Warehouse management software for small businesses is a solution dedicated to companies in logistics and supply chains that want to keep costs low and, at the same time, remain competitive. How does this work in the actual case scenario? That simply explains why, if you're a small or medium business, you need only certain capabilities that can solve your most urgent business problems. In other words, you may need to transform your business operations from paperwork to mobile registration partially.
By working directly in logistics and logistics software development, I have observed a counterproductive trend that is also understandable. I saw companies that run orders picking on paper sheets, and all of that is still in 2022. It's ineffective because it creates enormous manual tasks, but it was understandable that the manager wanted to keep costs low and customers happy. By taking one life example from the logistics distribution business in the supply chain, we'll consider why small and medium enterprises may need a WMS system today more than ever.
We'll share brilliant examples from the EMEA and APAC regions involving international logistics to show why you might take that step in developing your customized WMS system. All that and a bit more in our article below.
Warehouse management system and its impact on service level
In the very first instance, you may ask yourself why you need the best warehouse management software if you're a small or medium-sized business. As stated above, it's clear that if you implement small business warehouse management software, you'll most likely want to increase prices for warehouse services. It can make your customers unhappy. This trend is evident in the supply chain, where small business operations, even in more prominent logistics companies, are still utilizing paperwork for tasks like picking, packing, or inventory control.
It boils down to the fact that, to some extent, it is still more affordable to keep hiring people for minimum wage than to implement a modern system that will increase service prices, and you still need to hire the same people.
If an order picker has a mobile device with the picking list, he can work faster, but he still needs to be there the same way with paper to pick the orders. Order management on the warehouse floor still requires people. Nevertheless, we conclude that having a WMS system is still vital if you're a small or medium-sized business. But first, we want to summarize what is needed most for your small business warehouse management software.
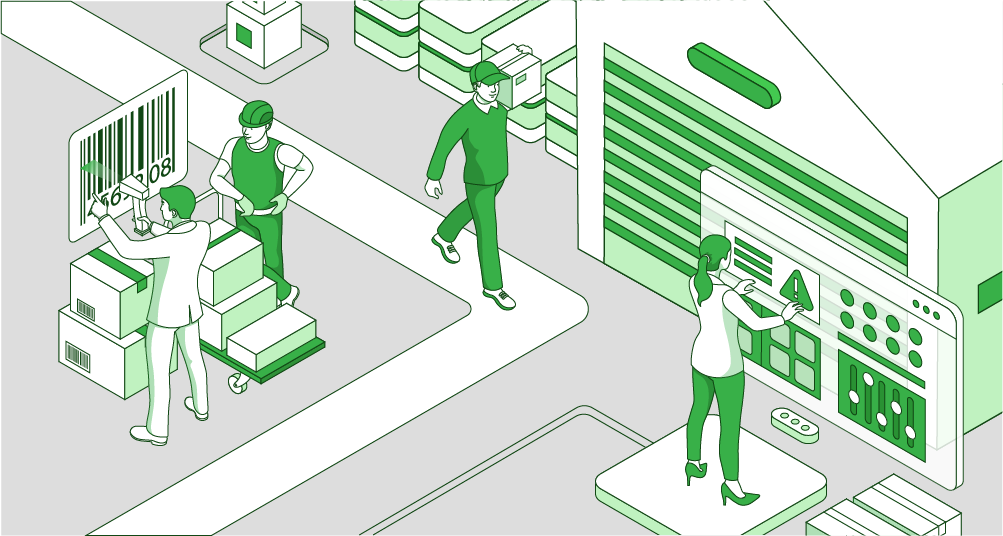
Here are the elements that are crucial for your WMS system if you're an SMB:
Real-time inventory tracking throughout the supply chain.
Know about inventory levels, sales velocity, and arrival of shipments.
Analyze sales to forecast demand and plan materials.
Ensure adequate inventory to meet demand.
Access inventory information for warehouse staff, vendors, and managers.
Maximize control by reducing dead stock and shortages.
Optimize warehouse picking processes.
Generate reports for inventory analysis.
Track inventory across warehouses and points of sale.
Set workflow alerts for quick replenishment of inventory.
Manage cash flow through better inventory management (here comes some financial analytics)
It's clear now that a considerable volume of operations dedicated to WMS systems comes through warehouse inventory management software for small businesses. And that's true; if you're a small or medium-sized business, your first thought about implementing software should be inventory management.
If you familiarize yourself with professional warehouse inventory management software, you'll be more accurate and cut costs. We're not talking here about limiting warehouse clerks in favor of more digitized processes or directly increasing warehouse service prices.
The main thing is gaining a competitive edge because if you're empowered to convince customers that by having dedicated software for accurately managing stock levels, you can ensure them you're doing a good job.
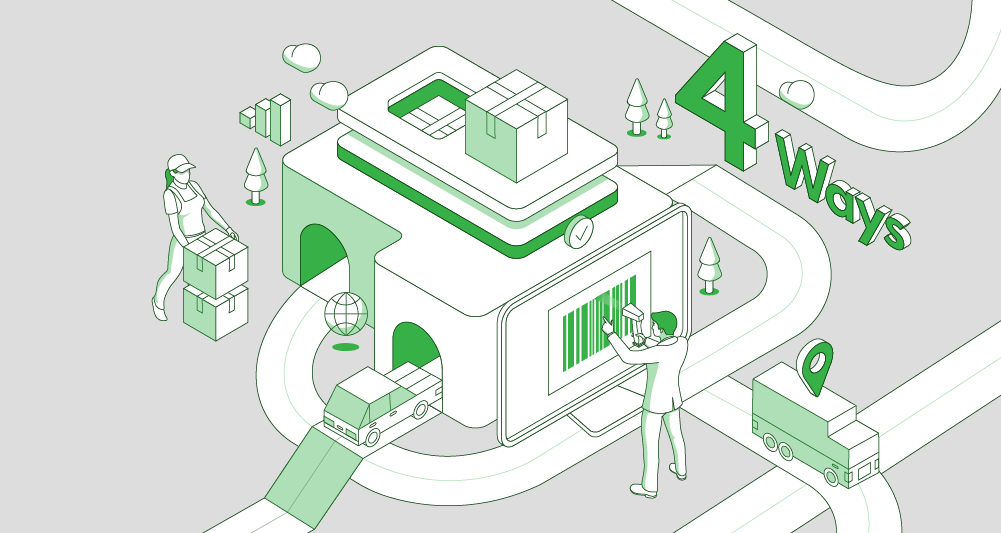
How warehouse management software influence your business risks
Converting your customers to a contract logistics service model isn't an easy task. They don't just come to you without effort. The procurement process can last months and often results in nothing. If you have a warehouse and store goods from manufacturing, etc., the challenges of managing inventory and acquiring customers are pretty similar.
You may still lose your goods due to missing items, damages, or lack of a return process based on WMS. There are plenty of reasons for this. By leveraging our experience in the logistics industry, we aim to help you understand what can happen if you don't have a WMS system.
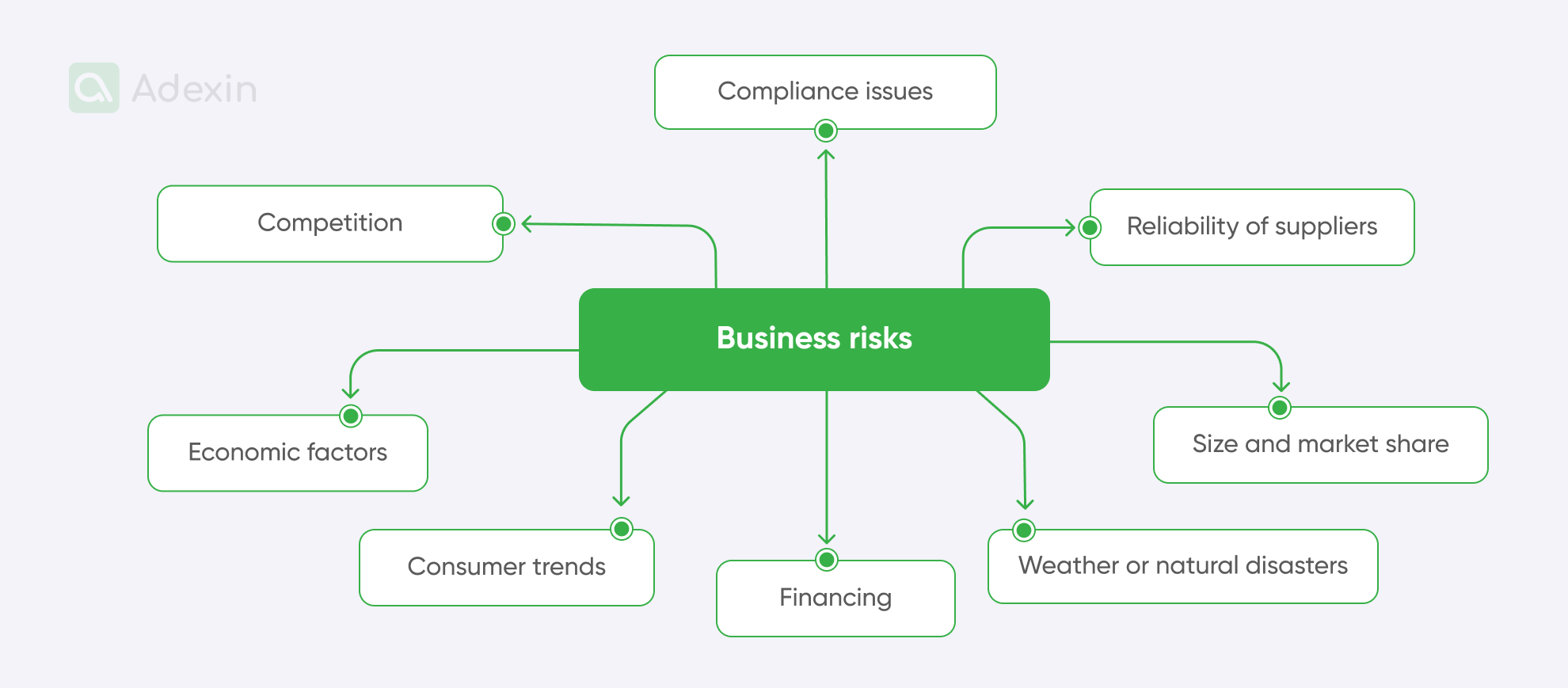
Below, we've listed things that are out of your control and can make it harder to run your business without WMS:
Compliance issues
Reliability of suppliers
Competition
Economic factors (price and availability)
Size and market share
Consumer trends
Financing
Weather or natural disasters
The risk that you can have under control with the WMS system
Inventory management and inventory inaccuracies
WMS provides real-time tracking and automatic inventory updates, ensuring accurate inventory levels. You can prevent stock shortages and lost sales.
Order fulfillment errors
A WMS streamlines order picking and packing processes, using barcode scanning and automation to minimize errors. Incorrect orders can result in dissatisfied customers, so having them under control automatically gives you these advantages.
Inefficient use of space
A WMS optimizes warehouse layout and storage locations, improving space utilization and reducing unnecessary movements. You can prevent poor space management and overloaded warehouse areas.
Labor inefficiencies
A WMS improves labor productivity by optimizing task allocation. It allows you to track performance and reduce manual interventions. With the right warehouse management system, you can remove manual processes and inefficient labor, which means reducing wasted time.
Outdated stock
A WMS helps manage inventory rotation (FIFO/LIFO), ensuring that older inventory is used or sold first to reduce obsolescence. You avoid expired inventory, thus preventing substantial financial losses.
Data security breach
WMS includes security protocols and access controls to protect sensitive information and limit unauthorized access. You can prevent unauthorized access to your system from the warehouse level and against security breaches and data loss.
Inconsistent reporting and analysis
WMS provides accurate and consistent reporting and analysis, enabling informed decision-making and performance tracking. You can finally stop with Inconsistent or inaccurate reporting.
Supply chain disruptions
A WMS provides greater visibility into the supply chain. The system facilitates proactive management and rapid response to disruptions. Again, you can avoid delays and increased operational costs.
Loss Prevention
Theft, damage, or loss of inventory can significantly impact profitability. A WMS increases security through tracking and monitoring, reducing the likelihood of theft or loss.
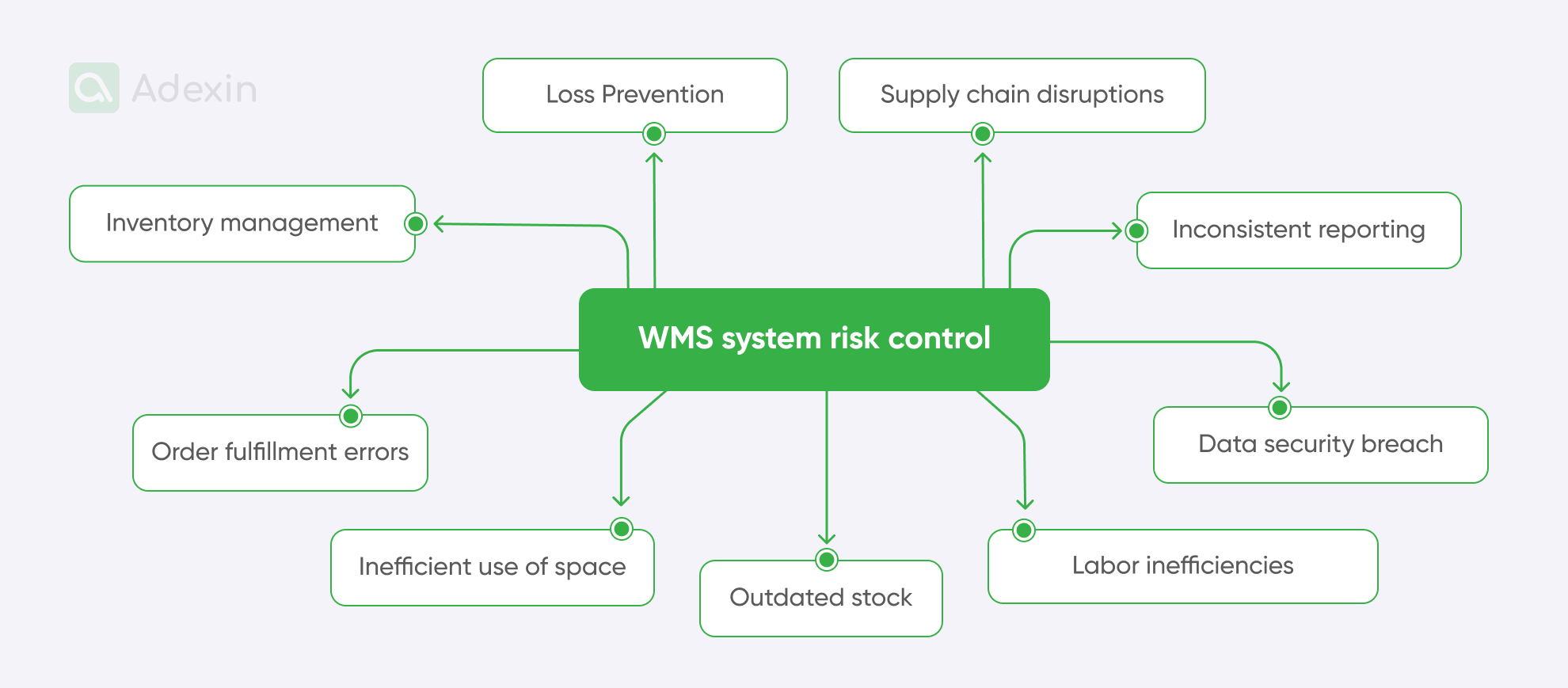
So, by saying this, you really manage your stocks better with WMS. This will also be a huge factor that can influence your customer to work with you in contract logistics. This also benefits your warehouse or distribution center, even if you run your own warehouse or rent your service based on contract logistics.
In every exceptional company, scaling is a priority. Growth is a natural part of the logistics business. With a WMS system, you can rapidly increase your capabilities and be more convenient for your future business partners. It's also easier to dictate new fees for your services with existing customers if you properly explain to them these features of WMS, so the areas that you'll have under control with WMS.
Need help with warehouse management systems development?
Learn how we can help you
Explore moreBenefits of using WMS for small business
As a small and medium-sized business, you may still not be as efficient as you'd like without a WMS system. It's hard to predict exactly what can cause your inefficiency, but based on our experience, we know that some risks impact your business even if you have WMS. It is because poor management and lack of skills are indispensable factors. Even with sound systems, you may need to know how to problem-manage your business operations effectively.
Knowledge of logistics can help you manage operations better and pursue your business goals. We have listed several elements in warehousing that require special attention and help you yield faster results when working with the WMS system.
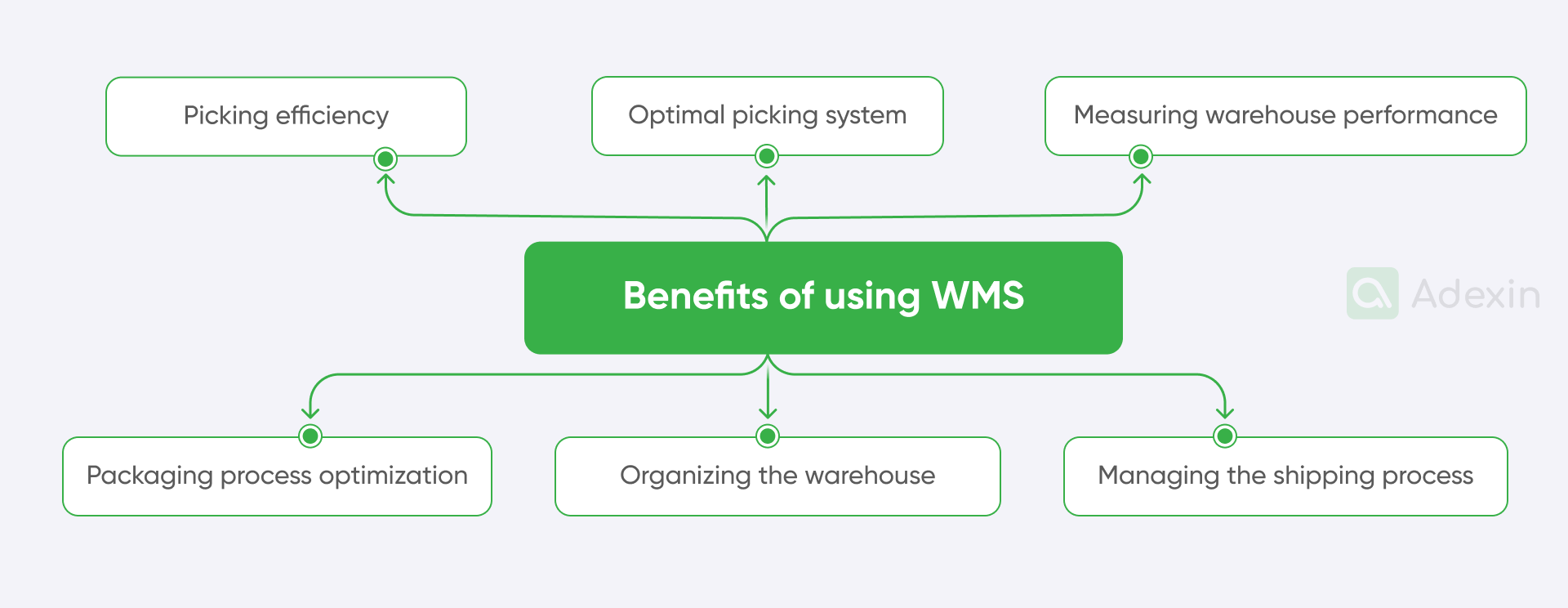
Here is what you can do better with WMS and what needs to be handled with greater attention:
Organizing the warehouse with the best inventory management software
Proper inventory organization and placement are critical to efficient warehouse operations. Without a WMS that automates and optimizes this process, you may have difficulty arranging your inventory, which can lead to difficulty locating products and increased picking times.
Picking efficiency for inventory management
Without a WMS, you may face challenges in efficiently receiving incoming inventory, leading to delays, errors, and inefficiencies in warehouse operations.
Optimal picking system
An optimal picking system is essential to maximizing the efficiency and accuracy of warehouse operations. Without a WMS that helps implement and manage picking strategies, such as batch, zone, or wave picking, the picking process can experience inefficiencies and errors.
Packaging process optimization leading to efficient inventory management
Optimizing the packing process is another critical aspect of efficient warehouse operations. Without a WMS, you may face challenges ensuring that orders are packed accurately, efficiently, and safely. Implement efficient packing procedures, such as using suitable packing materials, optimizing packing station layouts, and optimizing productivity.
Measuring warehouse performance for better inventory management
Monitoring and measuring warehouse performance indicators, such as order fulfillment rates, inventory turnover, and picking accuracy, is critical to identifying areas for improvement. Without a WMS that provides accurate and comprehensive data analysis, you may struggle to measure and manage warehouse performance effectively. So, in fact, your WMS software has inventory management system capabilities.
Managing the shipping process
Effective management of the shipping process, including order packing, labeling, and carrier selection, is critical to timely and cost-effective order fulfillment. Without a WMS that streamlines shipping operations and integrates with carriers, you may encounter delays, errors, and increased shipping costs.
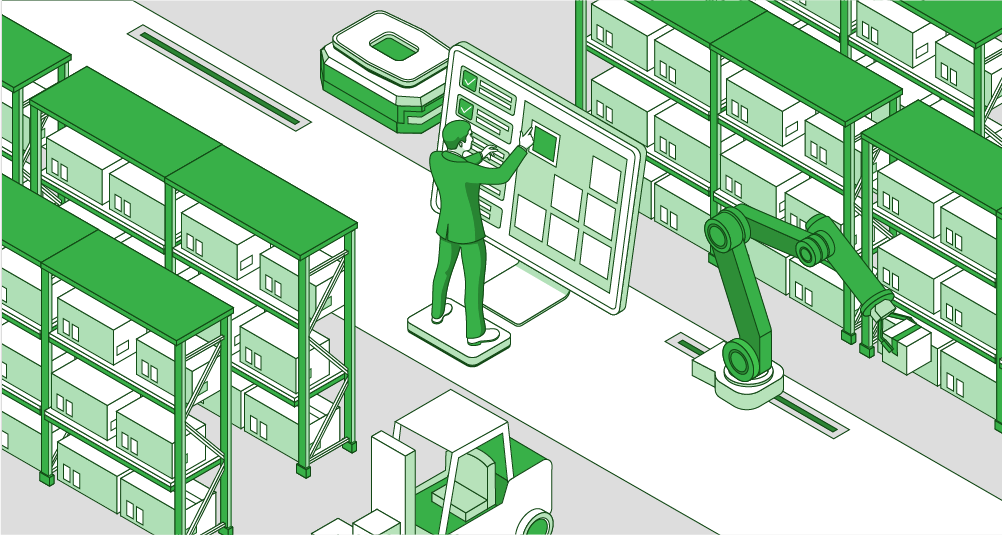
What are the benefits of a custom next-generation WMS?
Moving through the subject of how WMS can help small and medium-sized businesses, we've already touched on the relevant benefits of using it. However, through conversations with hundreds of logistics companies during trade fairs like LogiMAT in Stuttgart, Breakbulk Europe, Logistics Summit, and other major European events, we found that logistics companies are struggling with sales. This struggle revolves mainly around a unique selling point (USP).
Companies should learn to leverage WMS systems relevant to the service quality level they can provide to customers. It's about keeping costs low and considering other factors that can benefit our business. Customization is critical when we're talking about the next generation of WMS. It is what today's customers are expecting.
If you're selling to the food industry, you must comply with regulations and provide your customers with unique value that your WMS can deliver. The same applies to handling goods in heavy industry, chemicals, or e-commerce.
Today, WMS systems built based on customized software are one solution you may create on request to comply with each niche you work for. You can make your system unique for your customers by working with experts like Adexin, which delivers first-in-class WMS systems for small and medium-sized businesses.
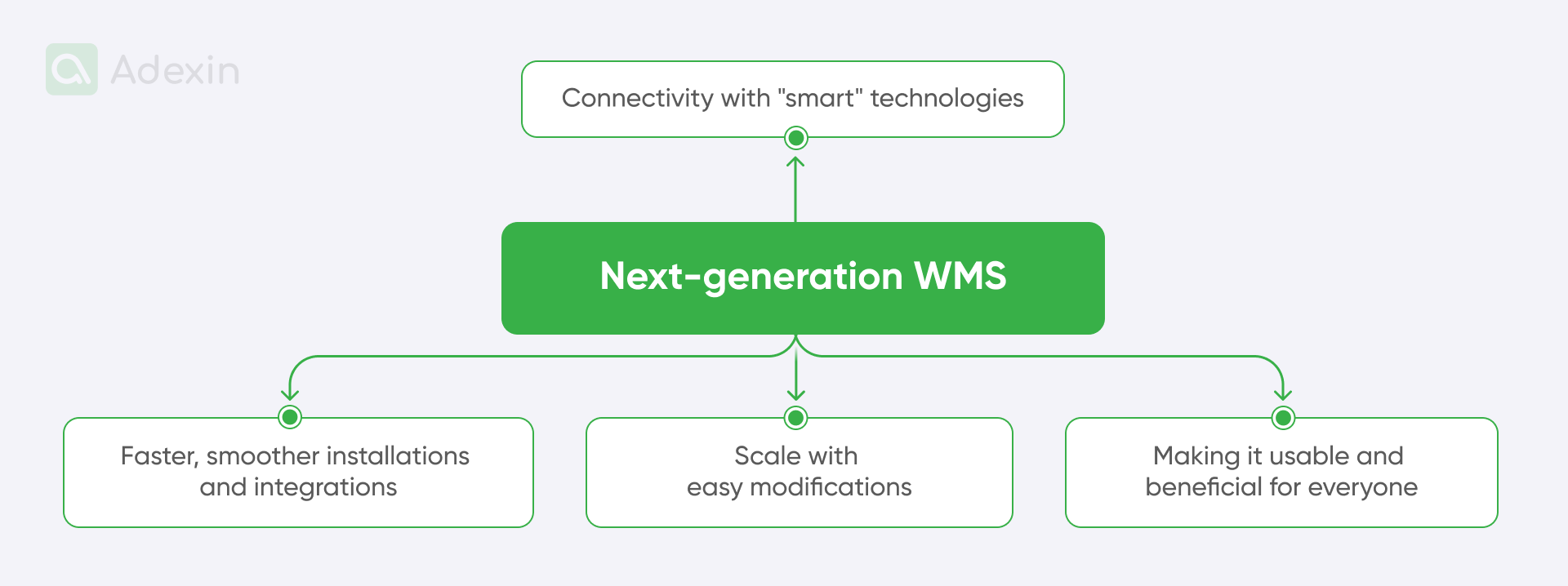
Here are the benefits of WMS you can receive with a custom system development from Adexin:
Connectivity with "smart" technologies
WMS customization enables integration with new "smart" technologies such as IoT devices, RFID tags, and AI-based analytics. By leveraging these technologies, you can increase visibility, automate processes, and improve decision-making in warehouse operations.
Faster, smoother installations and integrations
Personalization of the WMS enables customized integration with existing software and hardware infrastructure. It provides capabilities of inventory management software. It ensures faster deployment and seamless integration with business processes, minimizing disruption and maximizing productivity.
Scale with easy modifications
A custom WMS system can be designed to fit your company's unique growth trajectory. With easy modifications and upgrades, you can scale your system to meet changing operational requirements, whether expanding into new markets, adding product lines, or increasing order volumes.
Making it usable and beneficial for everyone
Personalization enables you to design user interfaces and workflows that cater to specific employee needs and preferences. By creating intuitive interfaces and customized features within your WMS, you can increase user engagement, productivity, and satisfaction at all levels of your organization.
Are you in search of a reliable tech partner?
Adexin can help with advanced logistics solutions
Contact usFinal takeaway on the warehouse management system for small businesses
Small business warehouse management software offers a tailored solution for logistics and supply chain companies aiming to balance cost efficiency with competitiveness. By tailoring WMS systems to specific levels of service quality, companies can effectively address their most pressing challenges, moving from manual to mobile operations. This transition is critical to streamlining processes, increasing productivity, and meeting customer expectations.
To further understand why small and medium-sized businesses need WMS systems now more than ever, we've outlined the critical elements required for successful small business warehouse management software. These include real-time inventory tracking, sales forecasting, space optimization, labor productivity, and more, all essential to improving overall operational efficiency and gaining a competitive edge.
Contact us now to learn how a customized WMS solution can revolutionize your small business and give you greater efficiency and profitability.