own a warehouse and truck fleet, you need to be aware that, most likely, your main source of income is storage, not delivery. The immense difference in labor costs mainly causes this trend.
Other examples from statistics have shown that transport means are more profitable in better-developed countries. Let’s say that European countries vary in costs per tonnage, e.g., ranging from about 5 EUR in Bulgaria (less expensive) to nearly 19 EUR in Denmark and Sweden for road transport in 2006. This explains why companies that own fleets of trucks prefer to register their fleet in countries like Romania and run their warehouses in the Netherlands while hiring staff from less developed EU countries for lower wages. An example of such a business is the e-commerce company VidaXL from The Netherlands, which registers its fleet of trucks in Romania while maintaining its capital in the Netherlands with a core distribution center in this beautiful Dutch land.

Logistics management meaning and its efficiency
The meaning behind logistics management is to improve efficiency. Through this term, logistics optimization elements should be translated and delivered through data analysis. Here are the key elements of focus that help management optimize logistics:
Insights into infrastructure
This is related to trade and transportation, so frankly, it's about the layout of warehouses and resource management, which in this context can be described as truck fleet management.
On-time delivery
Shipments are at the scheduled delivery time, so it is an outbound process.
International shipments
International trade transactions where customs regulations must be taken into account. Customs processes and paperwork should be made more efficient.
Traceability and tracking
Real-time location of shipments and their traceability throughout the logistics chain. At this stage, it is necessary to analyze delivery time performance against estimated delivery time (ETA), etc. Here, you get insight into on-time delivery rates, transit times, and service failures.
On-time shipping
This kind of data concerns shipment departure date and time. So, you can validate when the shipment left the warehouse. This measurement can also reveal scheduled delivery dates and times, giving you accurate carrier performance data. It is a critical performance indicator (KPI) in the logistics industry. It measures impacts on customer satisfaction, revenue, and overall business reputation.
Incorrect quantity shipped
This value shows whether the order quantity was matched within a certain time frame. For example, the customer's order could vary from the actual order handled in the warehouse. This boils down to the wrong shipped quantity. So, the actual number of items shipped may be too high or too low, which generates extra costs afterward.
Documentation errors
This process can be handled digitally with a document management system (DMS) to provide order information, such as order number, customer details, shipping address, and product information. However, without proper training, your staff can still make errors, often with manual data input. This results in incorrect shipping documents with wrong quantities (QTY) and SKUs on packing slips, invoices, bills of lading, and customs documentation. Common error types include incorrect addresses, missing information, and discrepancies in quantities or product descriptions. These are mostly filled in manually and prone to typos.
Need help with document management systems development?
Learn how we can boost your business processes
Explore moreInventory discrepancies
By tracking product SKUs and unique product identifiers, you gain insights into inventory levels using recorded quantities in the inventory system. Physical inventory counts, such as cycle counts of actual quantities of products on hand, manage this process. Issues might arise later on with order history, which involves information about incoming and outgoing shipments. Any issues can be presented in discrepancy reports, where you can validate detailed records of inventory differences and mistakes made in the warehouse.
Why is it important? For example, according to Inventory Inaccuracy in Retailing: Does it Matter?, the survey results showed that about 60% of the SKUs analyzed are affected by inaccuracies in warehouse inventory records. Correcting such inaccuracies leads to a 4% to 8% increase in sales at participating retailers. So, no matter how accurate your inventory records are, this report shows that there is much to be gained if you strive for further accuracy.
Damaged goods
Here, the focus is again on shipment details, where the order number, shipping carrier, and delivery date are crucial. Frankly, damage to items is a natural part of this business and cannot be completely avoided, so it is crucial to keep an issue description that can help track the nature and extent of the damage to the product. Some warehouse management systems allow you to capture images of damaged goods for direct visual documentation. It helps make customer claims in B2B and share information with customers to help handle complaints and claims for high-value, high-risk goods.
Well, according to Industrial Engineering Advance Research & Application, very often, damage can be caused by the poor design of the warehouse shelving. So, logistics companies can also run reports on damaged-good warehouses, where all affected goods can be stored with easy access. This is because all the items should be scrapped or dedicated to the spare parts dismantle process to be reused for purposes other than direct sales.
Overall tracking metric
As mentioned above, there are tracking precautions for shipped goods you must take with carriers. Internally, however, there are several other metrics that you can track, such as barcode scanning, RFID, and near-field communication (NFC) systems. It could include, for example, the volume of goods moved internally in the warehouse or metrics that can help assess the ease of use of internal equipment for transportation (such as the working hours of forklifts and ETPs).
You can use these systems to measure these more precisely:
Transportation management systems (TMS). Software for managing transportation operations and collecting data.
Warehouse management systems (WMS). Software tracking inventory and order fulfillment.
Customer relationship management (CRM) systems. Storing customer data and interactions.
The above are good examples of the data that you can manage to capture the most inefficient parts of the business. By looking into these numbers, you can make more accurate decisions and improve overall performance.

KPIs as logistics management important component
We will give an example of transportation efficiency in automotive supply chain management, where the KPI metrics indicate that not all performance aspects are being properly handled. Let’s examine some issues based on KPIs and how corrective actions can be implemented based on the measured performance metrics:
Accurate and timely documentation 90%. This metric indicates that the company has noticed a drop in administrative performance. It was calculated based on 22 shipments dedicated to end customers with spare parts for the car assembly, where the documents for 2 shipments contained errors. This caused delays in issuing documents, and these documents required amendments. By analyzing this metric, we need to assess the root cause, which could be improperly trained personnel or a lack of software that can run auto-checks for manually filled shipping details.
Proper packaging 70%. The KPI metrics show that 15 shipments had packing issues. These issues could involve packing methods and staging problems, such as pallets being too high or incorrectly stacked before loading onto the truck. Out of 22 shipments, 7 had packing issues, causing delays. The root cause could be poor packing instructions for the outbound team. They might not know the required pallet height for air cargo shipping.
Correct labeling 95%. During the same month, one error with shipping labels was made out of the 22 shipments. The 5% drop could be caused by incorrect shipping labels, where the outbound team swapped labels for different pallets. A small issue like this could cause delays and incorrect delivery destinations. The root cause could be multiple pallets near the dock, indicating mixed pallets for several destinations and customers near the loading dock.
So, by looking into metrics, here are the corrective actions that can be taken to manage logistics more properly:
Accurate and timely documentation (90%)
Issue: Errors in shipping documentation lead to delays and amendments. The potential root causes are insufficient training, inadequate software, or process inefficiencies.
Managers can consider corrective actions:
Implement mandatory documentation training for all relevant staff.
Invest in or upgrade document management software with automated checks.
Develop clear and standardized documentation templates.
Implement document management software that can run document checks automatically.
Establish regular audits of documentation accuracy.
Proper packaging (70%)
Issue: Packaging issues lead to damage and delays. Potential root causes include a lack of standardized packaging guidelines, improper training, or inadequate packaging materials.
Logistics management should consider corrective actions:
Develop detailed packaging guidelines for different product types.
Provide comprehensive packaging training for all staff involved.
Implement a WMS system with guidelines for packing methods (with automatically calculated pallet layouts, etc.).
Ensure an adequate supply of appropriate packaging materials.
Implement regular packaging audits and inspections.
Correct labeling (95%)
Issue: Incorrect shipping labels lead to delivery errors. To prevent the error from happening again, it is crucial to find the potential root causes. That might simply be human error, inadequate labeling systems, or poor workspace organization.
Effective logistics management should point out corrective actions, such as:
Implement a double-checking system for shipping labels.
Utilize barcode or RFID technology for label generation and verification.
Improve workspace organization to prevent label mix-ups.
Deploying software to generate shipping labels automatically with clear shipping details.
Provide regular training on label accuracy and outline shipment importance to put more attention on high-value, high-risk shipments.
Are you in search of a reliable tech partner?
Adexin can help with advanced logistics solutions
Contact usConclusion on logistics activities and management
Effective logistics and supply chain management is the foundation of successful logistics operations. You can gain a competitive advantage in today's fast-changing market by optimizing the flow of goods, reducing costs, and increasing customer satisfaction. However, all the results can be more effective and turn into a more visible return on investment if you get custom software that combines everything we've said in this article.
Mastering logistics, from inbound and outbound processes to transportation planning and inventory management, is critical to driving growth and profitability. Consider upgrading your logistics skills. Check our blog for detailed information and practical strategies, or contact us for expert advice. Let's optimize your logistics together!