Inventory management software for warehouses facilitates how businesses can manage their stock most efficiently. Good stock management allows you to optimize efficiency in your distribution center and cope better with demanding processes such as last-mile delivery or just-in-time delivery (JIT).
Inventory management involves defining operational requirements that align with the best warehouse management software at the facility level and the type of stock. Whether it is the food industry, e-commerce, or heavy industry with dangerous goods stock, this includes rules for inbound, outbound, and warehouse operations, along with analytics capabilities in one system.
To manage inventory most efficiently, you need the best warehouse inventory management software. In this article, we explain what is required from your inventory management software and what warehouse and logistics software development entails for SMEs, as well as the implementation considerations. See our guidelines and enjoy this insightful knowledge with first-hand experience from the logistics industry.
What are the elements of inventory management software?
Inventory management is very often a component of warehouse management systems (WMS), which include both software solutions and a set of processes. However, it can also function as a separate entity. Companies often benefit from more agile inventory warehouse management system solutions based on custom development, which can integrate with other departments in the organization. Deloitte, for example, believes that one crucial factor that can make or break a customer’s shopping experience is inventory visibility.
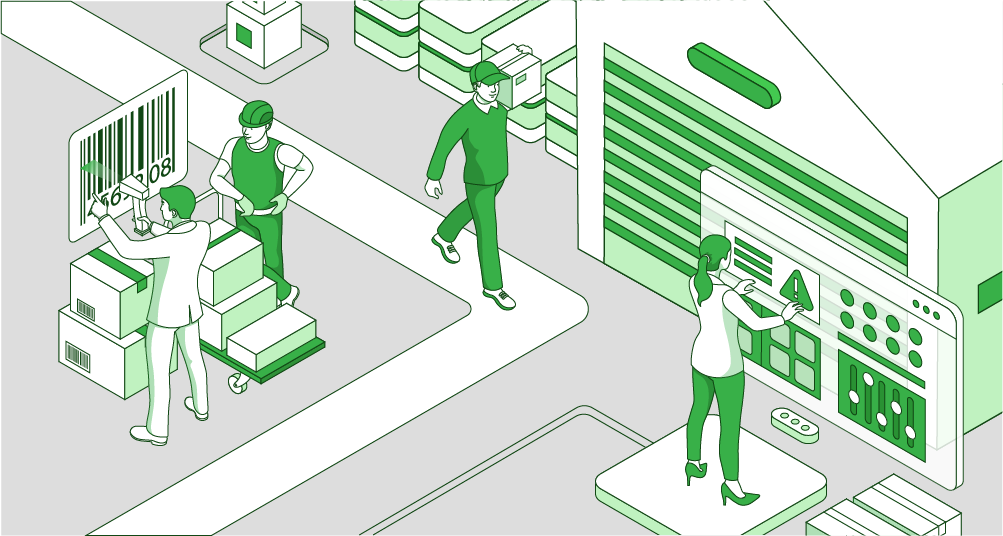
Inventory management has a broad operational area and it covers three main elements:
Inbound
The moment that is measured is when goods arrive at the warehouse. It is the time when trucks deliver goods with trailers or containers, and they are ready to be unloaded at the warehouse docks. Inbound includes operations required for a warehouse management system, such as:
Receiving. Checking and receiving incoming goods.
Unloading. Removing goods from transport vehicles.
Inspection. Verifying the condition and accuracy of goods received.
Sorting. Categorizing goods for proper storage.
Putting away. Transporting items to designated storage areas.
Labeling. Marking goods for identification and tracking.
Returns processing. Handling returned goods and processing them appropriately.
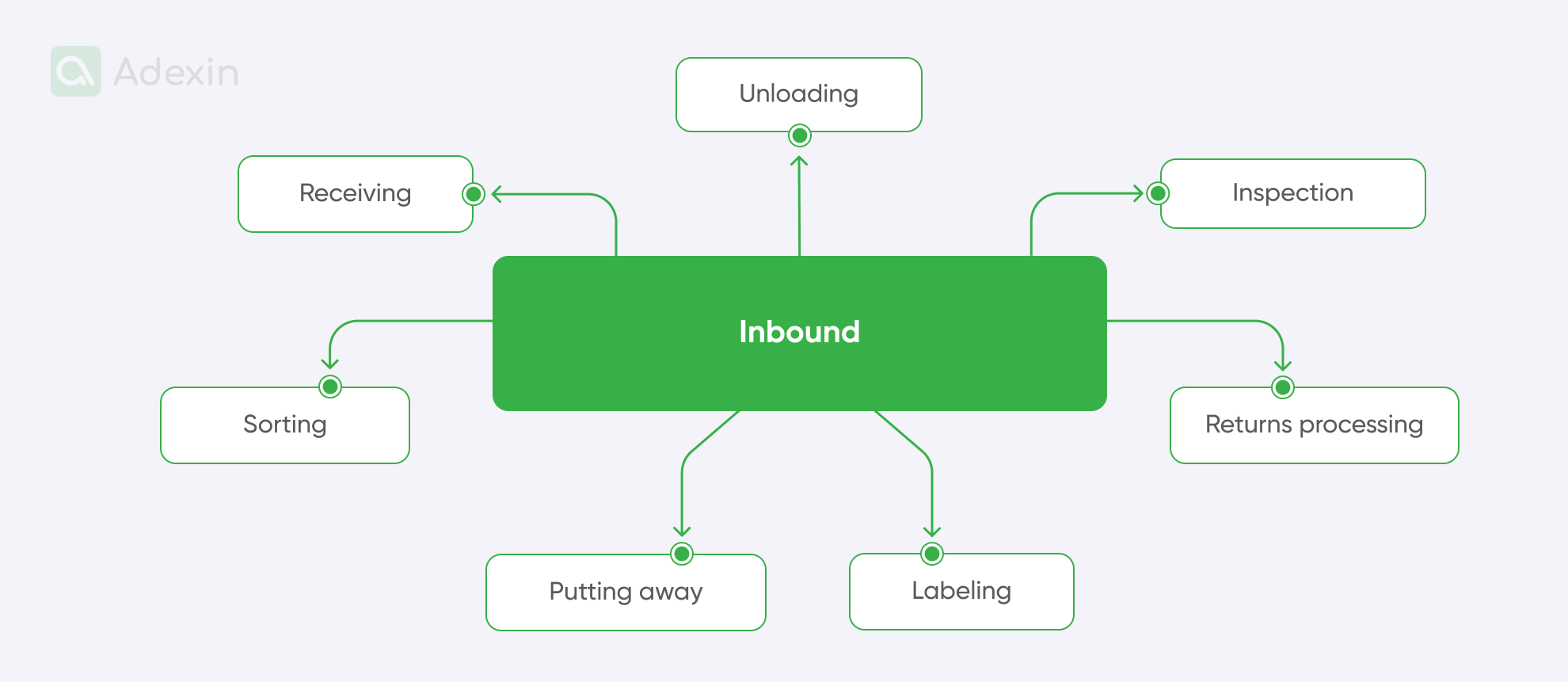
Outbound
When the order management system receives orders, these are provided to the inventory management system. The next step is the invoicing process related to preparing for shipping and shipping itself. Here are the steps to ensure that outgoing inventory is accurately and efficiently processed and shipped to customers:
Order picking. Selecting products from inventory to fulfill customer orders.
Packing. Securely packing selected products for shipment.
Labeling. Applying shipping labels and necessary documentation to packages.
Staging. Organizing packed orders in designated areas for final inspection and loading.
Loading. Placing packed orders on transport vehicles.
Shipping. Dispatching loaded cars to destinations.
Documentation. Preparing and managing required shipping documents and records.
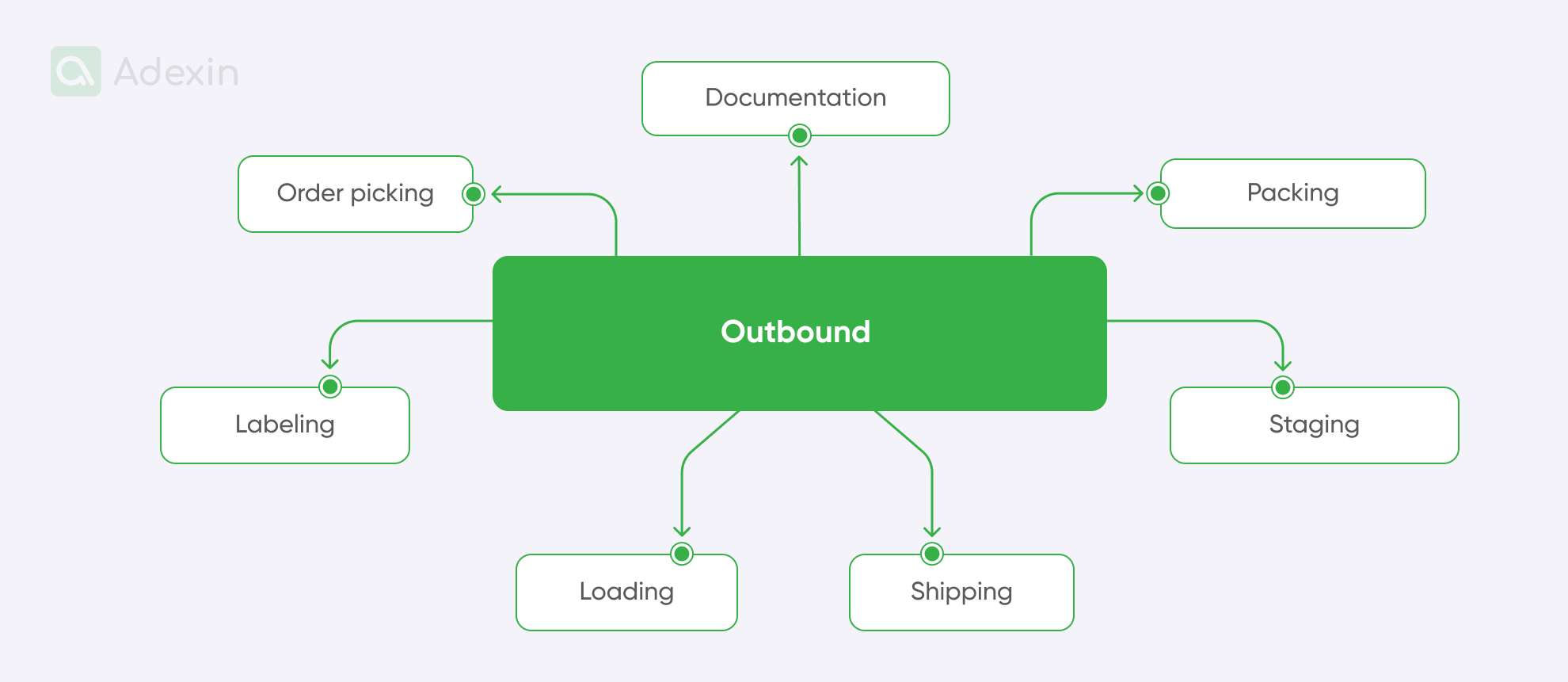
Inventory warehouse operations
We can say that inbound and outbound are also basically operations on the inventory management software, but these two terms solely cover what comes in and what goes out from the warehouse. But having in mind all other internal operations on the inventory, we can mention:
Inventory counting. Regular counting of inventory, including cycle counts and annual physical inventories, to ensure accuracy.
Replenishment. Replenishing inventory from the warehouse to picking areas to meet demand.
Inventory rotation. Implementing methods such as FIFO (first in, first out) or LIFO (last in, first out) to manage product shelf life and reduce waste.
Slotting. Strategically placing inventory in optimal locations in the warehouse for efficient picking and storage.
Quality control. Checking inventory for damage, defects, or discrepancies to maintain quality standards.
Returns processing. Handling returned goods, including checking, restocking, or disposing of items as needed.
Inventory tracking. Using software and technology (such as barcodes and RFID) to monitor inventory levels, locations, and movements in real-time.
Data analysis. Analyze inventory data to forecast demand, identify trends, and make informed decisions about inventory levels and orders.
Security and compliance. Ensure all inventory handling processes comply with safety regulations and industry standards.
Combining all the elements from receiving to put away or outbound operations like pick, pack, load, or shipping creates a scheme of repeatable processes daily in warehouses and distribution centers.
Warehouse management system for inventory and storage
What poses one of the challenges in inventory management is the storage capabilities that should comply with inventory warehouse management software features. It means that if you store various sorts of goods in your warehouse, your system must sort out different stock for different locations. This is because items require different storage areas. It can sometimes be a fridge or area for a damaged location. It's not the only feature in the system's capabilities. Software should also recognize where to store on-the-shelf items and if they can be located in higher or lower locations. Plenty of small elements are essential to consider in inventory management software.
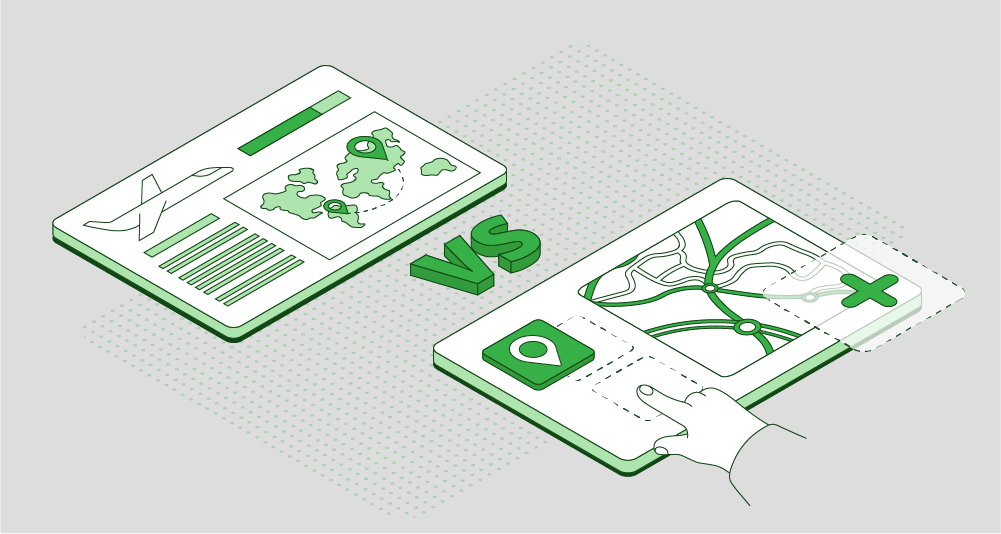
Storage requirements include:
Space allocation. Software algorithms should designate specific areas in a warehouse for different types of inventory based on their attributes, such as size, weight, and other characteristics.
Racking systems. Racks or pallet racks should seamlessly integrate within the software to optimize the use of space, streamline the picking process, and store products efficiently.
Temperature and climate control. Software functions should help monitor and control environmental conditions in the virtual warehouse, especially for products requiring controlled temperature or humidity.
Security measures. Software for inventory management should incorporate access control mechanisms, such as surveillance functions and inventory tracking technology. These embedded mechanisms should help prevent unauthorized access and theft.
Organization and labeling. Software should provide digital tools to clearly label storage areas for easy barcode scanning and implement an organized system. It is already the standard in the software to facilitate easy identification and retrieval of items.
Safety protocols. Inventory software should have integration capabilities with safety compliance checks and incorporate accident prevention features such as safety protocol reminders. The system should also prompt with recommendations for appropriate handling equipment.
Inventory accessibility. The software design interface should be easily accessible during picking and replenishment operations, taking into account factors such as customs clearance. This last one applies to store items in temporary locations until customs operations are handled.
Fire prevention. Inventory management should integrate fire protection simulation and alerts, along with recommendations for the use of fire-resistant materials. It is enforcing internal policies for handling flammable or hazardous materials (DGR goods).
Performance optimization. Software should allow for continuous data analysis and adjustment of digital storage layouts and processes to maximize efficiency and minimize unnecessary movement or handling of inventory. It is just about minimizing the number of transactions.
Scalability. One of the most important software elements is the one that accommodates future growth and changes. So, that means the software should be agile. It should consider product mix, enable seamless expansion, and optimize digital warehouse solutions.
Need help with warehouse management systems development?
Learn how we can help you
Explore moreStorage requirements can also highly depend on the sort of goods that are based on the warehouse management system. The most known kinds of storage include:
Bulk storage: large quantities of goods are stored without individual packaging, often in bins, on racks, or the floor.
Shelf storage: items stored on shelves for easy access and organization, suitable for smaller items or items of various sizes.
Pallet racking: storage of goods on pallets, usually stacked in rows and accessible by forklifts or pallet jacks.
Drawer storage: small items are stored in drawers or compartments in cabinets or racks, often used to store parts or components.
Storage: additional floor space built in a warehouse for storage, used when vertical space is limited.
Automated storage and retrieval systems (AS/RS): these high-tech systems automatically store and retrieve items using robots, conveyors, and computerized controls.
Temperature-controlled storage facilities: these are designed to maintain specific levels of temperature and humidity, suitable for perishable goods or sensitive materials.
Hazardous materials storage: specialized areas equipped with safety measures for the safe storage and handling of dangerous or flammable materials.
Outdoor storage: goods stored outdoors, often protected by canopies or fences, suitable for large or bulky items.
Cold storage: facilities designed to maintain low temperatures for the storage of perishable goods, such as frozen or refrigerated foods.
High-density storage: maximizing storage capacity through the use of compact racking systems or mobile storage units suitable for warehouses with limited space.
Flow racking: goods stored on sloping shelves with rollers or casters for easy movement and retrieval based on the principle of gravity.
Container storage: small items stored in bins or containers, often organized using shelving or container racks for easy access and inventory management.
This complexity varies much more when it comes to automated or smart warehouses. Here, software solutions require a different design approach. This is because an automated warehouse doesn't consider a human factor that needs to highly interfere with inventory. This impact has completely different advanced features, but of course, there are many other factors.
4 main stages to implementing inventory management software
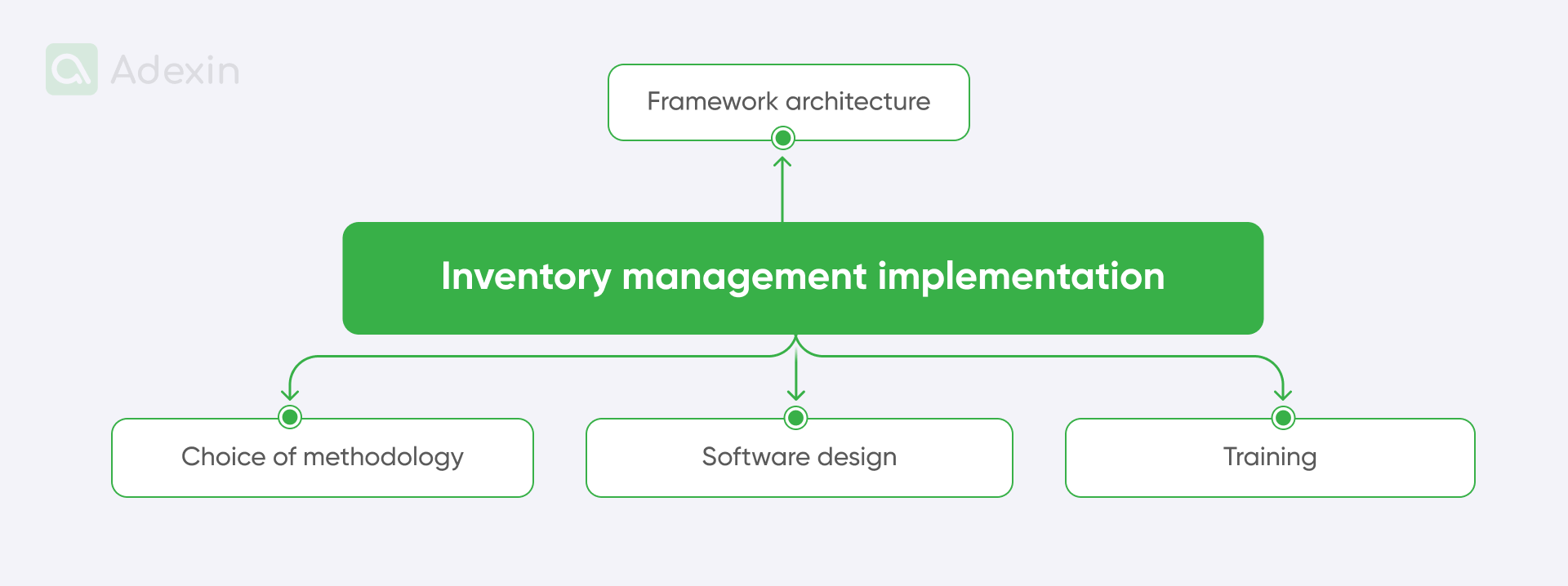
So, it's worth considering enabling your company with software that meets all storage requirements. Knowing your business, you can start by engaging your business in developing custom software. You can evaluate software partners and then implement a process that can include these 4 stages:
1. Choose a framework architecture for the best inventory management software
Analysis of the requirements. Understanding the specific requirements and challenges of the industry or business sector, e.g., food industry, high-tech, chemical industry, or e-commerce. Identify the functions and features required for effective inventory management.
Design. Create a framework architecture that outlines the software's overall structure, including the database schema, user-intuitive interface design, and integration points with other systems.
Selecting the technology stack. Choose the appropriate technologies and tools to build the software, considering factors such as programming languages, databases, frameworks, and third-party integration.
2. Choice of methodology for the right warehouse management system
Agile methodology. Choose an agile approach to software development, such as Scrum or Kanban, to allow for iterative development, frequent feedback cycles, and adaptive planning. It enables a flexible response to changing requirements and priorities throughout development.
Collaborative working. Encourage collaboration between cross-functional teams, including developers, designers, domain experts, and stakeholders, to ensure alignment with business goals and user requirements.
Continuous improvement. emphasize constant improvement and learning through regular retrospectives and feedback sessions that allow the team to identify areas for optimization and improvement.
3. Software design for better tracking inventory
Database design. Design a robust database schema to efficiently store and manage inventory data, including product information, inventory levels, transaction records, and sales orders.
User-friendly interface design. Create intuitive and user-friendly interfaces for different user roles, such as warehouse managers, inventory clerks, and administrators. Prioritize usability, accessibility, and responsiveness to improve the user experience.
Develop functionalities for improving the supply chain. Implement core inventory management functionality, such as inventory tracking, replenishment, order fulfillment, reporting, and analytics. Ensure seamless integration with other systems, such as ERP (Enterprise Resource Planning) or CRM (Customer Relationship Management) software.
4. Training for warehouse operation
User training. Inventory management solution onboarding includes comprehensive training and onboarding to familiarize users with the inventory management software's features and functions.
Technical training. Train IT staff and system administrators responsible for maintaining and supporting the software infrastructure.
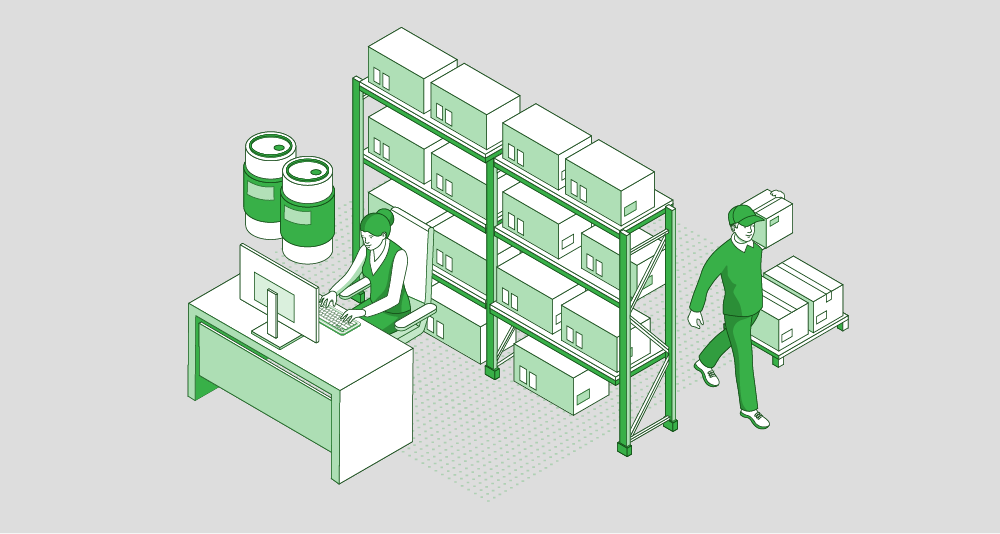
Warehouse management software for small business implementation
We call it small warehouse inventory management software because we consider that even small and medium-sized businesses can implement custom software for their warehouse and inventory management.
SMBs can design their own inventory warehouse management system at a low rate and benefit from much higher capabilities. The primary goal of the project, to develop an application that can store inventory information, maintain stock levels, and update inventory based on sales information, is to understand the business needs and requirements. Thus, the warehouse management system should comply with your industry. This means that each business, basically in each industry in which it operates, requires a different inventory management approach.
We, as developers of custom software for the logistics industry, already have experience in creating applications and solutions for warehouse management systems. We can optimize shipping, picking and packing, order and returns, integration, analytics, and many more.
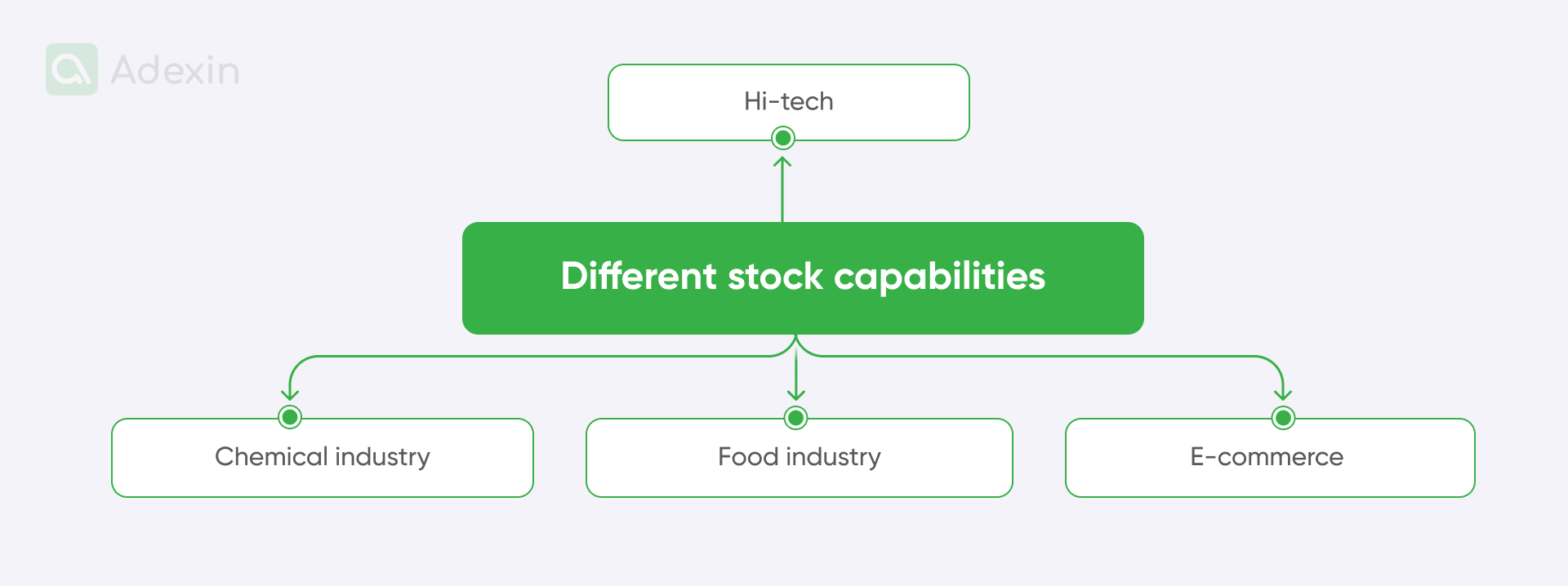
For example, we can mention four different industries that may require different stock capabilities:
Food industry
The food industry requires precise temperature control to maintain the freshness and safety of perishable products. Compliance with food safety regulations is critical to prevent contamination and ensure product integrity. It creates susceptible storage requirements.
Hi-tech
High-tech companies deal with sensitive electronic components and equipment that require meticulous handling and storage conditions. Climate-controlled environments are necessary to protect against temperature and humidity fluctuations that can damage delicate components.
In addition, when hard drives or processors are stored, it is often required to minimize electrostatic effects on elements that can damage items.
Chemical industry
The chemical industry handles hazardous substances, which requires strict compliance with safety regulations. To reduce the risks associated with chemical storage, warehouses must be equipped with adequate ventilation, security measures, and fire suppression systems. These are essential for warehouse management and keeping stock in good condition, for example in multiple warehouses.
E-commerce
E-commerce companies operate in a rapidly changing environment with fluctuating demand and diverse product offerings. E-commerce inventory management systems require scalability and flexibility to adapt to changing inventory levels and customer demands.
Are you in search of a reliable tech partner?
Adexin can help with advanced logistics solutions
Contact usFinal takeaway for WMS software
Effective inventory management is crucial for companies in various industries, be it the food industry, the high-tech sector, the chemical industry, or e-commerce. Companies can optimize their inventory management processes by implementing inventory management software solutions. It leads to greater efficiency and ensures compliance with industry regulations. Whether you are a small or medium-sized business, developing customized software provides the flexibility and scalability you need. You can more easily meet your unique warehouse requirements and business needs.
Take the first step towards modernizing your warehouse management and opening up new opportunities for success. Contact us today to learn how our customized inventory management software can streamline your operations, increase efficiency, and help your business grow.