Behind WMS, we see a Warehouse Management System dedicated to facilitating a new approach to stock management, order fulfillment, dock management, yard management, and mobility in the warehouse. Companies today cannot function properly without a WMS system that provides warehouse automation processes.
Looking at the main statistics, we see that from 2023 to 2024, the WMS market evolution has grown by more than 12%. This figure is measured in spending on WMS solutions, which ranges from 3.07 billion in 2023 to 3.52 billion in 2024. According to some sources, this is estimated at a compound annual growth rate (CAGR) of 14.7%.
We explain the definition of warehouse management systems here through firsthand experience in the supply chain industry. You can learn more about WMS software and what complements this solution regardless of the size of your warehouse and operations.
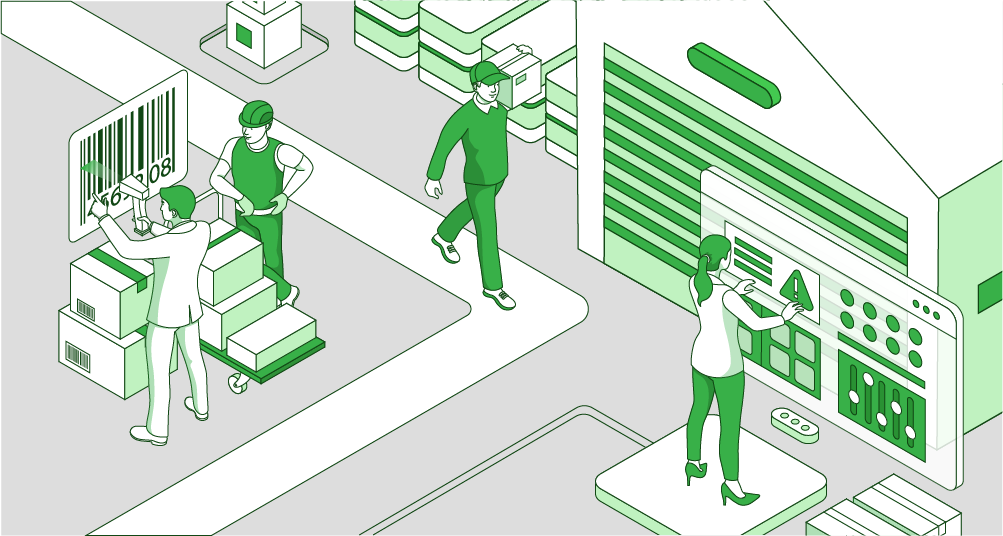
What is WMS?
The WMS definition is about implementing all the warehouse processes that are important for the Order Fulfillment Process. So, de facto, we need to outline everything connected to the WMS system, meaning to give you insights on what helps inbound, store, manage, and ship goods from the warehouse to the customers.
Of course, what the WMS development process will be like strictly depends on what kind of logistics business you are in. Your warehouse can deliver supply chain solution services in a contract logistics model. In this type of service, you should be able to adapt to customer demand requirements. It can be e-commerce, difficult-to-handle healthcare goods, Hi-Tech, or others. You can also provide other services based on your business profile. It doesn't change how WMS is working.
So, what is a warehouse management system for real? To better understand a WMS system, we should start by understanding the Order Fulfillment Process Steps. This process includes not only elements related to warehousing but also those needed for integrating supply chain management elements, such as order management, distribution, shipping, and some carrier management. Thus, we see fulfillment logistics complemented by supply chain solution capabilities.
Main order fulfillment process steps within the WMS system and beyond
Below, we outlined process steps in fulfillment logistics by adding where the WMS software complements this operation. These activities are very characteristic of eCommerce but can be adapted by companies that provide another service for warehousing and logistics processes.

Receiving inventory
Goods can come from various sources, including third parties, other departments, company warehouses, pipelines, or databases. Incoming inventory must be counted, checked, and recorded to ensure correct quantities and acceptable quality. SKUs or barcodes on products are used for receiving, storage, and subsequent retrieval.
Receiving inventory is the basic functionality of the warehouse management system. It is actually the very first touch point where goods are registered upon arrival in the warehouse. The WMS system helps with registering goods and labeling them with QR or barcodes.
Inventory storage
Upon receipt, goods are inventoried and issued immediately or sent to short- or long-term storage. Products are stored long enough to arrange orderly distribution for ongoing sales.
At this step, the WMS system helps locate inbound goods registered during the receiving inventory process on the shelves in the warehouse. For this process, the warehouse management system uses a mobile app that guides warehouse clerks to put away goods in dedicated storage locations. Whether it is a fridge for FMCG, perishable goods, or DGR goods, all that is supposed to be stored in dedicated locations that the WMS system helps navigate in warehouses. WMS supports also labor management.
Order processing
An order processing management system manages the picking and packing of products for each new customer order. In e-commerce, this system can be integrated with a shopping cart on a website to automatically start order processing.
A warehouse management system is often integrated with additional systems like a custom order management system that provides data on current orders. In e-commerce, it might be an online store integrated with WMS. The system helps manage orders and prepare picking lists for collecting them in the warehouse, check stock levels upfront, and choose the most suitable way to get them ready for shipping as soon as possible.
Need help with order management systems development?
We are happy to assist you
Explore morePicking
The picking team or automated robots select products from the warehouse according to the bill of lading, which includes product SKUs, product details, and locations.
Orders that reach the warehouse management system are distributed to warehouse clerks with picking lists on mobile devices. The WMS helps manage picking paths to shorten the order picking time. It can also automatically select locations from low shelves and navigate to dock locations, and yard management where goods are placed ready for shipping.
Packaging
Packaging materials are selected to achieve the lowest practical dimensional weight to optimize space on delivery trucks and reduce shipping costs. Packaging teams often include materials and labels for return shipping.
The packing process includes sealing pallets and labeling goods, sometimes palletizing if goods require lightweight pallets for air shipping or are too heavy to be shipped on wooden pallets. The warehouse management system also helps manage this process by finding an optimal way for stacking pallets. The level of assistance the warehouse management system provides depends on its advancement level.
Shipping
Orders are sent to the transportation channel for delivery. Carriers determine costs based on actual or dimensional weight, whichever is greater. Optimizing dimensional weight is critical to avoiding delays and additional costs.
Here is where the role of the warehouse management system is over, as this part includes carrier management. The only thing that a warehouse management system does here is integrated with relevant systems, such as the loading platform or TMS system, and provide information to these systems that shipping is ready to leave the warehouse and be loaded. So, this is where integrated warehouse management systems support your business capabilities.
Delivery
Shipping routes often involve multiple carriers. For example, FedEx may pick up a package for delivery by USPS. Hybrid methods are practical for reaching remote areas. Here, the warehouse management system no longer tracks the movement of goods as data on shipping is transferred to TMS systems (transportation management systems). Transportation management handles all the logistics, whether it is last-mile delivery or any other known shipping method.

Returns processing
Returns processing begins with attaching shipping materials and a return label to the original order. Returned products undergo quality checks and are refilled, returned to the vendor, or sent for recycling.
Here is where the WMS software comes back into play. Upon reaching the warehouse, returned goods are registered again by the warehouse management system with special labeling. Warehouse clerks need to control the goods to determine if they can be returned to the warehouse shelves or transferred to other locations for quality checks or dispute resolution.
Top 5 elements that define warehouse management systems
I think you are now able to define comprehensive warehouse management systems. However, what we've discussed so far has only reflected order fulfillment. Based on the following five elements, we'll take a more holistic look at the warehouse management system to show its relevance to various business areas.

1. Inventory management
The warehouse management system is all about inventory management, a huge part of order fulfillment. It handles tasks such as receiving, storing, and organizing inventory in the warehouse. Inventory management is the foundation of what a warehouse management system (WMS) is designed to do.
2. Order management
Order management plays a key role within a warehouse management system's broader functionality. The system facilitates the efficient processing of orders, from receipt to preparation for shipment. The WMS ensures that orders are accurately processed and delivered to customers on time.
3. Warehouse management metrics and analysis
Warehouse management systems also provide valuable metrics and analysis related to warehouse operations. These metrics help assess warehouse performance, such as inventory turnover rates, picking accuracy, and lead times. By analyzing these metrics, warehouse managers can identify areas for improvement and optimize warehouse processes.
Here are the most commonly known metrics used by warehouse management systems:
OTIF (On Time In Full). This is a common performance measure, but other metrics are equally important.
SD (Average Stock to Dock Time). Measures stock movement efficiency.
AODP (Average Order to Dispatch Process Time). Tracks order processing efficiency.
Audit to Dispatch Process. Monitors order processing steps for efficiency.
Warehouse Occupancy Levels. Manages space and inventory effectively.
Operational Prioritization. Enhances workload efficiency and identifies resource allocation needs.
Aging Stock. Tracks aging of stock to prevent obsolescence.
4. Mobility
Modern warehouse management systems often include mobile functionality, allowing warehouse employees to access the system from mobile devices or tablets. This mobility enables real-time updates on inventory movements, order statuses, and tasks, improving warehouse operations' overall efficiency and accuracy.
5. Supply chain integration
Warehouse management systems play a key role in integrating with other systems within the supply chain. This integration ensures seamless communication between stakeholders, suppliers, manufacturers, distributors, and transportation providers. By integrating with other systems, WMS software enables end-to-end visibility and optimization of the entire supply chain process.

We draw this conclusion based on our experience in the logistics industry and developing software solutions for companies active in the supply chain. We have demonstrated our commitment and knowledge of the industry by developing several useful solutions that have been able to solve several business problems. As an example, one of these is a mobile application for truck drivers, the purpose of which was to digitalize document flow in real-time. The solution significantly accelerated the processing of documents, while eliminating the loss of documents, improving the quality and the possibility of smooth processing by payment systems.
We know which warehouse management system features are important for your warehouse operations. Based on experience, we pay close attention to flexibility, as this agile approach can help you select only certain features. Whether your business is small or medium-sized, you may not need all of them. And we are always ready to make a custom-optimized solution that will directly solve your problems.
Where WMS system can be used?
WMS systems can be adapted through various specializations and are crucial for the supply chain. Here are several examples of WMS systems used in the supply chain:

Reverse logistics
Definition: The process of moving goods from their final destination back to the manufacturer or retailer for return, repair, recycling, or disposal.
Example: Electronic companies handle returns of defective products and recycle them.
Third-party logistics (3PL)
Definition: The use of third-party companies to outsource elements of a company's distribution and fulfillment services.
Example: A retail company using a logistics service provider to manage its warehouse and shipping operations.
Fourth-party logistics (4PL)
Definition: An integrator that brings together and manages the resources, capabilities, and technology of its organization and other service providers to design, build, and launch end-to-end supply chain solutions.
Example: A company using a 4PL provider to oversee the entire supply chain management elements, from sourcing to delivery.
Cold chain logistics
Definition: Transportation and storage of temperature-sensitive products such as food, pharmaceuticals, and chemicals.
Example: Transport of vaccines that require refrigeration from the manufacturer can be transported to healthcare facilities.
Military logistics
Definition: Military logistics involves the planning, coordination, and execution of the movement, maintenance, and supply of military forces
Example: When deploying troops, logistics includes coordinating the transportation of soldiers, vehicles, supplies, and equipment to the designated area of operations. This process must ensure they are maintained and supported throughout the military mission.
What are warehouse management system benefits?
A warehouse management system (WMS) offers a myriad of benefits that can significantly increase the productivity and efficiency of warehouse operations.

Here are some key advantages:
Optimized stock management. A WMS provides real-time visibility into inventory levels, locations, and movements, enabling better control over inventory levels. You can reduce excess inventory and minimize stockouts.
Increased efficiency. By automating various processes such as receiving, picking, packing, and shipping, WMS streamlines operations. Moreover, it reduces manual errors and improves overall efficiency.
Increased productivity. With features such as optimized picking routes, barcode scanning, and task assignment, WMS helps warehouse workers work more productively. This is leading to higher throughput and faster order fulfillment.
Greater accuracy. Barcode scanning and automated data capture minimize human error associated with manual data entry, leading to more accurate orders and happier customers.
Better space utilization. The WMS warehouse management system helps optimize warehouse layout and storage configurations, maximizing space utilization and enabling efficient storage of goods.
Challenges facing the warehouse management system
Once again, delving deeper into WMS system implementation cases, we've observed a fascinating trend. Businesses in logistics aren't simply seeking a WMS system or any other software. Supply chain, logistics, and transportation companies are searching for solutions to their problems.

Here are the main problems in the warehouse of most logistics companies:
Paperwork. Warehouse still relies heavily on paperwork, which can slow operations, increase errors, and hinder communication.
Lack of mobility. Limited mobility limits employees' flexibility and responsiveness. Mobile solutions enable real-time access to data, task management, and better communication.
Lack of a tracking system. Without a tracking system, inventory visibility suffers, leading to inaccuracies. A tracking system allows for real-time monitoring and proactive management.
Lack of a labeling system. The lack of a labeling system complicates organization and product identification. A labeling system provides clear product identification and streamlines processes.
Lack of integration with other systems. Operating in isolation leads to data silos and fragmented workflows. Integrating other systems available in SCM improves data flow, automates processes, and improves decision-making.
These are only some problems in warehouse operations. So, let's say that your warehouse needs to solve one of these problems. You won't need robust WMS software with a comprehensive management system, but you will need some of these capabilities embedded in your solution and integrated well with legacy systems.
It is simple, and this is where custom logistics software development can help you the best. You can save time and money that way, and for real, use WMS system capabilities, regardless of the types of warehouse management that are needed (based on stock, industry, etc.). What can be more important if you're a small and medium-sized business? Also, you can always exceed your operations by using existing WMS system capabilities. So, a good example of custom software development can help you scale cost-efficiently.
Are you in search of a reliable tech partner?
Adexin can help with advanced logistics solutions
Contact usFinale takeaway
A warehouse management system (WMS) is an essential tool for modern companies. It revolutionizes inventory management, order fulfillment, dock planning, and warehouse mobility. Today, companies rely heavily on WMS systems to ensure efficient warehouse operations and meet customer demands, and we've helped them do just that.
We have defined warehouse management systems through firsthand experience in the supply chain industry. We highlighted their key role in facilitating various aspects of warehouse operations. WMS systems play a key role in ensuring smooth and efficient workflows, from inventory receiving to order processing, picking, packing, shipping, and returns processing.
Contact us today if you want to revolutionize your warehouse operations with a customized WMS solution. We can help you with the WMS system and fleet management software development and integration. Moreover, we can help adapt types of warehouse management to your particular needs, whether you need cloud-based warehouse management or on-premises. Learn how our software development expertise can help you streamline your workflows. It's time to improve efficiency and drive business growth.