We all know what prevents us from achieving good results in a warehouse. Disorganization is the biggest enemy of any warehouse, but effective people management is equally important. We constantly consider how to tackle specific issues in our workspace cost-effectively.
Research shows that the placement process alone can account for up to 36% of overall warehouse costs. This error-prone activity clearly poses a risk to warehouse operations and transportation costs. A single wrongly packed and damaged package can significantly impact returns and efficiency.
In this article, we point out 5 major warehouse errors and how you can improve them. We rely solely on our experience in logistics and supply chain, and we're sharing this info to help others.
As a former business analyst in the supply chain field, I aim to provide a reliable perspective on improving your current warehouse situation. You can rely on our knowledge and get the right perspective on your current situation in the warehouse and how it could be improved. See below what we've prepared for you to help secure your warehouse operations.
Top 5 problems of warehousing operations
Order picking is a critical and costly process within internal logistics, often consuming over 50% of total warehouse expenses. This is due to its labor-intensive and time-consuming nature. Undoubtedly, it involves significant manual handling that also impacts employee safety.
Errors in retrieving products for customer orders can lead to substantial financial repercussions. These include costs associated with accepting returns and significant additional labor for handling and checking returned items, re-picking, re-packing, re-delivery, and administrative overhead.
Furthermore, such errors can negatively affect cash flow due to unpaid invoices. They may even result in stock write-offs if returned products are damaged or past the acceptable delivery timeframe.
Given the significant impact on costs and customer service quality, the logistics sector and researchers are investing in modern technological solutions to optimize order-picking processes. But before we dive into these solutions, we should clearly state the five major warehouse errors. Below, we've split each error into three levels. This can help you better understand the overall structure of each issue you might face in your warehouse operations.
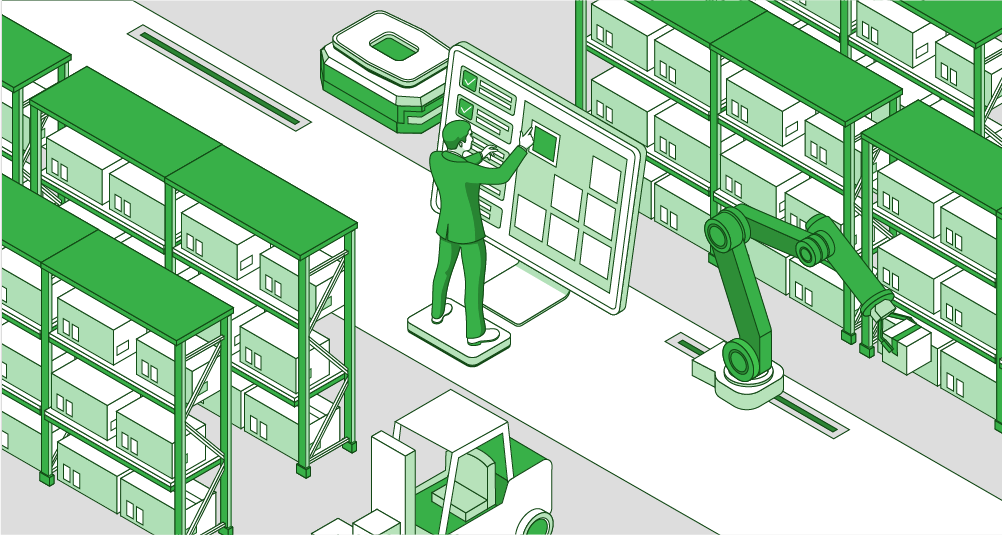
1. Poor inventory management
Poor warehouse environment. Inaccurate stock levels directly impact customer satisfaction, leading to unfulfilled orders or delayed shipments and, subsequently, lost sales opportunities when products are out of stock. This pervasive issue also negatively affects supplier relationships due to inconsistent order forecasting.
Lack of warehouse automation tools. Internally, poor inventory management leads to a lack of real-time visibility into stock, making it impossible to make informed decisions. This drives increased carrying costs due to overstocking and obsolete inventory and causes staff to waste time searching for items or reconciling discrepancies, ultimately hindering operational efficiency.
I think, instead of beating around the bush and questioning us, "Why are we constantly playing catch-up with our inventory instead of being in control?" – we should move further with a software solution. So, instead of perpetually reacting to stock shortages and surpluses, we must cultivate a mindset of proactive foresight and precision. We should view inventory not merely as static goods but as a dynamic flow of value that requires continuous understanding and intelligent anticipation.
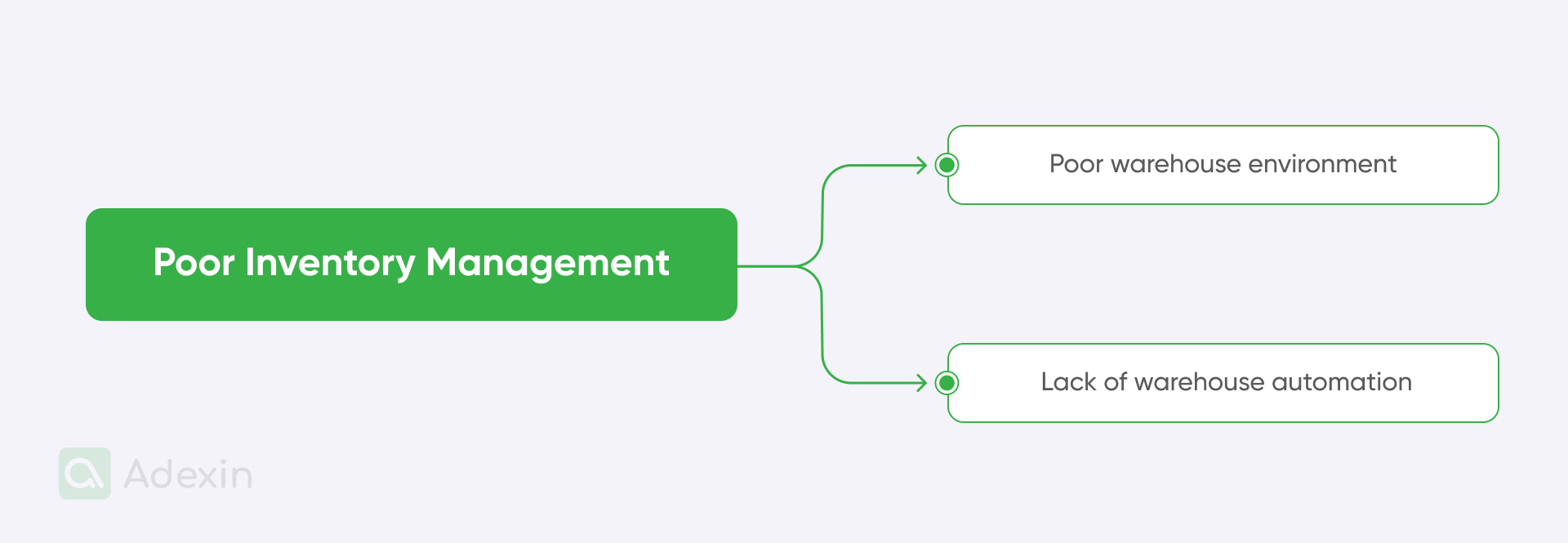
2. Inefficient picking processes
Poor picking and packing errors. Inefficient picking processes result in slow order fulfillment, extending customer lead times, and generating high warehouse picking error rates that lead to incorrect or incomplete orders. This directly indicates that maintaining customer satisfaction increases returns. Well, this ultimately damages brand perception due to unreliable delivery.
Poor warehouse management software. Well, narrowing this subject internally, we see that inefficient warehouse picking processes manifest as non-optimized pick paths, leading to unnecessary travel time and fatigue for pickers. This directly results in increased labor costs due to the inefficiency of manual and unguided processes and a lack of traceability for items picked, making it difficult to pinpoint errors and ensure accountability.
Looking at this with the question, "Why are our pickers still running marathons through the warehouse when technology could guide them to the finish line?" We may have a simple solution. The solution lies in elevating the act of warehouse picking from a manual task to a guided orchestration of efficiency. We must embrace technology not as a replacement for human error but as an intelligent partner that liberates our people from needless movement and error. This will allow them to focus on the precision and quality of fulfillment.
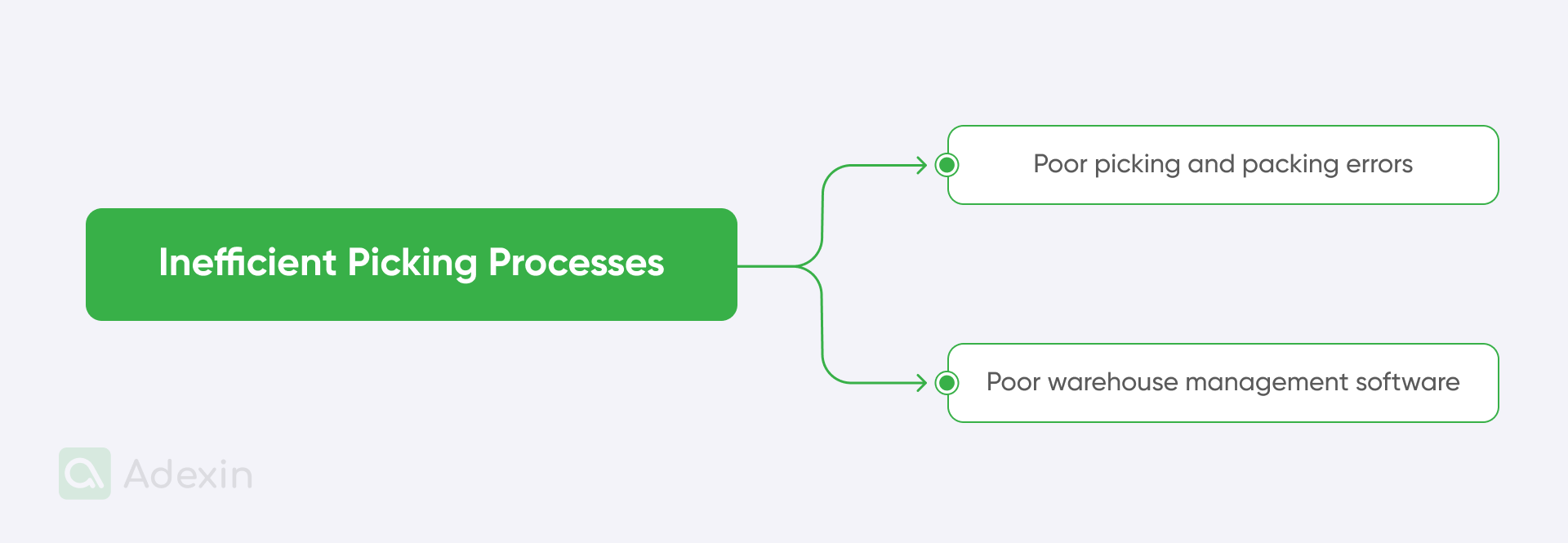
3. Inadequate space utilization
High manual error rates. Inadequate space utilization limits the ability to scale operations to meet increased demand or store new product lines. Congested docks cause delays in inbound receiving and outbound shipping. If storage capacity is consistently maxed out, this can also constrain correct product offerings.
Lack of autonomous mobile robots. From an internal perspective, inadequate space utilization is marked by wasted vertical space and horizontal space due to poor warehouse layout and storage design. This creates overcrowded aisles and workstations that reduce safety and productivity and significantly increase time spent locating items, as an organization is compromised.
By asking ourselves, "Why are we paying for empty air or tripping over boxes instead of maximizing every square foot of our expensive warehouse space?" we should focus on firm solutions. We must fundamentally shift our perspective on warehouse space from a fixed, finite constraint to a fluid, optimized resource. Every cubic foot holds potential, and by consciously designing for flexibility and maximizing density, we are not just storing goods but intelligently investing in future capacity and operational fluidity.
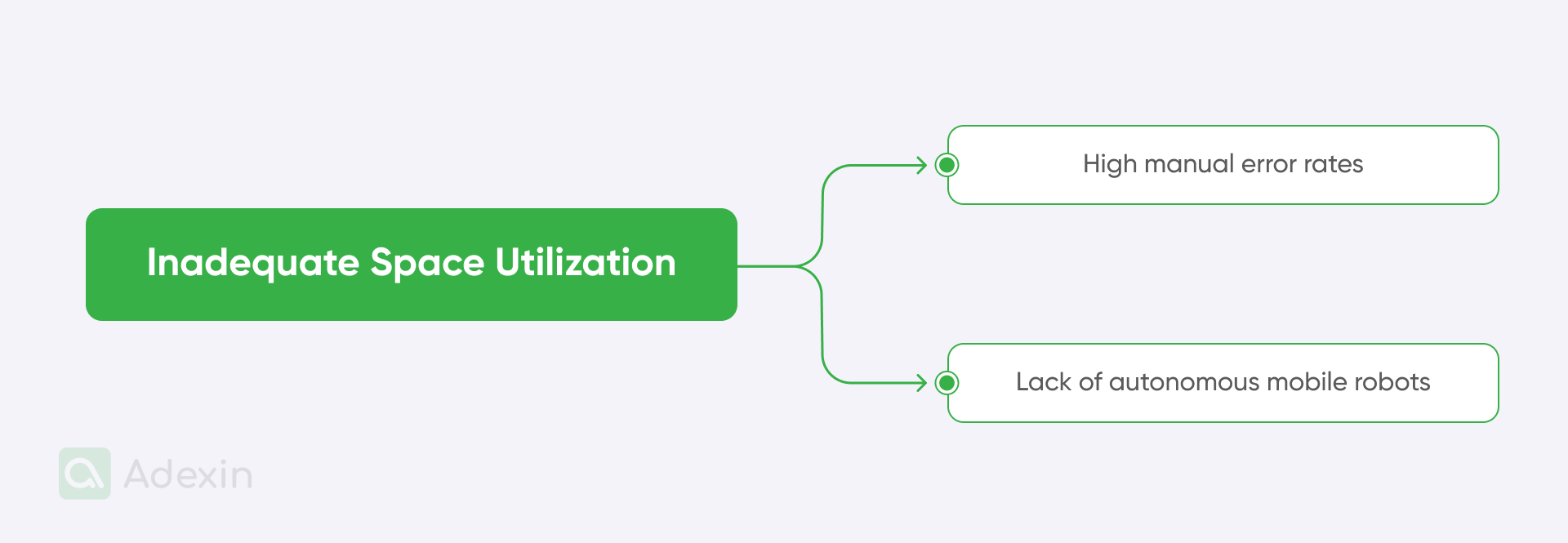
4. Lack of standardized procedures
Correct item not in hands. A lack of standardized procedures leads to inconsistent customer service quality due to varying operational standards, making it difficult to meet service level agreements (SLAs) because of unpredictable performance. This ultimately reduces customer trust when processes are unreliable.
Lack of automated storage and retrieval systems. The lack of standardized procedures results in variability in performance across shifts and teams, leading to an unpredictable operational rhythm. This also drives increased human errors due to reliance on individual discretion rather than clear guidelines and significantly slows the onboarding of new staff as there are no consistent workflows, standard operating procedures (SOPs), or MOPs.
We may think: "Why is every shift a unique adventure in problem-solving instead of a predictable, well-oiled machine?" The path to consistency is paved with clarity and shared understanding, not rigid dogma. We must instill a culture where best practices are not merely documented but deeply understood, continuously refined, and consistently applied by everyone.
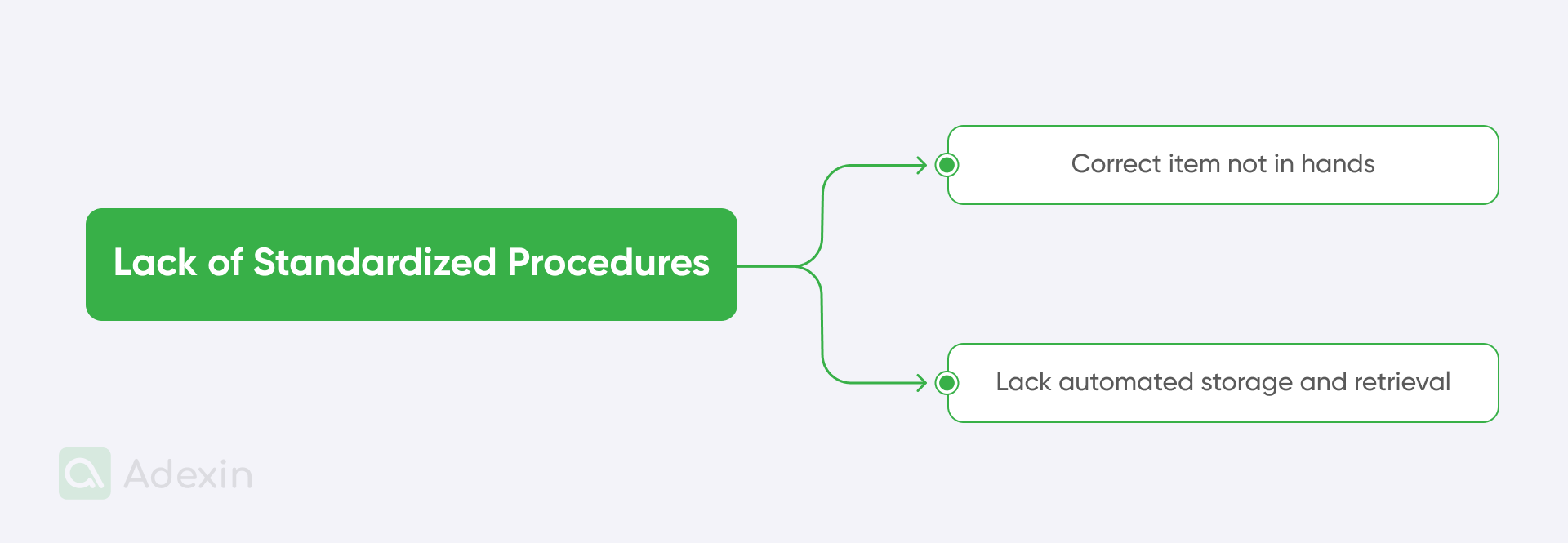
5. Weak returns management
Messy warehouse. Weak returns management results in a slow and inefficient returns process that frustrates customers and impacts their likelihood of re-order. Delays in refunds or exchanges lead to negative customer experiences, which ultimately contribute to a damaged brand and company’s reputation.
Lack of advanced warehouse technologies. Going further, from the internal perspective of that problem, weak returns management is characterized by increased operational costs due to the manual handling, inspection, and processing of returns. This also leads to tied-up working capital as returned items are not quickly restocked or disposed of. A critical lack of visibility, automated storage and retrieval systems, as well as tracking of returned items, leads to lost inventory or too much inventory and accounting discrepancies.
Looking at this more broadly, we may ask: "Why does managing returns feel like a black hole where products disappear and profits get swallowed?" Instead of viewing returns as merely a logistical burden, we must philosophically embrace them as a critical component's touchpoint for customer loyalty and a valuable source of insight. By transforming the returns process into a seamless, transparent, and respectful experience, we not only recover value but also reinforce trust and gain data to prevent future issues.
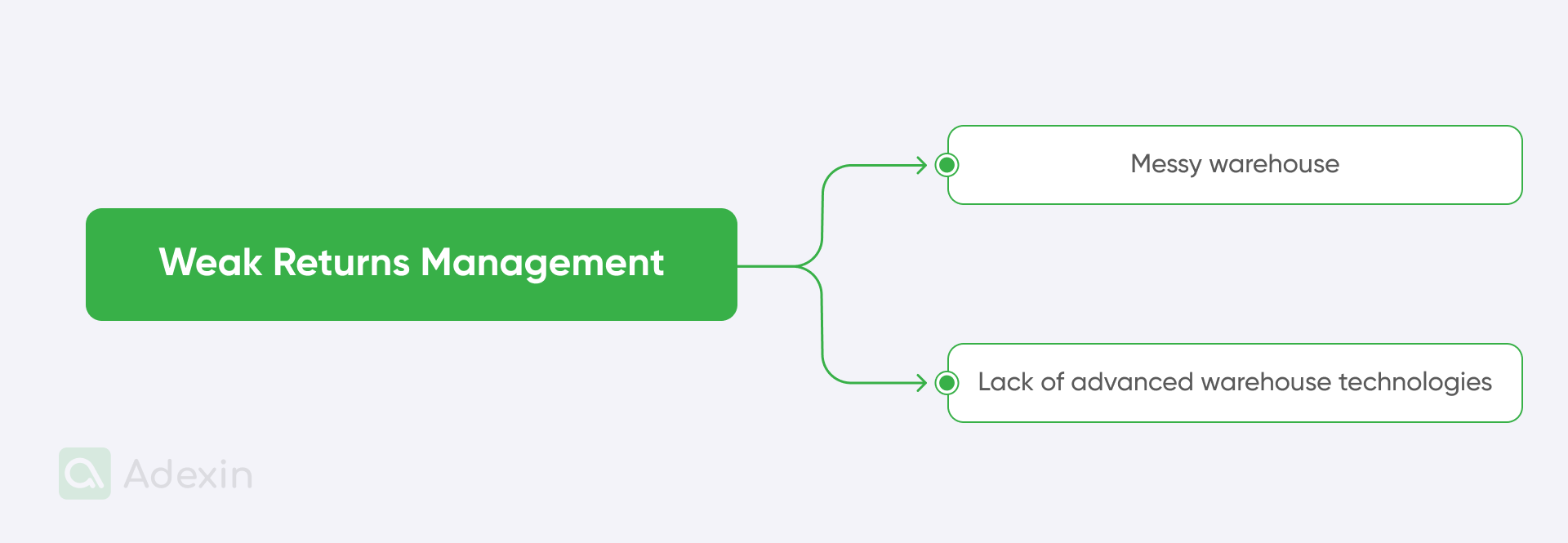
Solving warehousing challenges with custom tech
We all understand the challenges that hinder optimal warehouse performance. Disorganization is a primary adversary, but effective people management is equally crucial. Continuously, we seek cost-effective solutions to specific workspace issues. At Adexin, we understand the complexities of logistics and are here to help you solve your warehousing challenges with tailored logistics technological solutions.
Here's how we partner with you:
Your dedicated technology partner. We position ourselves as a technology partner, not just a vendor. We pride ourselves on a deep understanding of logistics and supply chain, ensuring our solutions seamlessly fit into your existing business workflows rather than forcing disruptive change. Our commitment is to deliver working, tailored digital solutions that truly address your needs.
Empathy in implementation. We know how challenging it can be to implement new IT systems in live logistics environments. That's why we don't just push pre-built systems, we create them with you, ensuring they align perfectly with your unique operations and minimize disruption.
Well, we’re sure that, while the market typically offers three types of solutions for logistics and warehousing needs, like existing solutions for quick implementation, hybrid approaches that combine off-the-shelf tools with customized modules, and fully customized software built from scratch, Adexin exclusively specializes in and provides fully customized software.
No matter the complexity, our goal is to deliver a solution that precisely fits your operation, providing the flexibility and precision that off-the-shelf options simply cannot match. Our expertise is proven through real-world applications.
eProcurement solution for educational resources
For a client seeking to streamline the procurement of educational materials, Adexin developed a custom eProcurement platform. This solution optimized the entire purchasing workflow, ensuring efficient resource allocation and cost savings by tailoring the system to their unique organizational structure and supplier network.
Lightweight warehouse management system
We partnered with a business that needed a highly specific, agile WMS that existing large-scale systems couldn't provide without significant overhead. Our custom-built, lightweight WMS precisely addressed their inventory tracking, order fulfillment, and operational visibility requirements, leading to streamlined warehouse processes and improved accuracy.
Need help with warehouse management system development?
Learn how we can boost your logistics processes
Explore moreThe high cost of ignoring warehouse errors
The insights shared in this article highlight the critical need to address warehousing errors to ensure efficient and cost-effective logistics operations. Ignoring these issues can lead to significant setbacks, but proactive solutions can unlock a future of seamless growth and enhanced performance.
Delaying action on these critical warehouse issues isn't just maintaining the status quo, it's actively choosing a path of inefficiency and escalating costs. You'll continue to battle delays and penalties as you rely on cumbersome manual processes like Excel spreadsheets. Uncoordinated processes will lead to wasted logistics spending, often 1,5 to 2 times more than necessary, as different departments or warehouses operate in silos. But believe me, after nearly 10 years in the supply chain, I could deliver more cases as an example that you could consider.
Your warehouse managers receive instant alerts when something goes wrong, allowing swift corrective action before minor issues become major problems. This isn't a pipe dream, it's a reality we've delivered in real projects. Again, please believe me, there might be much more of that.
Are you in search of a reliable tech partner?
Adexin can help with advanced logistics solutions
Contact usFinale takeaway
Don't let inefficiency hold you back. It's time to move beyond identifying problems and start implementing real solutions. Let's discuss your logistics processes: We'll draft a technical approach and timeline tailored to your needs.
The questions we've posed throughout this discussion, like "Why does logistics still feel like it's stuck in 2005?" or "Why does managing returns feel like a black hole?" underscore a collective frustration with inefficiencies that are no longer acceptable in today's dynamic market.
At Adexin, we understand these complexities intimately. We know that off-the-shelf tools often fall short of unique business needs, and implementing new IT automated systems in live logistics environments can be daunting. That's why we position ourselves as your dedicated technology partner, crafting solutions with you, not just for you.
Don't let your logistics feel stuck in the past. Partner with Adexin to unlock seamless growth and enhanced performance. Visit our website or contact us today for a free consultation and discover how tailored technological solutions can revolutionize your operations.