Logistics businesses create a net where there are various dependencies. As a logistics manager, you need to focus on many areas, such as financials, shipping costs, material handling, customer services, and people management, which are highly important for daily operations. It's good to rely on the expert's knowledge. In this article, you'll get to know how we helped businesses manage their operations better by giving you insights into our work and real examples from my personal experience working in logistics and supply chain.
What is the importance of logistics?
The importance of logistics management starts from the very foundation of your daily operations. It involves an interdependent network characterized by smooth daily operations, excellent customer service (which is crucial in B2B logistics), clear communication, and transparency. There are several more factors outlined below that are important for logistics managers and are helping in shaping better logistics strategy.
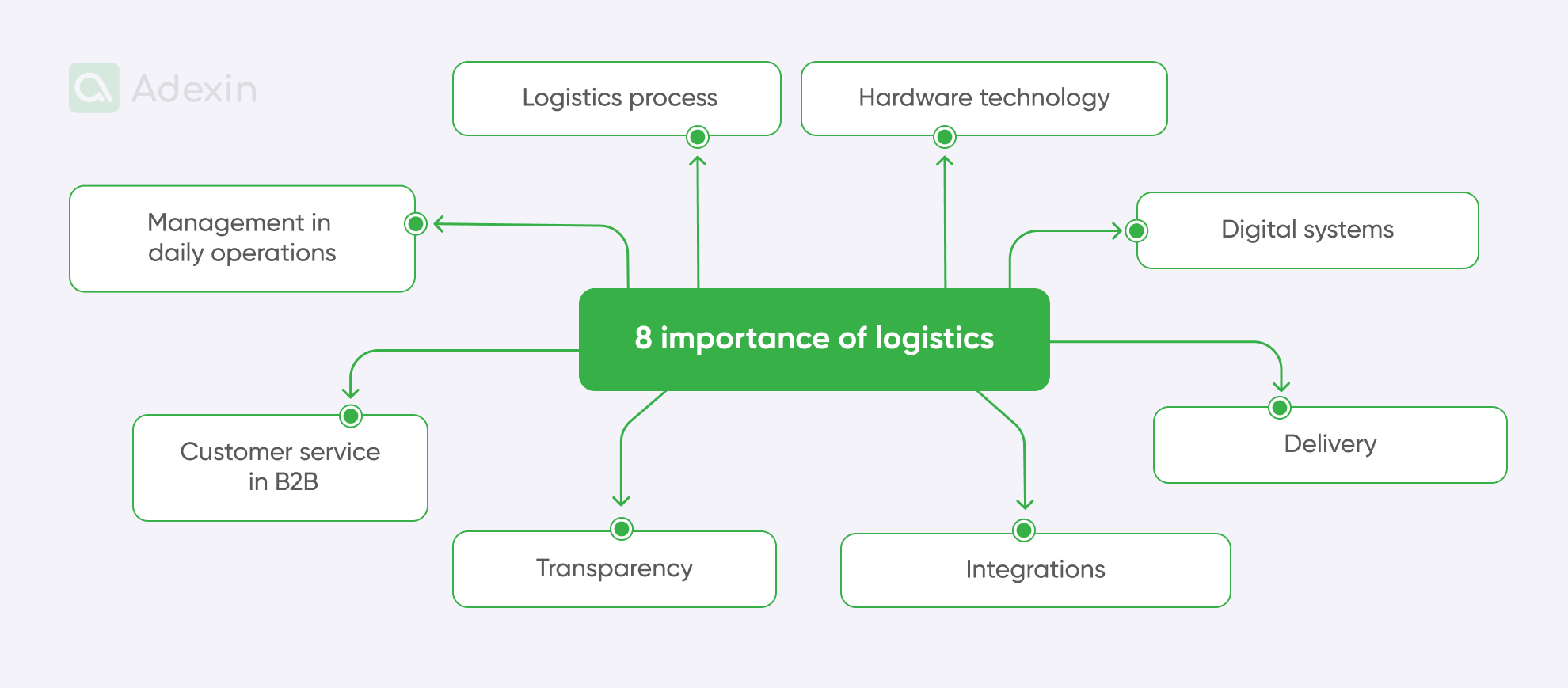
1. Significance of logistics management in daily operations
Companies need to be cautious in monitoring daily operations. It is very significant to manage logistics because this is not a job that you can forget one day and come back to another. Logistics management's first importance is understanding that solving everyday problems and all operations involves what will bring you more fruitful benefits each week in the entire supply chain.
Let's give an example from a digital Hi-fi goods producer. Such a company produces high-quality sound systems and distributes them from a warehouse in the Netherlands in the EMEA region. That company is using fulfillment logistics services from a logistics provider. Let's assume that your logistics company provides fulfillment services. You should focus on various aspects of this e-commerce business and keep it up and running. All operations, from inbound logistics to outbound logistics, depend on you and your team's daily logistics strategy. All that to get customer expectations delivered. Thousands of orders will be daily, and many issues can happen along the way. You need to be cautious about various aspects of your business. Your customers will most likely require quarterly reviews and weekly KPI reviews, so you need to provide them with good results weekly.
Many issues in logistics can be solved with custom software development services that can replace and automate your particular tools used in the warehouse. Custom software can help eliminate your reliance on MS Excel tools in your core operations. If your team members need proper knowledge about calculations, macros, and VBA in MS Excel, this tool can be insufficient to manage your data. We have helped various companies tackle these problems through a range of solutions such as an Excel-to-Web platform for the procurement sector, as well as more extensive solutions such as applications to help truck owners or parking lot operators app. These Adexin’s solutions can not only optimize operational work but also significantly save time on providing services, as well as optimize income and KPIs. So, it's worth considering how logistics management software can improve your operations.
Need help with custom mobile app development?
Learn how we can boost your logistic business processes
Explore more2. Customer service in B2B and covering customer needs
Customer service (CUS) is highly important in B2B logistics. Even if your business remains well organized, you cannot anticipate and have policies for all issues upfront. There is always a learning curve in each business where serious issues arise, like during the COVID-19 pandemic, and you need to learn how to solve these issues and balance communication with customers.
While working in logistics, I remember when my truck cargo was obligated to wait hours in lines at the Bulgarian-Romein borders during transit from Istanbul, Turkey, to Venlo in the Netherlands due to longer control checks regarding security and healthcare. Customers were impatient, and it wasn't easy to accept that the cargo wasn't yet in the Netherlands.
Customer service operations were crucial, where people from the Control Tower could balance negative feelings. What I know for sure is that many companies don't have a CUS department. There is limited communication between carriers, customers, warehouses, etc. This lack of communication is the root cause of shallow customer satisfaction.
3. Transparency that brings overall quality
What is essential is to provide transparency, both internally and externally. It means keeping all stakeholders informed. So, in the very early stage, you must develop a suitable communication matrix and system to handle operational issues more effectively. When it comes to your customers, they will trust you more when your business remains transparent. When it comes to your people, they will feel safe and help you secure the company by, for instance, their ability to solve problems quickly. If they know about the issues faster, they can resolve them faster.
Let's give an example from logistics. Internally, when you have established a good communication matrix, your people should know whom to contact in particular cases. The communication matrix might be shaped as a contact organogram list with all the people responsible for some instances in logistics. So, there might be contact details for the customs department, transport coordinators, etc. Knowing whom to contact will reduce issue-solving time, which might also be a KPI factor (some businesses may measure the time spent on issue resolution).
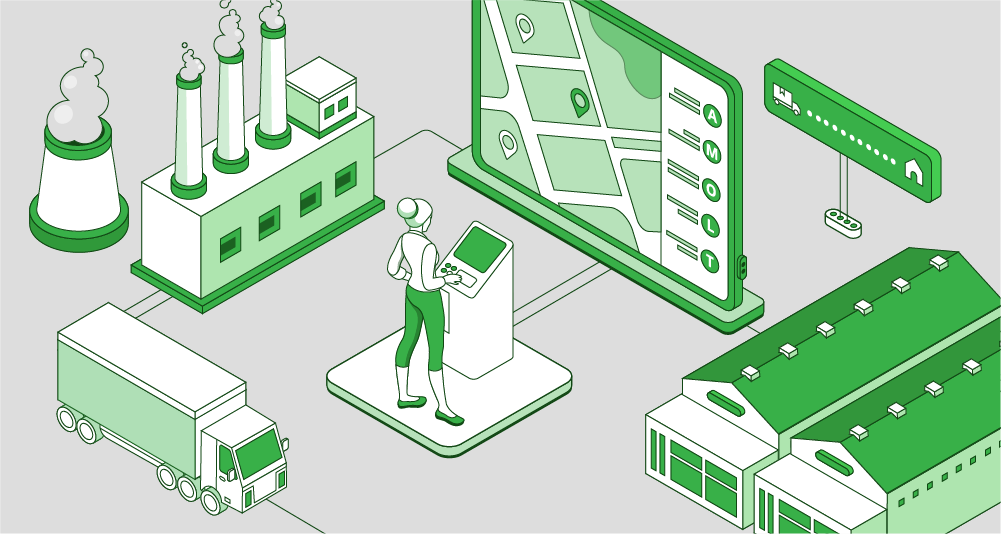
4. Integrations and its competitive advantages
Here are several reasons why integrations are necessary in logistics:
No more data silos. Integrations connect your systems and processes, providing a real-time view of everything from inventory, orders, and shipments to finances and more.
Lower error occurrence. Automation reduces manual data entry and minimizes errors. That's why it's important to connect departments and ensure that the warehouse is integrated with office administration.
Integrations boost efficiency. Internal integrations free up staff time, allowing them to devote their working hours to other tasks. You can achieve this by automating workflows.
Allow for stronger collaboration. Everyone has access to the same data. It enhances transparency and improves communication across departments, integrating the business more effectively.
Data-based smarter decisions. Integrations provide insights that optimize logistics through more informed decisions. By making decisions based on mutual cooperation and shared data, you can gain a competitive edge.
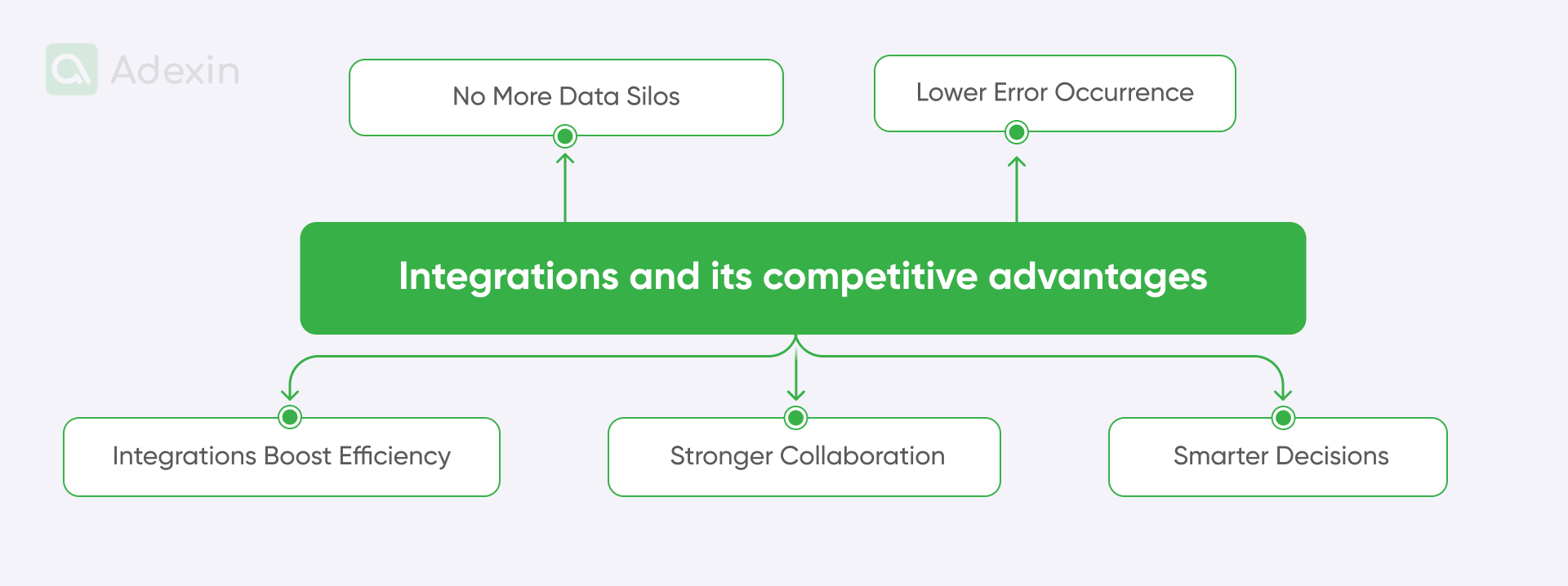
5. Delivery like logistics important factor
Delivery is one of logistics's core elements, and its importance is beyond discussion. Even if it seems closely related to transportation, in fulfillment logistics, you are responsible for everything. So, it's not just about preparing shipments but also about delivering them to end customers. Therefore, it's crucial to pay attention to this aspect.
To illustrate the importance of delivery in logistics, let's refer to small-pack (SP) shipping. Not many may know, but in 2024, the European leader in SP is DHL from Germany. They have entirely pushed away other businesses, such as those from France, by offering SP services widely. Despite its language barriers, it saw an opportunity to grow in a challenging market like France and provided global delivery for businesses that want to operate globally more effectively. It's worth noting that they genuinely understand the value of delivery in this market and have won more deals in 2024 than DPD or UPS recently in France, basically that their SP service is better and cheaper too. Since 2017 DHL has spent over 7 mln euros in a new depot near Paris, where in 2024 they also extended its services for specialized logistics.
6. Digital systems in logistics management
Nothing is more important nowadays than robust logistics systems in your business. Custom software development services have been available for many years to help you grow your business with tailored solutions. Here are the digital systems you may use in logistics:
Warehouse & transport for logistics management and supply chain. Warehouse management systems (WMS) and transport management systems (TMS) manage everything from inventory to routes, boosting efficiency and reducing errors.
Order management systems. The OMS System is the order maestro of your logistics, which helps with demand forecasting and managing everything from order placement to fulfillment.
Inventory management systems. IMS system is key for your logistics. It keeps track of inventory levels to avoid stockouts or overstocking.
Route optimization software for a more effective supply chain. Transport optimization is a key element in delivery. Start small with a route optimization system to find the most efficient routes, saving time and fuel.
Real-time tracking systems. These systems provide constant updates on the location and status of goods, benefiting both businesses and customers.
Labor management systems (LMS). This system optimizes the workforce by scheduling and allocating tasks for efficient labor use.
Supply chain management software. The SCCT system provides a holistic view by integrating all logistics functions for optimized operations. It helps also manage each third-party logistics company linked to your network.
Logistics CRM for customer and logistics management. A tailored customer relationship management system helps keep customers satisfied and loyal.
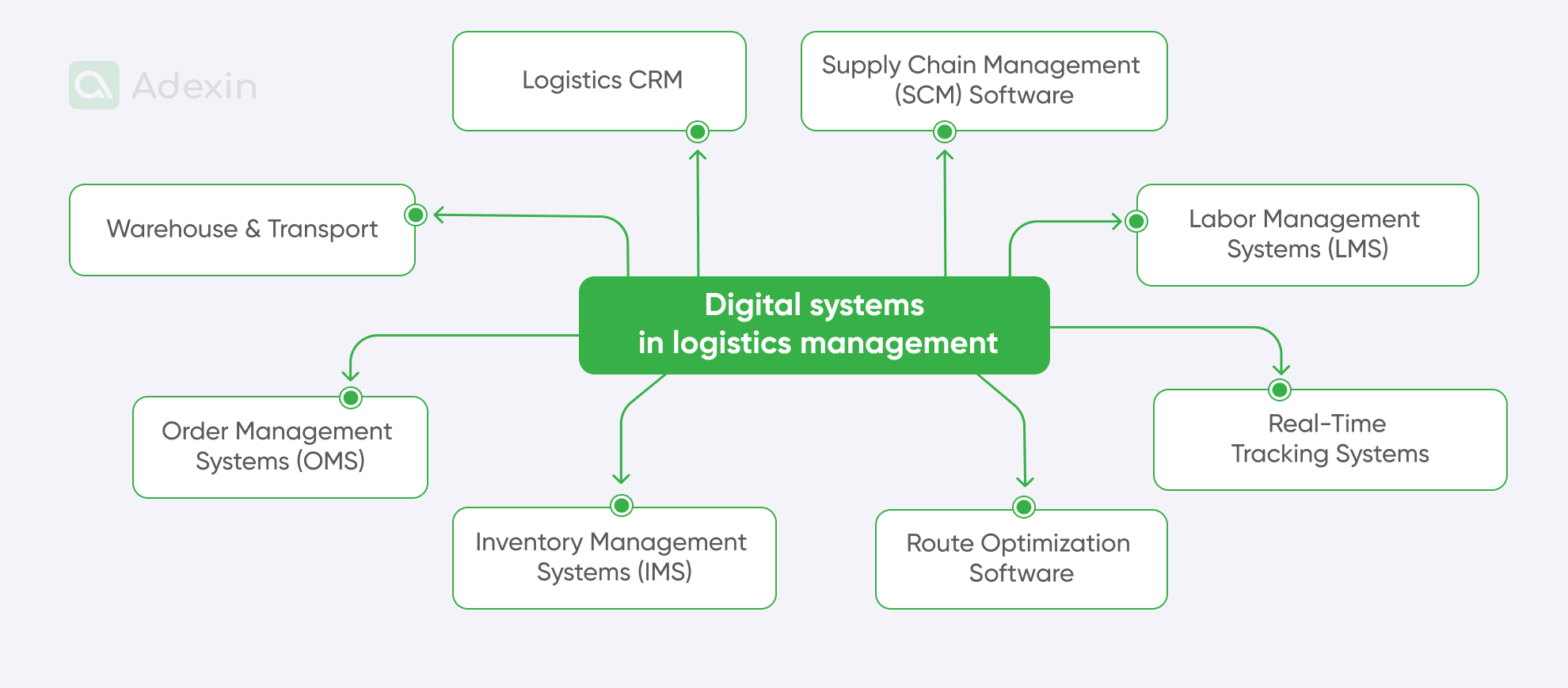
7. Hardware technology for business logistics
Hardware and technology, such as internal vehicles and robotics within automated warehouses, are critical in logistics today. Here are some essential hardware and technology elements you should keep in your warehouse to leverage your business performance effectively.
Warehouse essentials:
EPTs and forklifts. Essential for lifting and transporting pallets and heavy goods.
Conveyor belts. Automate the movement of goods, speeding up picking, packing, and sorting processes within the Value Added Service (VAS).
Barcode scanners. Essential mobile hardware for accurate and efficient inventory management and order fulfillment.
Mobile computers/tablets. Used by warehouse personnel for tasks like picking, receiving, and checking inventory levels.
Printers. Hand-carried by employees for printing labels, packing slips, and other essential documents. Despite future NFC tag technology, printers are still necessary.
Warehouse racking systems. Organize and optimize storage space for efficient product access.
Transportation hardware:
Trucks and trailers for supply chain transportation. The backbone of long-distance freight movement, available in various sizes and configurations for cargo needs.
Delivery vans for supply chain deliveries. Used for last-mile delivery within the supply chains, which can include deliveries in cities and towns and pallet cargo on longer distances.
Shipping containers. Standardized metal containers for secure and efficient transportation of goods by sea, air, or land.
Telematics systems. Hardware is installed in vehicles to track location, monitor performance, and optimize routes.
Additional hardware for future purposes:
Drones. Emerging technology for specific applications like inventory inspection or last-mile delivery in remote areas.
Robots and packing machines. These are used for automated tasks like palletizing, depalletizing, and sorting in warehouses. They can also seal pallets to protect them for shipping.
Security cameras. Monitor warehouse and yard activity for security purposes, which helps assess accidents and damages.
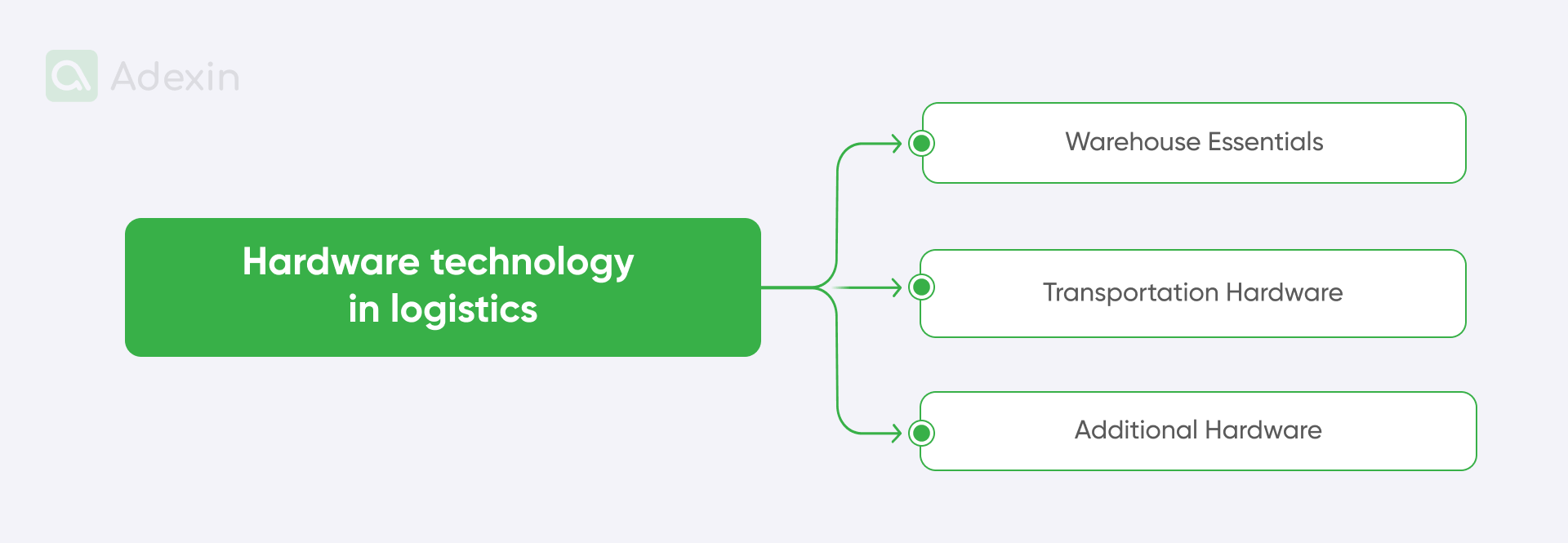
8. Logistics process and documents management
Focusing on the importance of logistics operations, workflows, and data management based on effective digital document management systems makes managing a warehouse much easier.
Let's jump directly to the examples of managing logistics processes. Within the warehouse, you have processes like receiving goods where logistics refers. However, this process often remains inefficient due to manual errors. These errors might include mixing pallets and items or incorrect labeling, which leads to goods being placed in the wrong locations in incorrect quantities. To improve this and get a well-organized logistics process, you need to assess the root cause.
You need to evaluate what happens with pallets at the receiving station. There might not be a clear area where employees can collect goods for error-free scanning. If there are too many goods on the table or if the area is messy, errors are likely to occur. Moreover, people at the receiving station often use paperwork. Paperwork like commercial invoices is usually filled out manually or handed over in poor condition. Suppose you have a document management system (DMS) that allows employees to scan barcodes on the invoices and recognize documents in the system. In that case, it is more likely that all data will be registered digitally. It allows receiving employees to ignore paperwork and achieve better results with receiving goods by looking at what they have on the desktop.
Are you in search of a reliable tech partner?
Adexin can help with advanced logistics solutions
Contact usSummary of the importance of logistic
Logistics is the backbone of any business, so don't neglect its important eight factors. The intricate network ensures that goods move smoothly from origin to destination. Its all means can impact everything from customer satisfaction to financial success. Today, we explained why logistics management deserves your full attention.
Effective logistics management is an investment that pays off. By focusing on the above-mentioned areas, you can ensure your business operates smoothly. Think about delivering exceptional customer service and gaining a competitive edge in the marketplace. Take control of your warehouse operations today with us. Explore how a DMS, TMS, and WMS can transform your receiving process and boost your bottom line. Contact us to learn more about the partnership for custom software development for the logistics industry.